Competitive Advantage
Top-level industry executives meet with University officials for an unprecedented forum.
FROM THE DEAN
College of Engineering, Computing and Applied Sciences has a distinct geographical advantage. We are at the epicenter of the Interstate 85 corridor, a vital artery connecting five states in the fast-growing Southeast. This area, with its $1.9-trillion regional economy, is quickly becoming a national leader in advanced manufacturing.
Each job is more than a number or a salary. It’s a ticket to attaining the American dream. It’s a family that can pay its mortgage, put a car in the garage and send its children to college. It’s an individual who can make a positive contribution to society. It’s the foundation of an economy that supports vibrant cities with opportunities for arts and education. Put simply, all of us profit when our companies do well.
Against this backdrop, in the fall of 2018 Clemson University called together some of the Southeast’s most influential executives for a forum on advanced manufacturing. We asked them to give us our “homework” for the year; specifically, what research and education programs their companies needed to sustain the region’s success for years to come. In a wide-ranging conversation, the executives described the challenges they face and spoke about the value they place on internships, co-ops and initiatives that promote diversity. We are now working to shape programs that will directly respond to these needs.
In this issue, we feature some of our advanced manufacturing programs already in place. Michael Carbajales-Dale heads a program that sends students into advanced manufacturing plants to conduct assessments that have saved companies tens of thousands of dollars in energy costs. Elizabeth Gendreau, a master’s student working with Josh Summers, illustrates the unique advantages for students who participate in our study abroad programs. Cole Smith and Laine Mears describe the cutting-edge educational opportunities for students in our graduate programs made possible by the National Science Foundation Research Traineeship Program. As part of TIME for Robotics, a group of researchers is creating an advanced manufacturing curriculum rooted in personalized learning and virtual reality.
On a more individual level, Yue “Sophie” Wang’s research focuses on the collaboration between robots and people in the workplace, while Srikanth Pilla and his Ph.D. student, Saeed Farahani, have created a new streamlined manufacturing process. Jianhua “Joshua” Tong is using 3D printing and laser processing to create devices that convert electricity to hydrogen as a way of storing energy. These programs and this research are creating the technology and workforce that will play a key role in the future success of advanced manufacturing in South Carolina and beyond.
This issue also features alumni who have distinguished themselves both in their careers and through their generosity to the college. Ron and Jane Lindsay have given $1 million to fund scholarships, professorships and other needs of the college.
In another story, we meet Vanessa Ellerbe Wyche, who has made history as the first African-American to serve as deputy director of NASA’s Johnson Space Center.
The college is afforded with advantages that position us to have a direct, positive impact on the world: We have a strategic location, top talent and the world’s best alumni, and I invite you to join us as we leverage them to shape the future.
Anand Gramopadhye, Dean
College of Engineering and Science
LEADERSHIP
Panelists for the Advanced Manufacturing Forum were (L to R): Dochul Choi, senior vice president, global business and technology strategy, Samsung Electronics America; Scott Clark, chairman and president of Michelin North America; Knudt Flor, president and CEO of BMW Manufacturing; Tim Hardee, president of the South Carolina Technical College System; Mike Mansuetti, president of Bosch North America; and Wolfgang Rubrecht, vice president, strategy and business development at Siemens.
COMPETITIVE ADVANTAGE
Advanced manufacturing executives, working toward a shared vision for South Carolina’s economy, call on Clemson University to help develop the workforce and energize innovation.
By Paul Alongi
Presidents and vice presidents from some of South Carolina’s most influential companies gathered in Greenville this fall for an unprecedented forum on how Clemson University can best partner with industry to meet the needs of its advanced manufacturers.
University officials are now working to create the research, education and outreach partnerships that will ensure advanced manufacturing remains successful in the state for years to come.
Clemson University President James P. Clements said the number of high-level executives who participated underscores the importance of higher education to the success of advanced manufacturing in South Carolina and beyond.
“Higher education plays an important role in moving new technologies to the marketplace and in creating a well-qualified workforce,” he said. “This forum provided a great opportunity to establish a dialogue with some of the state’s most influential advanced-manufacturing leaders. We look forward to continuing an important conversation that will ultimately lead to new and improved programs, helping promote job creation and economic growth.”
The forum was the latest in a series of Clemson efforts to support and accelerate advanced manufacturing. The organizing force behind those efforts is the Clemson University Center for Advanced Manufacturing, led by director Mark Johnson.
For states along the Interstate 85 corridor, manufacturing is a cornerstone of a combined $1.9 trillion regional economy, accounting for more than 1.57 million jobs in Alabama, Georgia, North Carolina, South Carolina and Virginia, according to the National Association of Manufacturers.
South Carolina alone has 239,500 manufacturing jobs, which is 11.7 percent of nonfarm employment, the association found.
Ideas to ensure future success ranged from more internships, co-ops and diversity to a greater emphasis on data analytics and artificial intelligence. Several of the executives said they were up against tech companies, such as Google and Facebook, in competition for computer-savvy employees.
Even as technology rapidly changes manufacturing, several of the executives agreed that human beings will remain the most important component for success. Flor said BMW has hired 150 Clemson graduates since building its Greer plant, the largest in the company’s network.
“We have very, very good experience with this, but we need to come to the next higher level because we want to be the benchmark in production,” Flor said. “For this reason, we need the best people, and this is why we are here.”
Dochul Choi, senior vice president, global business and technology strategy, Samsung Electronics America, said Samsung believes it is innovation and university partnership that will help ensure success at its home-appliance manufacturing facility that opened in 2017 in Newberry.
“This is serious business we’re talking about,” he said. “We have committed to investing $380 million over the next several years and have already hired and trained 650 employees. But to reach our full potential, we are going to continue to invest and will need a strong and competent workforce.”
Scott Clark, chairman and president of Michelin North America, asked educators to help market manufacturing, which he described as dynamic, clean, safe and automated. He called on educators to go beyond teaching technical skills and to help prepare students for a fast-paced environment that requires collaboration. Educators can also help create a more diverse workforce, Clark said.
“We need that because our customers are diverse. We need it to win. Make sure that you’re bringing diversity into your institutions so that we have access to diversity.”
The ways big data, artificial intelligence and other technology are changing manufacturing emerged as a key theme.
