Historically, diesel engines have used
the unit
injection system and the distributor/inline pump system. These older
systems had two main disadvantages: Firstly, they were cam-driven and
as a result the maximum pressure for fuel injection was only achieved
at high engine speeds. Secondly, they were limited in the number of
injections that they could deliver per combustion cycle. The
common-rail injection diesel systems build upon direct-injection
technology which allows fuel to be injected
directly into the combustion chamber. Common-rail injection systems use
a rail to store
the fuel at pressures in excess of 2,000 bar. This rail is shared
between all cylinders, hence the name common-rail. The common rail
allows a steady high-pressure supply of fuel independent of engine
speed. The transfer pump is electronically activated to maintain the
optimal pressure in the rail. Early generations of common-rail
injectors used magnetic solenoids to control the injection of fuel into
the cylinders. The latest generation of common-rail injectors use
piezoelectric inline actuators to control fuel injection. These new
actuators use hundreds of piezo-crystal wafers which expand very
rapidly when a current is applied. Piezoelectric inline actuators can
be integrated very close to the injector jet needle, providing
friction-free movement. These injectors allow for much more precise
fuel-injection times with shorter response times, as well as improved
atomization of the fuel.
Common Rail diesel injection systems have
several main advantages over older fuel injection systems. The high
pressure fuel supply from the rail allows for the fuel to be injected
quickly and at high pressure into the cylinders. This allows the
electronic diesel control unit (EDU) to very accurately control the
fuel injection. Such accurate control allows for up to 5 fuel
injections per combustion stroke ("pilot", "pre", "main", "after", and
"post" injections). The "pilot" injection, which occurs before ignition
allows for good fuel-air mixture. The subsequent "pre" injection
shortens the delay in the main injection, drastically reducing NOx
gases, vibrations and other noise. The "after" injection occurring
immediately after the "main" injection ensures that all particle matter
is burned. Finally, the "post" injection allows for control of exhaust
gas temperature, increasing after-treatment efficiency.
The overall result of using advanced
common rail diesel injection systems is an engine that operates more
efficiently, and is capable of outperforming it's gasoline-powered
counterpart. Virtually all previous downsides of operating a diesel
engine, such as noise, weak performance, vibrations and particle
emissions have been eliminated with common rail direct injection
diesel engine technology.
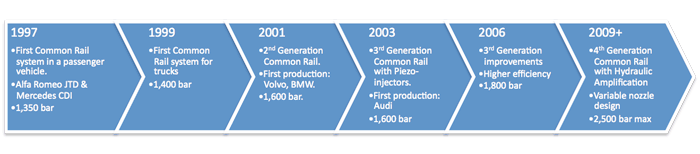
Common Rail Engine Names by
Manufacturer:
Audi: TDI
BMW: D-engines
Daimler: CDI
Fiat Group: JTD
Ford: TDCi Duratorq and Powerstroke
GM Opel/Vauxhall: CDTi and DTi
GM Daewoo/Chevrolet: VCDi
Honda: i-CDTi
Hyundai/Kia: CRDi
Land Rover: TD5
Mazda: CiTD
Mitsubishi: DI-D
Nissan: dCi
Peugeot: HDI or HDi
Renault: dCi
Subaru: TD
Toyota: D-4D
Volkswagen: TDI
Volvo: D and D5