Drive by Wire
by Sajit Pillai, Clemson Automotive Engineering Graduate Student
- Basic Description
There is a trend in the automotive industry towards eliminating mechanical and hydraulic
control systems and replacing them with electronic controls.
Many traditional mechanical components can be eliminated such as shafts, pumps, hoses, fluids, coolers, cylinders, etc.,
which reduces the weight of the vehicle and
improves efficiency. Electronic controls can also improve safety by facilitating more automated control functions like
stability control. They also enhance the flexibility of automotive systems, making
it easier to modify or upgrade vehicles. Electronic controls improve handling, enable better fuel efficiency and exhibit
shorter response times in emergency situations.
The complexity of the system control functions enabled by electronic systems can make vehicle performance more difficult to model. Integrating these complex systems, while achieving predictable, fail-safe performance represents a significant challenge for the automotive industry.
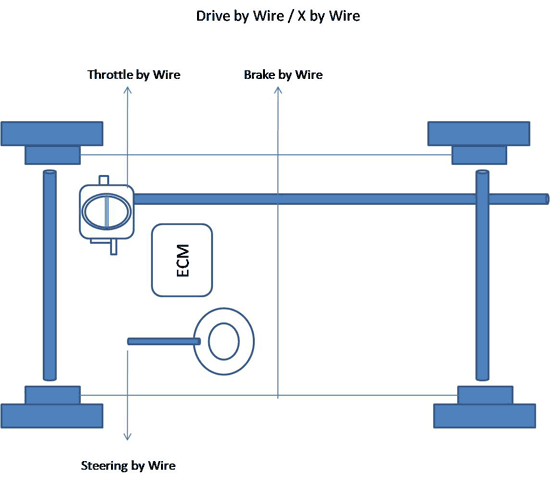
Drive by wire involves 3 main systems:
- Steer by Wire
-
Steer-by-Wire systems do not have a direct mechanical connection between the steering wheel and the wheels of
the vehicle. Instead, turning the steering wheel sends instructions to an electronic control unit, the control unit actuates
an electric motor that controls the steering angle of the wheels. Steer-by-Wire systems have the following advantages:
- Interior styling is easier and more versatile due to the absence of the steering column
- There is more space available in the engine compartment
- This system can be modeled and installed as a modular system
- Allows designs that prevent the steering wheel from rigidly impacting the driver during a frontal crash
- Driving characteristics can be monitored and the steering response can be easily adjusted
- Simplifies designs and lowers manufacturing costs
There are different models for steer-by-wire systems. Below is an illustration of one such system:
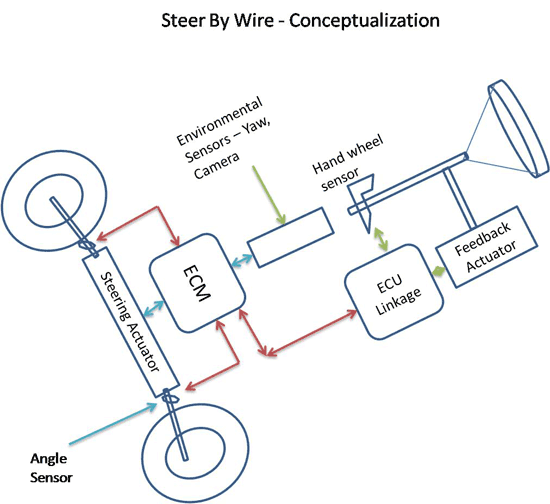
Steering wheel position and angle is measured by hand wheel sensor which is linked to ECM through an ECU
linkage which generates torque. Environmental sensors analyze environmental factors like Yaw, roll over position and
positions using cameras which are translated into the engine control module.
Using all these inputs tires are actuated using steering sensors and the angle of the steering rod is controlled
and monitored by the ECM.
- Sensors
-
Torque sensor, steering angle sensors, yaw sensor, wheel speed sensor, and wheel angle sensor
- Actuators
- Steering actuator, feedback actuator, pinion actuator
- Throttle by Wire
-
Throttle-by-wire is an automotive technology that is widely used on vehicles today. It replaces the
traditional throttle linkage (a cable between the accelerator pedal and the throttle) with an accelerator pedal position
sensor and an electronically operated throttle.