Mike Mansuetti, president of Bosch North America, said that an engineer at Bosch’s Anderson plant recently used new ways of analyzing data to reduce the scrap rate by 40 percent. Everyone should be reading books about artificial intelligence, which can be used for the good of manufacturing and problem-solving, he said.
“This is not just the engineering folks,” he said. “We’re talking about all aspects of a manufacturing plant,” including logistics, control and human resources.
Wolfgang Rubrecht, vice president, strategy and business development at Siemens, said software should become a prime topic in the education of mechanical, electrical and industrial engineers.
“Those are the people who recognize the interesting aspects of manufacturing and are willing then to go into these jobs,” he said. “If you’re a computer science graduate, you’re probably more inclined to go to Facebook or to Google. But if you’re a mechanical engineer or industrial engineer and you have an interest in manufacturing, you will deploy these software skills in manufacturing.”
Tim Hardee, president of the South Carolina Technical College System, said skilled people are needed for advanced manufacturing in South Carolina, a state that turns out more than 100,000 tires a day, 12 Dreamliners a month and 400,000 BMWs a year.
That output places enormous demand on the state’s workforce, a challenge Clemson is combatting directly. Hardee said he is looking for students who start in the technical college system because of its affordability but have the academic skills to succeed at Clemson.
“What that leads to is advanced manufacturing in the state of South Carolina moving to the forefront,” he said. “There are 5 million South Carolinians. We want them to have those great jobs. How we do that is having technical college people come in through the technical college system, moving to Clemson and becoming great engineers there.”
The forum was called “A Vision for Advanced Manufacturing in the Region 1.0: A Framework for Competitive Growth.”
It focused on a plan for action at Clemson and beyond, said Johnson, who is also the Thomas F. Hash ‘69 SmartState Endowed Chair in Sustainable Development in the College of Engineering, Computing and Applied Sciences.
“This forum was a critical step,” he said. “Private sector partners and educational institutions are working together to build on this framework to ensure the region is successful in advanced manufacturing for years to come. Clemson’s ‘homework assignment’ from these executives is to build cooperation between companies, colleges, universities and government working toward a shared goal: a stronger, more prosperous advanced manufacturing community. ✲
PROGRAMS: Clemson’s Industrial Assessment Center
FUTURE CONNECTIONS
Students work alongside career manufacturers at Clemson’s Industrial Assessment Center, improving plant efficiencies while building professional networks.
By Paul Alongi
The whirring of pneumatic wrenches filled the Komatsu plant in Newberry, South Carolina, as four Clemson University students made their way past workers assembling yellow forklifts. A woman noticed the students’ bright orange hard hats and greeted them with the two words every Clemson diehard likes to hear.
“Go Tigers!”
It was a warm welcome for a team that had made the 90-minute drive from campus to help Komatsu assess how it could reduce its energy use.
The students were from Clemson’s Industrial Assessment Center, a program that takes engineering education out of the classroom and into manufacturing plants. The center’s energy-use assessments are free and come with the potential to save each participating company tens of thousands of dollars.
With 17 site visits in its portfolio, the center is now charging into its third year with a total of 11 students eager to leave their mark on the world. Among them is Lakshana Nagaraj, who is working toward a master’s degree in industrial engineering.
“I think energy saving is the ‘in’ thing right now,” she said. “There is a lot happening with climate change and the environmental effects. We need to do something about it. This is the first step. Everyone can make an effort toward energy saving.”
The center’s teams have been fanning out across the state for two years to assess small- to mid-sized manufacturers. They have recommended ways to save an estimated $1.6 million in energy, with each company saving an average of more than $25,000 per year.
The assessments also have helped companies reduce their environmental impact, while giving students real-world experience and connecting them with employers, said Michael Carbajales-Dale, the center’s director and an assistant professor of environmental engineering and earth sciences.
“The way some of these companies talk with students — it’s almost like an interview,” Carbajales-Dale said. “They see students as potential new employees. A lot of companies realize the good training that IAC students get.”
Clemson launched the center in October 2016 after receiving nearly $1.3 million from the U.S. Department of Energy’s Office of Energy Efficiency and Renewable Energy.
It is among 28 Industrial Assessments Centers nationwide that provide no-cost assessments to small- and mid-sized companies. In an October 2018 report, the White House cited the centers as an example of a federal program that “contributed to the progress in manufacturing education, training and workforce development.”
To be eligible for an assessment, companies must have fewer than 500 employees at the plant site, gross annual sales below $100 million, and have annual energy bills between $100,000 and $2.5 million.
The plant must be within 150 miles of an Industrial Assessment Center. Most of the Clemson assessments take place in South Carolina, although the center’s coverage area also includes parts of Georgia, North Carolina, Tennessee and southwestern Virginia.
Clemson’s center is made up mostly of undergraduate engineering students who work up to 14 hours a week as paid interns for as many semesters as they are available.
Students work under the supervision of faculty members, including Carbajales-Dale. Phil Litherland, the assistant director of the center, helps lay the groundwork prior to site visits.
On the Komatsu site visit, the team looked for ways to save money throughout the plant from the cranes and compressed-air system to the lighting and heating.
Ben Snelson, an industrial engineering major, said that when he first started doing assessments, he hardly knew what a manufacturing plant looked like. By the time he went to Komatsu, he had been on several site visits and had an eye for energy efficiency. It was good that many of the workers were using cordless drills powered by batteries and saving the compressed-air drills for the bigger jobs, he said.
“When you have a ton of running tools and a lot of lines and a lot of moving things, the hoses can get leaks really easily,” Snelson said. “They’re using batteries, so it’s cheaper. Compressed air is expensive.”
All signs point to a bright future for the center. Carbajales-Dale said he was working to find new sites to assess and for new ways of connecting clients with various pools of money, such as low-interest loans and rebates, that may be available to help make energy-efficiency upgrades.
“It’s not just in-and-out,” he said. “We’re connecting them with resources that can help get the job done.” ✲
PROGRAMS: NSF Research Traineeship Grants
THINK BIG
Two grants, funding convergence research programs at Clemson, are proving transformative for the University’s STEM graduate education.
By Paul Alongi
Graduate students are researching some of society’s most pressing challenges and learning to collaborate across disciplines in two separate programs that have positioned Clemson University at the forefront of a nationwide effort to transform STEM graduate education.
One of the programs is led by Cole Smith, associate provost for academic initiatives, and one is led by Laine Mears, the BMW SmartState Chair in Automotive Manufacturing.
