Torque Sensors
- Basic Description
-
A torque sensor, which is also called a torque transducer, is an instrument for measuring and monitoring the torque on a rotating system, such as an engine crankshaft. Torque sensors convert a torsional mechanical input into an electrical output signal. Torque is measured by sensing the shaft deflection caused by a twisting force. Since L, G and Ip, defined in the image on the right, are properties of the shaft, the torque value can be determined by measuring the rotation angle of one end of the shaft relative to the other. There are two types of torque to be measured, static torque and dynamic torque.
Strain gauges are the most common way to measure the torque applied to a shaft. When measuring the dynamic torque on a rotating shaft, slip rings, wireless telemetry and/or rotary transformers must be used to power the strain gauge bridge and receive the signal. Although strain gauge torque transducers provide high accuracy, their high cost and bulkiness limit their application. In addition, these transducers tend to require high levels of maintenance, making them unsuitable for mass integration into manufacturing systems.
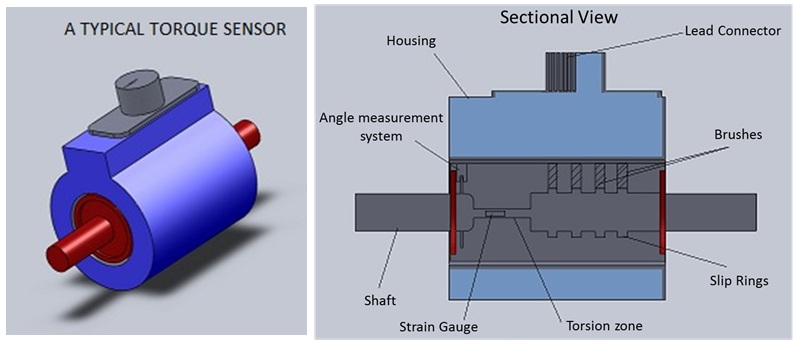
Another approach for measuring torque is employing proximity and displacement sensors. These sensors detect torque by measuring the angular displacement between a shaft's two ends. By fixing two identical toothed wheels to the shaft at a distance apart, the angular displacement caused by the torque can be measured. Proximity sensors or photocells located at each toothed wheel produce output voltages whose phase difference increases as the torque twists the shaft.
A magnetoelastic torque sensor can also be used to measure the torque applied to a shaft. This sensor detects changes in permeability by measuring the variation in a magnetic field. The key components of a magnetoelastic sensor are a thin ring of steel tightly coupled to a stainless steel shaft forming a magnetic circuit. A magnetometer converts the magnetic field into an electrical output signal that is proportional to the torque being applied.
Surface Acoustic Wave (SAW) torque sensing is an emerging technology for wirelessly sensing and transmitting values of torque. SAW torque sensors are resonators that have a resonant frequency that changes with applied torque. These sensors are passive devices that can be excited with an applied electromagnetic interrogation pulse. A receiver then wirelessly senses the resonant frequency and calculates the torque.
- Manufacturers
-
ATI Industrial Automation, Bourns, Continental, Dorman, Futek, HBM, HITEC, Honeywell, Interface, Kistler,
Lorenz Messtechnik, Measurement Specialties, Methode Electronics, Michigan Scientific, Omega, PCB Piezotronics, S. Himmelstein, Sensor Technology, Sushma, Teledyne, Transducer Techniques
- For More Information
- [1] Evolution and Future of Torque Measurement Technology, Lorenz Messtechnik website.
- [2] The Basics of Torque Measurement, Sensor Development Inc. website. [pdf]
- [3] Torque Sensor Applications , Futek website.
- [4] The Torqstar Torque Sensor ,
Sensorland.com.
- [5]
SAW Torque Sensors for Automotive Applications Help to Improve Fuel Efficiency, Schott AG press release, June 1, 2009. [pdf]
- [6] Torque Sensors,
YouTube, July 13, 2010.
- [7] Non-contacting Torque Sensors Aim at Power Steering Applications, C. Hammerschmidt, EE Times, Sep. 11, 2013.
|