Data Acquisition for Competition Vehicles
by Justin Callies, Clemson Automotive Engineering Graduate Student
- What is DAQ?
-
Data acquisition, or DAQ as it is commonly called, is a fairly simple concept. As the name implies data is acquired. This is the strictest definition of what these DAQ systems do but many are capable of much more. Data is acquired by various sensors which send digital or analog signals to a central processing unit where the information is at a minimum stored but usually processed in some way. These sensors sense things such as: temperature, pressure, position, force, and acceleration to name a few. In general the data is all digitized before being recorded in the central DAQ unit. From here this information can be processed and displayed by the unit itself or some peripheral display device such as a digital dash display. The information collected can also be beamed by radio antenna to a stationary computer located in the vehicle's pits.
For each sensor a different recording scheme is devised including sampling rates and resolution. Values which change slowly over time such as engine coolant temperature are usually sensed at 1 Hz. This low sampling frequency is due in part to the need to save space in the recording unit. More important values that fluctuate quickly such as suspension position or travel are often monitored upwards of 200 Hz. The resolution of measurements varies greatly as well due to the importance and scale of the measurement. Using the above two examples, coolant temperature would probably be sufficiently measured in increments of 1 degree while suspension travel must be measured much more precisely down to fractions of a millimeter. The variations in sampling rate and resolution as well as the number of measurements made are the deciding factors on what sort of processing power and memory capacity the DAQ system must be capable of.
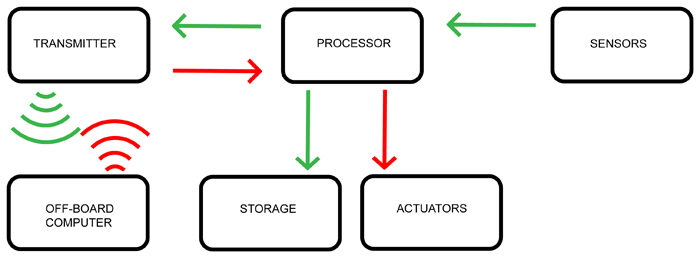
A Simplified Diagram of a Data Acquisition System
The diagram above shows the basic principles of DAQ but each block can look very different from system to system. The sensors can range from a single GPS position sensor to hundreds of sensors throughout the vehicle measuring everything from the position of the clutch pedal to pressure on aerodynamic elements. The central processing unit also varies differently usually depending on how powerful it needs to be to work with the type and number of signals it is receiving. The data recording and displaying is also a large variable. Currently this function is performed by everything from simple onboard memory units to PDA's to small networks of computers. The scale of the system depends greatly on the budget of the team implementing it as well as the type of vehicle and what point of development the vehicle is in.
- Why Use DAQ?
-
The primary use of DAQ in motorsports is in setting up and tuning the various systems of a vehicle. With these systems it is possible to go beyond the realm of the stopwatch and find out what effects, however minor, a changed setup parameter can have on a vehicle throughout a lap. This technique is invaluable when initially setting up a vehicle to understand how changes made to the car change its behavior. This technique can also easily be utilized to set a vehicle up for a given track through testing. The graphic below illustrates a few of the parameters that can be recorded by a DAQ system.
Some of the parameters monitored by DAQ
 |
In addition to making changes to a vehicle, DAQ systems can also be used to make changes to the driver. With the ability to break down driver performance to a lap-by-lap and even turn-by-turn basis it is possible to catch many mistakes that would not be evident inside the cockpit. The data that is acquired can also be a helpful communication tool between engineers and drivers in that it can graphically describe what the driver is feeling on the track.
One additional perk of DAQ is in fault finding. An engineer at a computer in the pits is able to constantly monitor performance parameters of the vehicle in real time. With this ability the engineer may be able to notice problems beginning to occur before they become serious and take action accordingly.
- GPS Based DAQ
-
As GPS and processor technology has advanced it has become possible to do amazing things with a simple receiver and processor. Some early GPS based systems could only sample at 1 to 5 Hz whereas current systems can handle 20 Hz. The resolution of the GPS receivers utilized has also increased allowing measurements within a few feet. This measurement may not seem accurate but the system is more interested in the precision of the GPS and takes many measurements over time. These location measurements can then be processed with software to get an accurate picture of speed and acceleration of the unit over time. When taking other variables such as vehicle mass into account it is also possible to get an idea of the horsepower of the vehicle. These systems are inherently limited in their uses but are great tools for driver development and due to their small price tags are a favorite amongst entry level teams and drivers.
Screen shot from GPS based DAQ analysis software (MaxQData)
|
The above graphic shows a screen shot from the MaxQData analysis software. Some of the most prominent features of GPS DAQ are featured. These include longitudinal and latitudinal acceleration as well as vehicle speed. This package is also capable of linking with video and audio recordings as well as overlapping runs or laps for comparison.
GPS systems are becoming more and more sophisticated. Many systems that are currently available have provisions for communication with other sensors including video cameras and even accelerometers. Some of these systems are similar to entry level conventional data acquisition setups in their capabilities but can still be significantly less expensive. In addition, because most GPS based packages are marketed to entry level teams and drivers, the user interface and software associated with the data acquisition tends to be much more user friendly.
- Sensors
- Position (controls, suspension travel), temperature (engine, tires), pressure (engine, tires, aerodynamics, brakes), accelerometers, wheel speed, engine speed, video and sound recorders, IR transponder, GPS receiver
- Actuators
- Digital dash display, warning lights, can utilize actuators associated with other systems such as engine control module
- Data Communications
- USB, ethernet, and radio transmitter for communications with off board computer
- typical systems can communicate with OBD, OBDII, CAN, FlexRay and other automotive Buses
- Conventional System Manufacturers (some with GPS systems)
-
Advantage Motorsports,
AiM Sports,
Competition Data Systems,
Edelbrock,
MoTec,
National Instruments,
Racepak Data Systems
- GPS Based System Manufacturers
-
G-TECH,
MaxQData,
NOLOGY,
RLC Enterprises Inc.,
Traqmate
- For More Information
- [1] Analysis Techniques for Racecar Data Acquisition, Jorge Segers, SAE International, 2008.
- [2] DAQs track race-car moves, MachineDesign.com.
- [3] Data Acquisition, Jerry F. Boone, Stock Car Racing.
- [4] Data Acquisition, Wikipedia.
- [5] Data Acquisition - A Helping Hand, John Hill, Stock Car Racing.
- [6] Ethernet Data Acquisition Improves Race Car Testing, Robert M. Winkler, Intelligent Instrumentation.
- [7] GPS Data, Racecar Engineer.
- [8] High-Performance Electronics for a Formula Race Car, National Instruments.
- [9] Precise GPS Sensing for High Performance Race Cars, Jonathan How and John Hansman, MIT.
|