Smith and Mears are placing a strong emphasis on convergence research, one of the National Science Foundation’s “10 Big Ideas.” The thought is that research should be driven by specific and compelling problems and that specialists from a wide range of disciplines should come together to solve those problems.
For the engineers involved, it means they no longer work only with other engineers. On any given day, they could be collaborating with students and faculty members in political science, psychology, education and a variety of other disciplines.
Both programs are open to master’s and Ph.D. students, and each program is funded by its own $3 million grant from the National Science Foundation Research Traineeship Program.
The National Science Foundation has distributed 149 of the grants to institutions in 41 states, the District of Columbia and the Virgin Islands, per the foundation’s website. South Carolina has two — both at Clemson.
The program is “designed to encourage the development and implementation of bold, new, and potentially transformative models for science, technology, engineering and mathematics (STEM) graduate education training,” according to the foundation.
In the program that Smith leads, students learn to root out vulnerabilities in a wide range of infrastructure systems that rely on each other to provide society’s basic services, ranging from clean water and food to power and communications.
In Mears’ program, students are learning to bring together human workers and internet-connected machines that are often loaded with sensors, generating massive amounts of data. His program is the first in the nation to match graduate students with technical college students on an assembly line built for research.
About 25 students were enrolled in the Smith-led program, which launched in 2016. Mears, who received his grant in September 2018, expected to have 10 students by fall 2019 and to later grow the program to about 25.
Graduates continue to get a traditional degree in their home departments — such as industrial engineering or automotive engineering — but also receive a special designation showing they have participated in a cutting-edge graduate program.
Smith and Mears sat down with IDEAS magazine at the end of the fall 2018 semester to discuss the National Science Foundation Research Traineeship Program, often called NRT for short, and what’s coming next.
What is an NRT grant and what makes it special?
Mears: It’s a grant from the National Science Foundation to establish new ways of educating graduate students. It’s a way to look at convergence research. It involves multidisciplinary research projects and creating new, creative ways of educating people in how they should be thinking about these coupled problems, which is really important right now. All signs are pointing toward getting away from the siloed way of educating students. We want to get them into open-ended problems, multi-disciplinary problems, and help them not become a master of everything but at least touch the other domains so they know how their decisions affect other domains.
Smith: And it’s very important that students see teamwork as an integral part of their education through this. It’s not just a matter of being co-advised by a few different professors, but also interacting with different students from other majors who think about problems completely differently from how they might. The program also gets them to a point where they can innovate their own research questions.
“We’re looking at technologies that connect people, provide data from people and give data immediately back to people. We’re looking at augmented reality, virtual reality, and haptic-types of feedbacks, and how those can map into systems of manufacturing. We’re running research projects and inventing new things.”
– Laine Mears
It’s not just being pushed by the adviser or the adviser and the students in their own silo, but also talking to a student from policy or planning or political science. They bring up issues that an engineer might never have thought needed to be addressed in the first place.
Clemson has two NRT-funded graduate programs. How prestigious is that?
Smith: I’d say it’s a very prestigious setting we’re in right now. I don’t necessarily think two is the limit on this either. There are more opportunities, because a lot of the faculty who we have brought in recently have this interdisciplinary mindset. It’s not a surprise that we’ve been successful.
Has any goal been set for Clemson to get a certain number of NRT grants?
Smith: We do want to be major players in all of the funding opportunities that are out there, whether that’s an engineering research center, or whether that’s an NRT. Clemson is a top university, a premier research university. We should be getting these types of research grants and we’re showing that we belong in there right now.
Mears: A very wise mentor said to me when I started the academic side to my career, “Think big.” And so, we’re going after these bigger programs, these longer-lasting programs, and they’re really giving us a nice base to build off of. We’re building smaller, industrial-type of grants over the top of this. It’s a nice bassline, and then you’re riffing on top of that with smaller grants. You can be a little bit more adventurous with the kinds of things that you try.
Does having two NRTs make it easier to get a third and fourth and so on?
Mears: I see some benefits to having two. We’ve already been talking with the personnel over in Cole’s program about what we need to watch out for and the things we need to be measuring.
Smith: We learn from theirs, too, because they bring this infusion of new ideas that we want to adopt within our own NRT. We’re building up some cultural knowledge of how you run these programs and some of the great ideas we didn’t think of within our own.
Could each of you tell me about the graduate programs you’ve established with NRT funding?
Smith: Ours is in resilient infrastructure and environmental systems. The idea is that when you want to try to address the resiliency of truly interconnected complex systems, you can’t come at it from one discipline. You have to understand where IT systems underlie these complex, integrated systems. You have to understand what the engineered aspects of them are. But you also have to understand public policy implementation and implications. You have to understand the psychology and how people will interface with these systems. It is an enormously complicated problem to deal with in a comprehensive manner. Those resilient infrastructures may be the entire food system we have in the country, or it might be coupled power and communication systems.
Modeling them is a very difficult undertaking because you have to be an expert at so many different things, and you also have to understand the connections that lie in between those systems. But that’s only half the battle, because even as you model these systems, you’re trying to improve them. You’re trying to optimize them. You’re trying to figure out with limited resources how you build the most robust system that can effectively serve the needs of diverse populations who are going to interface with technology in far different ways. It’s an amazingly rich area for research. That’s why we have so many people from so many different disciplines — pretty much all the different engineering disciplines and then many folks outside of the College of Engineering, Computing and Applied Sciences. Disciplines include mathematical sciences; planning, design, and the built environment; economics; and certainly computer science. These are all core competencies.
“When you want to try to address the resiliency of truly interconnected complex systems, you can’t come at it from one discipline. You have to understand where IT systems underlie these complex, integrated systems. You have to understand what the engineered aspects of them are. But you also have to understand public policy implementation and implications. You have to understand the psychology and how people will interface with these systems.”
– Cole Smith
How about yours, Dr. Mears?
Mears: We’re working on this convergence of the industrial Internet of Things — interconnected machines and software systems — and people who use them. The way it stands now is that this interconnected, networked Internet of Things spits information out, and people take that information and go make decisions. We’re working to bring a more holistic network and make this Internet of People and Things. So, we’re looking at technologies that connect people, provide data from people and give data immediately back to people. We’re looking at augmented reality, virtual reality, and haptic-types of feedbacks, and how those can map into systems of manufacturing. We’re running research projects and inventing new things. That’s what’s happening right now. And we’re looking at the industrialization side, which means asking how we can commercialize the things that we’re inventing. How do we find companies or create companies that make these things and that could get them out into the industrial network?
