Water-Alcohol Injection Systems
by Brad White, Clemson Electrical Engineering Student
- Basic Description
-
Water alcohol injection systems are used to dynamically control the combustion temperature and octane rating of the fuel in an engine's combustion chamber. With gas mileage being a recent, major concern, modern and future engines are and will be pushing the limits of cylinder pressures in an effort to gain fuel efficiency. Having dynamic compression modifiers, such as variable valve timing and superchargers, as means of optimizing the fluid and combustion dynamics of internal combustion engines, the need has arisen to closely monitor and adjust the combustion process dynamically according to engine load.
An internal combustion engine runs at its optimum when the combustion exerts the maximum pressure on its pistons at their optimal rotational positions with respect to the crankshaft. As engine systems move more and more into the higher compression and supercharged realms, we are faced with a few problems. First, we must make sure the cylinder pressure doesn't spike too quickly during combustion or detonation can occur. This can be dynamically controlled with a metered, supplemental water-alcohol injection. This system works due to the high latent heat of vaporization of the water-alcohol mixture and the octane increase the system introduces into the combustion process. As the engine's load increases, raising combustion temperatures, the sup limen tal injection system removes some of the heat from the combustion process, increases the chemical octane rating of the fuel, and cools the pistons in a safe and efficient manor.
One challenge that occurs with the increase of cylinder pressures, is the need to increase the octane of the fuel. With rising fuel costs, it can be prohibitively expensive to purchase high octane fuel. However, higher octane is only necessary when the engine is under a high load. This is only a small fraction of the engine's duty cycle. Having a variable octane fuel optimizes fuel costs by increasing the octane only when the engine's running parameters demand it. It has been demonstrated that, with a water-alcohol injection system, more energy can be safely extracted from smaller, more efficient engines without the need to buy expensive, high octane gasoline.

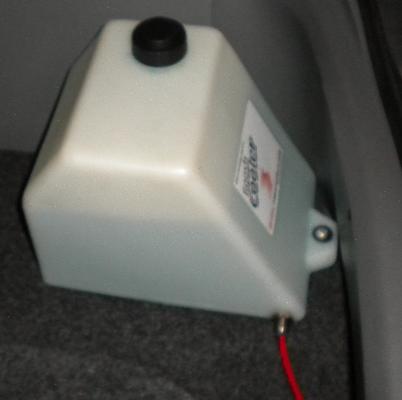
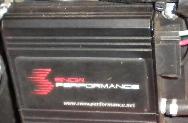
-
MAP Systems: Utilizing a Manifold Absolute Pressure sensor, Map Systems receive dynamic pressure feedback from the engine's intake manifold. The system's controller monitors this pressure and has set points that command injection rates based on manifold absolute pressures. For example: when a turbocharged car goes into high load, the combustion temperatures increase drastically. Sensing the boosted pressure in the intake manifold, the controller commands a pump to inject a highly pressurized water-alcohol mix into the air stream being ingested into the engine. This has a three-fold benefit. First, the heated air from the turbo is cooled by the water-alcohol mixture's high latent heat of vaporization; causing the air to be cool, dense, and oxygen rich. Second, the introduction of the water-alcohol mixture into the combustion chamber cools the chemical process. This reduces NOx emissions and reduces the probability of premature detonation. Third, as the mixture contains alcohol, the octane of the combustion chemical process is increased; further preventing early detonation and allowing for more aggressive ignition timing and leaner base fuel maps. These systems work best on engines with centrifugal type superchargers.
MAF Systems: Systems that operate in proportion to a Mass Air Sensor signal, are similar to the MAP reference systems. Rather than calculating an engine's load from a MAP signal, the controller calculates the load as a function of the mass of air that is being induced into the engine's intake manifold. This is accomplished by sampling the MAF return voltage, with an simple high input impedance operational amplifier circuit, and sending sending a filtered voltage signal to the water-alcohol injection controller. The controller compares the MAF voltage to the voltage references and calculates the engine's load. This system has the advantage of calculating the load before the air reaches the cylinders, while the MAP reference system calculates load at the precise time the air is reaching the cylinders, hence the MAF reference systems minimizes the probability of early detonation. These systems work best on high compression naturally aspirated, or positive displacement supercharged engines.
- Sensors
- MAP Sensor, MAF Signal Comparator
- Actuators
- High pressure pump, Injector nozzle
- Data Communications
- Control unit communications: Self contained
- Manufacturers
- Cooling Mist, AEM, Snow Performance,
- For More Information
- [1] Water Injection (Engines), Wikipedia.
- [2] Methanol, Wikipedia.
- [3] Water Injection, YouTube, Sep. 15, 2009.
- [4] How Water/Methanol Injection Works & How It Makes Horsepower in Gas Engines, YouTube, Mar. 28, 2011.
|