Acceleration Sensors
- Basic Description
-
Linear acceleration sensors, also called G-force sensors, are devices that measure acceleration caused by movement, vibration, collision, etc. All acceleration sensors operate based on a simple principle in which Newton's second law of motion is applied to a spring-mass system. A mass is connected to the base of the acceleration sensor through an equivalent spring. Since the force between the mass and base is proportional to the acceleration of the mass and the relative distance between them has a linear relationship with the force due to the spring, the acceleration can be calculated from a measurement of the relative position of the mass or force on the spring as it varies with time. Generally, the most common types of acceleration sensors include: piezoelectric, piezoresistive, variable capacitance and variable reluctance.
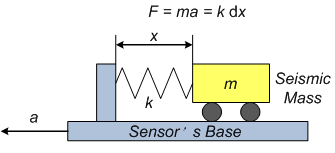
Piezoelectric
A piezoelectric acceleration sensor utilizes the piezoelectric effect to measure the relative distance between the mass and sensor's base, and then represents the acceleration in terms of an output voltage. Quartz crystals are occasionally used as sensing elements. But usually, ceramic piezoelectric materials such as barium titanate, lead zirconite titanate (PZT), and lead metaniobate are used. Piezoelectric acceleration sensors are widely used due to their compact size and light weight, but they cannot be used to measure steady-state accelerations.
Piezoresistive
In a piezoresistive acceleration sensor, a piezoresistive material is positioned so that it is deformed by the position of the mass changing its resistance. This type of acceleration sensor generally has a small size, large signal amplitude and good linearity, but it can be sensitive to variations in temperature. Piezoresistive sensors can be used to measure both steady-state and dynamic accelerations.
Variable Capacitance
A variable capacitance acceleration sensor uses changes in capacitance caused by a displacement in the mass to detect its position. The sensing element usually used here is an air-damped, opposed plate capacitor. These types of acceleration sensors have good sensitivity, linear output, good DC response, low power dissipation and low temperature sensitivity. One drawback of variable capacitance sensors is that they can be susceptible to electromagnetic interference.
Variable Reluctance
A variable reluctance acceleration sensor uses changes in the inductance of a coil caused by a displacement in a mass made of magnetic material to detect the position of the mass.
In most acceleration sensors, the spring is not a coiled wire spring, but it is something that tends to restore the mass to its initial position. Some sensors employ pendulums or diaphragms in place of the spring.
Servo force balance sensors operate in a closed-loop manner. These sensors monitor the balance of forces between the mass and spring and keep them in an equilibrium state. This mechanism minimizes the errors caused by nonlinearity of the spring but increases the cost.
MEMS Acceleration Sensors: Acceleration sensors based on MEMS (MicroElectroMechanical Systems) technology are becoming increasingly popular in automotive systems. MEMS devices are relatively small and rugged compared to other technologies. They are made by etching tiny mechanical structure in silicon wafers where they are readily integrated with system electronics.
In MEMS acceleration sensors, the sensitive element is a comb-like structure of differential capacitors arranged in parallel on a beam (forming the seismic mass) supported by springs etched from the silicon substrate. The differential capacitor forms a capacitive half-bridge driven by a high frequency square wave generator. When acceleration is applied perpendicular to the seismic mass, the differential capacitor is mismatched and a non-zero voltage appears on the central plate. This signal is preamplified, demodulated, amplified and output as a voltage proportional to the applied acceleration.
Automotive Applications of Acceleration Sensors:
- Collision detection and airbag deployment: To measure intensity of collision and signal to initiate airbag deployment.
- Electronics stability programs and control: Measures acceleration along various axes, (e.g. forward, braking and cornering accelerations, to compute relative movements and regulate them).
- Antilock braking systems.
- Active suspension systems: Measures longitudinal and lateral accelerations as well as vehicle roll characteristics to change damper characteristics accordingly.
- Hill descent/hold control: Measures vehicle inclination and speed to regulate system.
- Monitoring Noise,Vibration and Harshness.
- Vehicle navigation systems to determining vehicle location, speed, etc.
- Manufacturers
-
ÅAC Microtec, Altheris, Analog Devices, Bosch,
Continental, CTC, Freescale, GE, Honeywell, Kionix, Memsic, Mitsubishi Electric,
McLaren Electronics, Murata, Omega, Panasonic, PCB, Rieker, Sensata, Silicon Designs, STMicroelectronics,
TRW
- For More Information
- [1] Accelerometer, Wikipedia.
- [2] STMicroelectronics MEMS Accelerometers,
YouTube, June 8, 2009.
- [3]
MEMS Accelerometers, Matej Andrejasic, 2008. (pdf)
- [4] Optical Accelerometer Heralds New Class of Motion Sensors, Optics.org, Oct.29, 2012.
- [5] Accelerometers and How they Work,Texas Instruments. (pdf)
- [6] Introduction to Accelerometers,Omega Engineering website.
- [7] A Beginner's Guide to Accelerometers, Dimension Engineering website.
- [8] MEMS Accelerometer, Silicon Designs website.
- [9] Harvard's Four-Cent Paper Accelerometer, Popular Science, Feb. 14, 2011.
- [10] How a Smartphone Knows Up from Down (Accelerometer), YouTube, May 22, 2012.
|