What else do you think readers should know about Clemson’s NRT-funded graduate programs?
Smith: This kind of research is accessible to students. They understand that there is real impact in what they are doing. It’s an immediate impact. It’s not a theoretical construct, which then leads into other things, which eventually appears on the market. What we’re doing with these NRT programs, it’s easy to see how students would want to be involved with this. One of the major problems that all academics face right now is broadening that pipeline within graduate education, and these NRT programs are absolutely essential. ✲
PROGRAMS: Study Abroad
PROFITANT DES OPPORTUNITÉS
Elizabeth Gendreau’s academic journey led from the foothills of the Blue Ridge Mountains to the base of the French Alps.
By Ron Grant
By the time Elizabeth Gendreau reached the stage at Clemson University’s Littlejohn Coliseum in December 2018, she was picking up her second master’s degree and had a job offer at Michelin North America in Greenville.
Her story illustrates how studying abroad can enrich the academic experience for engineering students and give them an advantage in the hunt for jobs.
Gendreau began her Clemson studies in the Calhoun Honors College, which meant she was able to take advantage of the EUREKA! (Experiences in Undergraduate Research, Exploration and Knowledge Advancement) program. EUREKA! brings incoming freshman to campus in the summer before their first semester for a five-week period of research or other scholarly activities.
She chose to collaborate with Josh Summers, a professor of mechanical engineering, who at the time was engaged in a lunar wheel design project sponsored by Michelin and NASA, among others.
“Elizabeth stood out because of her enthusiasm and passion,” Summers said. “She was always good to work with because to her, everything was fun.”
Her EUREKA! experience evolved into a Creative Inquiry project that continued for the rest of her undergraduate career. Ultimately, she became the senior leader of the team.
While exploring study abroad options, she discovered that undertaking a global adventure could delay the completion of her degree by a semester. The extra tuition and housing costs created by such an interruption made the proposition very expensive, one that did not make economic sense for her.
“Even if the costs had not been prohibitive, I didn’t really find a program that would meet my curricular needs,” she said. “My goal was to immerse myself in the language in a kind of sink-or-swim scenario.”
As she moved toward receiving her bachelor’s degree, Gendreau also had to decide if she wanted to go to work or pursue studies at the graduate level.
“When we are looking for people who we think will survive grad school, they have to be passionate and inquisitive, and they have to be hardworking,” Summers said. “Elizabeth exhibited those traits all throughout her undergraduate career, and I knew she’d be an asset to the team.”
He invited her to work in his research program, and mentioned he’d taken a sabbatical at the Institut Polytechnique de Grenoble (Grenoble INP) at the University of Grenoble Alpes in France. Then he raised the possibility of studying there.
As a reward for her hard work throughout her undergraduate career, Summers invited Gendreau and several other graduate students to attend a one-week writing workshop in early 2016 at the University of Grenoble Alpes. She got a feel for the school, faculty and city, and decided to apply for their master’s degree program in industrial engineering. Not only was she accepted, but she ended up receiving an IDEX Master Scholarship for International Students. For her last semester, she received an additional research assistantship that reduced her out-of-pocket costs even further.
“Many of the undergraduate study abroad programs I looked into were only for a month or a semester, and in most cases, you were grouped with other Americans,” Gendreau said. “Consequently, the foreign language exposure would have been limited.”
At the University of Grenoble Alpes, she worked in classes taught in French, and she lived in a university residence surrounded by French and international students. “It was just what I wanted — a complete immersion in the French language and culture.”
She completed the master’s in France and then returned to Clemson to wrap up her thesis for her master’s degree in mechanical engineering.
“I feel very fortunate to have had the opportunity to participate in such a rewarding study abroad experience,” she said. “And with the assistantship, I was able to accomplish that in a way that was economically feasible.”
As she begins her career with Michelin North America, she is hopeful that her path might ultimately take her back to France.
Bonne chance, Elizabeth Gendreau. Bonne chance. ✲
PROGRAMS: TIME for Robotics
TIME FOR ROBOTICS
Researchers turn to virtual reality to help build the advanced manufacturing force.
by Paul Alongi
The same technology that adds a sense of realism to video games will soon teach students across the country about robotics in advanced manufacturing.
Virtual reality is the centerpiece of a new program, TIME for Robotics, that the Clemson University Center for Workforce Development is preparing to bring online.
It’s aimed at reaching a generation of students who grew up on smartphones and tablets while dispelling fears that robots will take away jobs. It’s also shattering the myth that manufacturing is dirty, miserable work.
The reality is that manufacturing has gone high-tech, and many decent-paying jobs are available for those with a background in science, technology, engineering and math, according to researchers. A key focus of the program will be on how people and robots can work together.
The new approach will be particularly helpful in attracting groups that might otherwise bypass advanced manufacturing, including women, groups underrepresented in STEM fields, veterans and people with disabilities.
Clemson President James P. Clements announced to a crowd of advanced manufacturing executives on October 9 that TIME for Robotics will be funded with $1.79 million from the Department of Defense Manufacturing Engineering Education Program.
“The changing landscape in manufacturing calls for new and innovative approaches to providing the workforce of tomorrow with the skills needed to succeed,” said Clements. “TIME for Robotics is aimed at deepening and diversifying the pool of workers who are ready for jobs in advanced manufacturing.”
The program is helping address industry’s call for workers with the skills needed to qualify for jobs in advanced manufacturing. A skills gap could leave as many as 2 million manufacturing jobs unfilled by 2025, per a study by Deloitte and the Manufacturing Institute.
Plans call for researchers to develop curriculum tracks for students pursuing high school diplomas, associate degrees, baccalaureate degrees and master’s degrees. Greenville Technical College will be the first to use the curriculum.
Courses will be divided into modules that are designed to supplement traditional classroom lessons. Instructors will be able to cherry-pick which modules to use in their classes.
The modules will be made available at EducateWorkforce.com, which gives students the freedom to study at times of their choosing. It’s a feature particularly attractive to students who also work full-time jobs, researchers said.
Anand Gramopadhye, dean of the College of Engineering, Computing and Applied Sciences, is leading the project as principal investigator of TIME for Robotics and the Clemson University Center for Workforce Development.