It provides several advantages over mechanical systems:
- Eliminates binding problems in mechanical linkages preventing the throttle from sticking
- Allows automated control of the throttle that helps to reduce emissions and improve fuel economy
- This system can be modeled and installed as a modular system
- Allows the ECM to integrate torque management with cruise control, traction control and stability control
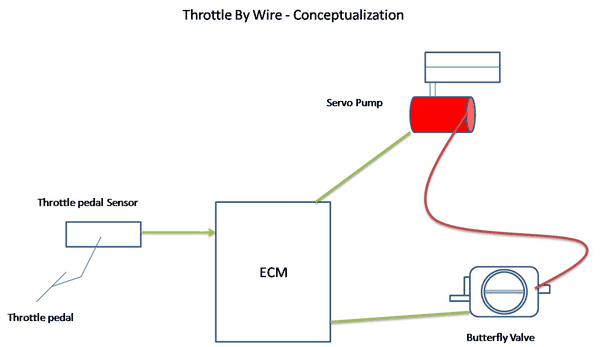
The accelerator pedal sensor senses the position of the accelerator pedal.
This information is conveyed to the ECM as a change in the electrical resistance. The ECM actuates a servo-motor,
which actuates the butterfly valve in the throttle assembly.
The position of the throttle is continuously monitored and the information is conveyed to the ECM using a feedback circuit.
- Sensors
-
accelerator pedal position sensor, throttle valve position sensor
- Actuators
- motor controlling throttle valve position
- Brake by Wire
-
Brake-by-wire is an automotive technology that completely eliminates traditional mechanical and
hydraulic components and replaces them with electronic sensors and actuators to control the brakes in vehicles.
Some of the advantages of brake-by-wire systems are:
- Reacts more quickly resulting in shorter stopping distance and time
- Loss of mechanical systems results in noiseless operation and elimination of vibration
- Lesser space consumed making the engine compartment and compact and helping in better space utilization
- Allows the ECM to integrate torque management with cruise control, traction control and stability control
- Reduces the weight of the overall system thus improving fuel efficiency
- Lack of mechanical power may facilitate the need the introduction of hybrid and fuel cells based vehicles
Brake-by-wire systems are still under development and cannot be found on passenger cars that are currently on the market.
One of several concepts for a brake-by-wire systems is illustrated below:
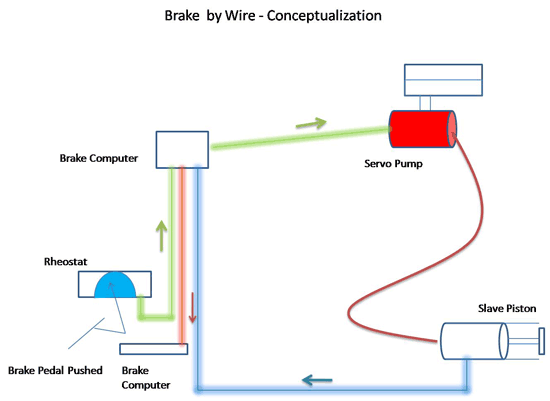
This systems consists of a rheostat that senses the position of the brake pedal.
This signal is interpretted by the brake computer, which generates signals to operate a servo pump.
The pump pressurizes the secondary circuit and brake fluid pushes against a slave piston that
activates the brake. The pressure is monitored and a signal is sent back to the brake computer,
which applies a mechanical force to the pedal as feedback to the driver.
- Sensors
-
brake pedal position sensor
- Actuators
- Servomotor/pump
The complexity of drive-by-wire systems is a concern to many automotive customers who
worry about the failure of software
and possible electronic malfunctions in sensors resulting in car accidents and passenger injury.
On the other hand drive-by-wire systems have been used by commercial aircraft for many years and have an
excellent safety record. Ultimately, the enhanced safety features and the other benefits of automated electronic
controls are expected to outweigh concerns about the complexity and reliability of these controls and drive-by-wire
systems will be widely used in automotive designs.
- For More Information
- [1] How Drive-by-wire Technology Works, John Fuller, HowStuffWorks.com, April 2009.
- [2] Drive by wire, Wikipedia.
- [3] Hy-Wire act: GM's drive-by-wire, fuel cell-powered prototype proves it's just a matter of
time before zero emissions vehicles are a reality, John Peter, Automotive Industries, Jan. 2003.
- [4] Drive-by-wire throttle: It's not so bad!, Michael Block, Orlando Examiner, Sep. 28, 2008.
- [5] SKF Drive-By-Wire NOVANTA Concept Car,
Larry Carley, AA1car.com, 2005.
- [6] Drive by Wire -
What will be its impact on future vehicles?, Rainer Kallenbach, Bosch, March 3, 2003.
- [7] 2009 VMX17 Throttle By Wire,
YouTube, Jan. 2009.
- [8] Electronic Wedge Brake,
YouTube, June 2008.
|