“Advanced manufacturing education will be innovated and strengthened through personalized learning and virtual reality, two of the grand challenges identified by the National Academy of Engineering,” he said. “This project will assure technological superiority through the transformation of the technical education paradigm.”
Rebecca Hartley, director of operations at the Clemson University Center for Workforce Development, said the courses will help dispel fears that robots will take jobs.
“So much is moving in the direction of robotics and automated processes,” she said. “There is a fascination with it and a terror when people think about losing jobs. TIME for Robotics will allow us to showcase the critical skills that students need to know. That takes away a lot of the fear. Most of the courses we are looking at focus on where the human interaction is so important.”
Kapil Chalil Madathil, the director of technology operations at the Clemson University Center for Workforce Development, said the team will create a series of courses that include online lectures and videos, along with lessons in augmented and virtual reality.
The curriculum could include lessons on programming robotic systems and how multiple robotic systems can work with a human, he said. One proposed augmented-reality module would allow students to walk through a manufacturing plant from a first-person viewpoint to acquaint students with various operations.
“The overarching goal is to support the needs of students entering the advanced robotics industry,” said Madathil, who is also an assistant professor of industrial and civil engineering. “We want to provide a plug-and-play system that allows students and instructors to use this content in a seamless fashion.”
Laine Mears, BMW SmartState Chair in Automotive Manufacturing at Clemson, said the Vehicle Assembly Center, an assembly line built for research, will serve as a testbed to validate the curriculum the team develops.
“We will have technicians and technical college students trying out the materials as they are developed,” he said. “We will see how they work in terms of training and how you might integrate those materials into a manufacturing enterprise. The Vehicle Assembly Center is an ideal place to do that because we have people and robots working together.”
One of the researchers contributing to the project, Yue “Sophie” Wang, is an associate professor of mechanical engineering whose research focuses on collaboration between people and robots.
Robotics is advancing rapidly in the market, she said.
“TIME for Robotics will prepare our future workforce and help make students aware of these new technologies in robotics, especially in manufacturing applications,” she said. “When they graduate and go into the job market, they will have the necessary skills to work with this new technology.”
Venkat Krovi, Michelin Endowed Chair in Vehicle Automation, said mystery surrounds what robotics is, what robotics can do and what skills people need to enter the field.
“Our goal is to look at educating the workforce to go one level deeper, to give them greater insight into what robotics can do and what it cannot do easily,” he said. “There is a lot of fear about robots replacing humans and a lot of it is unfounded.” In fact, Krovi explained, a robot can make dangerous jobs safer and it can take on monotonous work and leave more stimulating jobs for humans to pursue.
Funding for TIME for Robotics lasts three years, and plans are in the works to sustain the program beyond the grant period. ✲
RESEARCH: Artificial Intelligence
LEARNING TO WORK WITH ROBOTS
Yue “Sophie” Wang and her team are solving the mathematical equations and writing the computer code that could advance collaboration between robots and humans.
The robotic arm swung from one side to the other as Ph.D. student Zhanrui Liao tapped on a touchscreen control panel in a Clemson University lab stocked with robots and drones of various shapes and sizes.
“I’ve always been a fan of robots,” Liao said, as a smile spread across his face. “That was the first thought when I chose this lab.”
Liao is conducting research under Yue “Sophie” Wang, the Warren H. Owen – Duke Energy Associate Professor of Engineering. Their focus is on collaborative robots, such as the UR5 robotic arm that Liao was operating in the Intelligent and Interdisciplinary Research Laboratory.
The technology is aimed at helping human workers rather than replacing them. The idea is for robots to perform repetitive tasks, freeing people to do work that requires more skill and dexterity. For Wang and her team, the challenge is to ensure the robots can work safely and efficiently alongside humans. Their research could help make advanced manufacturers more competitive by boosting productivity.
Wang sees big potential for collaborative robots in the automotive and aerospace industries, both major employers in South Carolina.
“If we can combine the strength of highly skilled workers with robots that can do repetitive tasks without fatigue, then we will be a state that manufactures smartly,” she said. “And then we’ll have very high-tech manufacturing plants in South Carolina.”
Wang has carved out a reputation for herself as a fast-rising researcher and pioneer in human-robot collaboration research. She won two of the top research grants for early-career faculty members — the National Science Foundation’s CAREER award in 2015 and the Air Force Young Investigator award in 2016.
Wang said her team’s major innovation has been its “analysis and quantification of cognitive and social impacts on humans into robot motion planning and control algorithms.”
“If we can combine the strength of highly skilled workers with robots that can do repetitive tasks without fatigue, then we will be a state that manufactures smartly.”
– Yue “Sophie” Wang
“It’s very important to persuade your human partners to use automation,” she said. “If they do not accept these robotics partners which will help their performance, then they will do everything manually.”
Many robots in manufacturing plants work separately from humans for safety reasons, Wang said. To guarantee safety, Wang and her team have been measuring human position and velocity so that the robots can keep track of their human counterparts and avoid accidents.
The research is also helping robots learn what pace to work so that they don’t go too fast or too slow for their human collaborators.
Through the research, students are learning cutting-edge skills in robotics.
Both graduate and undergraduate students are getting in on the programming. In a Creative Inquiry course that Wang is leading, undergraduate students are designing a new part so that the UR5 robot can be outfitted with a “universal gripper.” It would allow the robot to pick up parts of various shapes without changing grippers.
The experience is positioning students to land jobs at software, robotics and autonomous driving companies.
“Most of my students are very good at mathematics and programming,” she said. “And they have hands-on experience with robots.” ✲
RESEARCH: Manufacturing Technology
AUTOMOTIVE INNOVATION
Clemson University automotive engineers invent “single-shot” manufacturing technology designed to lower car-build costs and improve gas efficiency in tomorrow’s cars.
by Paul Alongi
New technology invented at Clemson could help reduce the time and cost of manufacturing components that are composed of different materials and need to be joined together. Even better, the process could be automated with the help of artificial intelligence.
Srikanth Pilla and Saeed Farahani are calling their technology “hybrid single-shot manufacturing of metals and composites.” It’s aimed at streamlining the manufacturing of some components, such as the center consoles in high-end cars, said Pilla, the Jenkins Endowed Professor in the Department of Automotive Engineering and founding director of the Clemson Composites Center.
One of the goals is to reduce the cost of making vehicles lighter, which improves their mileage and helps automotive companies meet federal fuel efficiency standards. But researchers say the technology could be used in a variety of industries, including home appliance manufacturing.
The technology could be ready for the manufacturing floor in as little as two years, Pilla said.
When some parts are made conventionally, one machine stamps sheet metal into the desired shape, and another machine creates polymer or composite parts. Then the pieces are bonded together with glue.
In hybrid single-shot manufacturing, it’s all done on one machine. The technology can be used in existing equipment, obviating the need for major capital investment, Pilla said.
The new method could reduce infrastructure costs and cycle time, while helping ensure that the pieces are mistake-free and fit snugly together. Pilla illustrated the work with a half-moon-shaped piece of polymer that was embedded in a rectangular piece of sheet metal.
“We are shooting the polymer into the sheet metal, and that is deforming the sheet metal,” he said. “While it’s deforming, it’s also bonding to the sheet metal. So, it’s one single operation.”
Farahani moved to Greenville from Tehran Polytechnic to work under Pilla as a Ph.D. student at the Clemson University International Center for Automotive Research.
“When I found this research topic in the literature, I thought, ‘This is going to be perfect for me,’” Farahani said. “My academic background is metal forming, but my experience is mostly on composite and plastic tool design. So, with this subject, I can combine these two together.”
Pilla said the team’s approach to the research is unique: “Maybe one or two research groups in the world have been working on this, but they are all looking at it from the metals side. We actually flipped the problem, and we said, ‘This one people will do, and it’s easy to do because sheet metal has a pretty established methodology.’
“Also, my expertise is in polymers and composites, so it makes sense to investigate the problem by flipping it.”
As part of the research, Farahani built a “concept design tool,” and covered it with sensors that measure everything from temperature to pressure. He also created his own software that allows researchers to create a computer model of the machine’s process, called a “digital twin.” The digital twin, coupled with artificial intelligence, is playing a crucial role in teaching the machine to operate on its own.
For the tool to learn, it needs to make mistakes. But allowing the tool to run hundreds of cycles would be too expensive. Instead, researchers have conducted a limited number of experiments with the machine. Now they are feeding data from the experiments into the machine’s digital twin, along with physics-based models that help the machine understand its limitations.
“We are saying that science has limits, and these are the limits for you,” Pilla said of the message to the machine. “Then the machine will know what its capabilities are and accordingly it will try to learn by itself.”
The research helped Farahani secure his Ph.D. in automotive engineering in December. He is continuing this work as a postdoctoral researcher in Pilla’s lab to further refine the digital twin. Researchers also plan to test the new technology at the Clemson Composites Center with the goal of making real components. ✲
RESEARCH: 3D Printing Technology
LEVELING UP ELECTRONIC TECHNOLOGY
Clemson researchers explore how laser 3D printing could change how some of our everyday electronics are manufactured.
By Paul Alongi
Cars that go more than 1,000 miles on a single fill-up and smartphones that can run for days without recharging are possibilities that could come out of a new Clemson University research project that brings together 3D printing and laser processing.
Jianhua “Joshua” Tong and his team are working on a new 3D-printing technique involving rapid laser processing to create “protonic ceramic electrolyzer stacks” that convert electricity to hydrogen as a way of storing energy.
The electrolyzers could have several uses, including as a fuel source in cars or to store energy generated from solar and wind power.
The new laser 3D-printing technique would reduce the time and cost of manufacturing highly compacted electrolyzers, Tong said. In doing so, it could not only cut the cost of hydrogen production in half but also decrease device size one order of magnitude.
Tong, an associate professor of materials science and engineering, is leading the research with $1.6 million from the U.S. Department of Energy’s Office of Energy Efficiency and Renewable Energy.
“Our success will mean we can provide sustainable, clean energy,” Tong said. “That is the fantastic part. We are taking 3D printing to the next level.”
If researchers succeed with the electrolyzers, the same technique could be applied to 3D printing other types of ceramic products, including batteries and solar cells, Tong said. The technique could, for example, lead to high-density batteries that allow smartphones to maintain a charge for days at a time.
Tong’s project is the latest in a growing body of research aimed at using 3D printing to change how products are manufactured. In 3D printing, products are designed on a computer and then printed one layer at a time, the layers stacking on top of each other to create the product.
The microwave-size 3D printers often found in high school classrooms print with plastic. One of the big challenges in advanced manufacturing is to figure out how to cost effectively print with other types of materials.
For Tong, the focus is on ceramics. When made conventionally, ceramics have to be sintered in a furnace at high temperatures, often for several hours. Different types of ceramics need to be sintered at different temperatures.
An electrolyzer requires four different types of ceramics, making the sintering a challenge.
In Tong’s project, a 3D printer puts down a layer of ceramic, and a laser sinters it at the same time, eliminating the need for a furnace. The technique would allow the user to 3D print an electrolyzer made out of four different types of ceramics (like making a cake with a different flavor for each layer).
This could open 3D printing to new products and all the advantages that come with it. For example, a design for a car’s fuel-cell stack could be emailed to a factory thousands of miles away, and it could be printed within hours rather than waiting days for delivery, Tong said.
The project brings together four faculty members in Clemson’s Department of Materials Science and Engineering. Tong serves as the principal investigator on the project, while Hai Xiao, Kyle Brinkman and Fei Peng are co-principal investigators.
Rajendra Bordia, former chairman of the department, said the research enhances Clemson’s efforts to help create more sustainable ways of converting energy.
“The Department of Materials Science and Engineering is uniquely positioned to play a leading role in using electrolysis to create energy for transportation from renewable sources,” he said. “The team working on this project represents world-class expertise in relevant areas, including ceramic materials and devices for energy conversion, laser processing, additive manufacturing and ceramic processing.”
Anand Gramopadhye, dean of the College of Engineering, Computing and Applied Sciences, said the project builds on Clemson’s excellence in advanced manufacturing research.
“The amount of the award is a testament to the innovative ideas and top talent that are going into the research,” Gramopadhye said. “I congratulate Dr. Tong and his team on the grant.” ✲
CLEMSON ALUMNI: Ron and Jane Lindsay
COMING HOME
Returning to the Upstate has allowed Ron and Jane Lindsay to establish invaluable connections with the students and professors they support through generous donations.
By Paul Alongi
Clemson University alumni Ron and Jane Lindsay are donating $1 million to the College of Engineering, Computing and Applied Sciences to fund scholarships, professorships and the college’s greatest needs.
It’s just one of many ways the couple gives back to the University and the surrounding community.
Ron helps guide the college as a member and former chairman of its advisory board. He was recognized for his service in 2016 when he received the college’s highest honor, induction into the Thomas Green Clemson Academy of Engineers and Scientists.
Ron is also one of the original members of the Leadership Circle, a group of donors who provide unrestricted gifts to the college to support student engagement, faculty advancement and academic opportunities that shape tomorrow’s leaders.
The Lindsays’ latest donation was built in the same spirit.
Anand Gramopadhye, dean of the college, said the Lindsays’ gift will have a deep impact on students and faculty for years to come: “I express my deepest, heartfelt gratitude to Ron and Jane Lindsay. Their generosity is inspirational, and they are wonderful ambassadors for Clemson University. By giving so freely of their time and treasure, they are an integral part of the college’s success.”
Ron grew up in North Augusta, and Jane is from Mount Pleasant. They met at Clemson, and both graduated in 1980 with bachelor’s degrees. Ron’s degree was in chemical engineering, and Jane’s was in economic biology.
Ron took a job with Eastman in Kingsport, Tennessee, immediately after graduation and stayed with the chemical company for 36 years before retiring in 2016 as chief operating officer.
“Eastman benefited tremendously from Clemson engineering students,” Ron said. “We hired quite a few, and they were always very well-equipped.”
“I’m thankful for the opportunity to give back and grateful that Clemson University brought Ron and me together when we were students.”
– Jane Lindsay
After Ron retired, the Lindsays moved to their lake home about 30 minutes from campus. The move put them closer to their three grown children — Ryan, Elizabeth and Lauren — and two-year-old granddaughter, Blake.
The Lindsays mentor students through Clemson Presbyterian Church and offer financial-literacy counseling to help people with long-term financial problems.
They’ve opened their home to as many as 50 students at a time, including once last year for a church-university ministry planning retreat. The students didn’t have much chance to play on the water that day, so the Lindsays invited them back.
“As you get to know the students, you get past the stereotypes — what is being said about the current generation — and you get to know individuals,” Ron said. “You stay relevant and current with what they’re facing, what their challenges are.”
Nate Matzko, a biochemistry and genetics double major from Irmo, said he met the Lindsays through Clemson Presbyterian and that they have been a great support system when college gets stressful.
“I’m not surprised they’re making the donation,” he said. “They are two of the most loving, generous people I’ve come across.” ✲
The Lindsay gift is divided into five parts:
■ $500,000 establishes the Ron and Jane Lindsay Innovation Professorship Endowment
■ $250,000 establishes the Ronald C. Lindsay ‘80 and Jane B. Lindsay ‘80 Unrestricted Endowment for the College of Engineering, Computing and Applied Sciences
■ $100,000 will be directed to the CECAS Dean’s Excellence Fund
■ $100,000 establishes the Ron and Jane Lindsay Family Annual Professorship
■ $50,000 will be added to the existing Ronald C. Lindsay ‘80 and Jane B. Lindsay ‘80 Scholarship Endowment, which has already benefited several students since its creation in 2011
CLEMSON ALUMNI: Vanessa Wyche
BREAKING BARRIERS
Clemson was a launching pad for Vanessa Ellerbe Wyche, the first African-American to serve as deputy director of NASA’s Johnson Space Center.
By Paul Alongi
Vanessa Wyche is literally shooting for the moon and beyond in her new job, as NASA prepares to launch astronauts from Florida for a mission to Mars.
Wyche was promoted to deputy director in August 2018 after holding several leadership positions in a career with NASA spanning nearly three decades. She is now helping Director Mark Geyer lead 10,000 civil service and contract employees at Johnson Space Center in Houston and White Sands Test Facility in Las Cruces, New Mexico.
Wyche, who holds two engineering degrees from Clemson, said she follows the example set by her parents, who both gave back to their community. She counts her father as her most influential mentor.
“My father, who was an educator, believed that girls could do everything that boys could do, and so he exposed us to everything that my brother did,” said Wyche, one of four girls. “We got to learn everything about mechanics. He wanted us to be able to fix our own car if we had a flat.”
Wyche remembers having to study hard at Clemson. She entered the University without the benefit of having taken many advanced classes because they were scarce in South Carolina high schools at that time.
“I had some really good professors,” Wyche said. “I remember my chemistry professor probably the best of all. I remember telling him that I wasn’t quite understanding something. He told me that I just needed to step back, take a break, and it was going to come to me. And it did.”
Lee Gill, chief diversity officer at Clemson, said that Wyche’s success provides a powerful example to students who may not have had access to college-prep and STEM programs in high school.
“The message I want our students to take away is what she said — do not let your environment dictate who you are,” he said. “If you want to be an engineer, if you want to be a scientist, if you want to be an astronaut — wherever you come from — you can be that.”
Wyche grew up the youngest child in a family of five. They lived in Conway, a city along the Waccamaw River that is removed by about 15 miles from the tourist hubbub of Myrtle Beach.
Wyche’s father, Gilbert B. Ellerbe, Jr., served as the assistant principal at Conway High School, the executive director of a local recreation facility, and Boy Scouts master. Wyche’s mother, Inez Bethea Ellerbe, was an elementary school teacher and Girl Scouts leader.
“She was a great role model because she worked, and she also took care of five kids,” Wyche said.
“She made sure we all had exposure to the arts. We were all in scouts. We grew up in a church.”
Clemson recruited Wyche when she was a student at the South Carolina Governor’s School for Science and Mathematics, back when it was a summer program in Charleston. When Wyche arrived on campus, she joined her brother, Gilbert Ellerbe, who would go on to receive his bachelor’s degree in chemical engineering.
Wyche was at Clemson from 1981-87, receiving her bachelor’s in engineering and master’s in bioengineering.
Then she headed for Washington, D.C., where she took a job with the Food and Drug Administration in the Office of Device Evaluation. Her Clemson education prepared her well, she said.
While in Washington, the Clemson alumna met Georgetown Law student George Wyche, Jr., who became her husband. They moved to his hometown, Houston, so she needed a new job.
That’s how Wyche found her way to the Johnson Space Center, where she was the first woman hired as a project engineer in the division she was assigned.
“When I got here, I just used the same principles that allowed me to be successful at Clemson, which included hard work,” she said. “I was a sponge. If there was something to learn, I was learning it.”
Within about six months, Wyche was named employee of the month, and her career has been on a rocket-like trajectory ever since. She has held several leadership positions and is the recipient of two NASA Exceptional Achievement Medals and two NASA Outstanding Leadership Medals.
In her current job, Wyche has her sights set on new launches from Florida and sending astronauts to the moon and then on to Mars.
“These are exciting times at NASA,” she said.
Astronauts have been continuously orbiting Earth aboard the International Space Station for nearly 18 years. Since the shuttle retired, the space station has been resupplied by Russian vehicles launching from Russia.
But that’s about to change, Wyche said.
“We are on the verge of having two new vehicles that are going to launch from Florida — the SpaceX Dragon and the Boeing Starliner,” she said. “We just announced new astronauts. They are training to launch on those vehicles. And so, within the next couple of years, we’re going to be launching again from Florida. We’re super excited about that.”
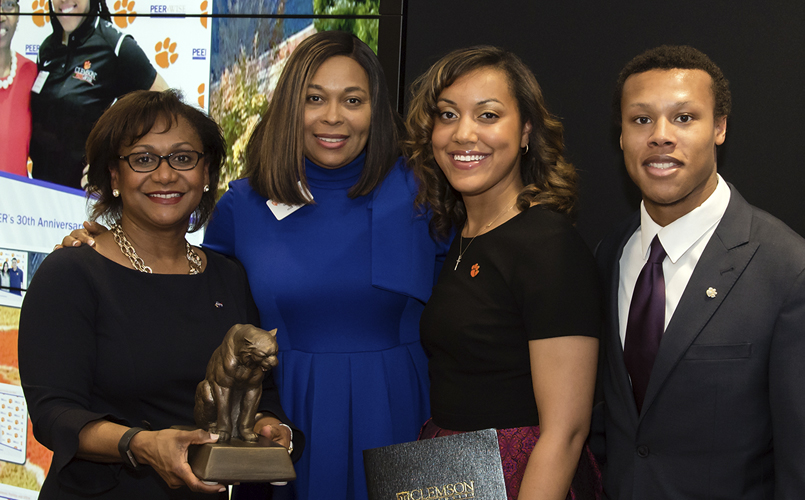
Wyche returned to campus last year to help celebrate the 30th anniversary of PEER & WISE, a program for underrepresented populations in engineering and science.
Serita Acker, the program’s director, said Wyche’s experience shows students there is no limit.
“She is a testament that if you work hard and you network and you get involved, you can go to greater heights,” Acker said. “From where I stand, she is an awesome role model.”
NASA also has been given a clear mission to go to the moon and then to Mars, Wyche said.
“The Orion vehicle is being built and managed here at the Johnson Space Center, and we will launch humans from Florida that will go to a platform in the vicinity of the moon called the Gateway,” she said. “We will have an orbiting spacecraft near the moon that will allow us to access the moon and from there build up a transport capability that will allow us to go to Mars.”
In addition to her career, Wyche is involved in several community organizations in Houston. One sends NASA engineers to a local elementary school to help with a science fair that is judged by professionals from the oil and gas industry. She has also worked with the Boy Scouts.
Wyche and her husband have a 24-year-old son, George Wyche, III, who is an Eagle Scout and college graduate, pursuing a master’s in psychology.
Anand Gramopadhye, dean of the College of Engineering, Computing and Applied Sciences, said that Wyche is an excellent ambassador for her alma mater.
“Mrs. Wyche’s service to her nation, community and alma mater position her as an excellent role model and inspiration, especially for students from underrepresented groups,” Gramopadhye said. “I congratulate her on her new job, and we hope to see her back at Clemson soon.” ✲
News from Around the College
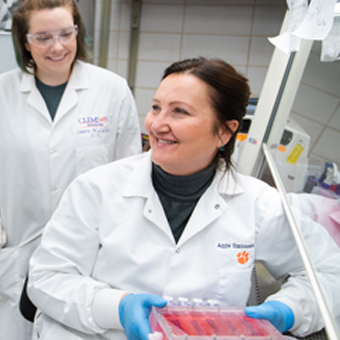
Diabetes targeted in new bioengineering research at Clemson University
Clemson bioengineers are launching a new research project to better understand cardiovascular disease in patients with diabetes, an affliction that affects about 13 percent of South Carolina adults and costs $4.3 billion in a single year.
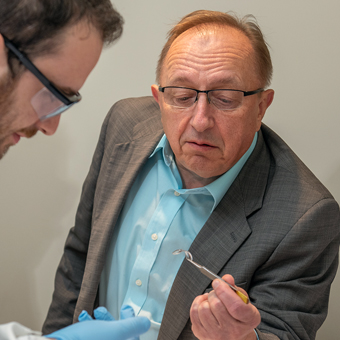
Breakthrough in self-healing materials detailed in journal Science
The cost of making plastics, paints, coatings for cell phone screens, and other materials that heal themselves like skin could be dramatically reduced thanks to a breakthrough that a Clemson University team detailed in the journal Science.
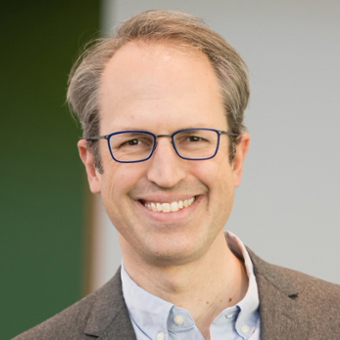
Clemson virtual reality, environmental research boosted by NSF grants
Brygg Ullmer, chairman of the Human-Centered Computing Division, is working to develop a customizable, hands-on virtual reality and advanced display system that could change how scientists across the country share information and collaborate, as well as how students learn.
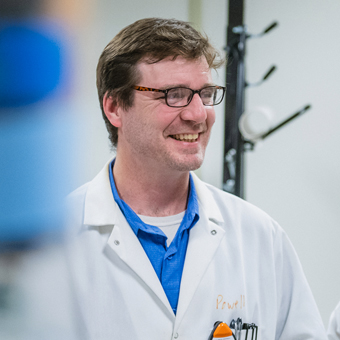
Brian Powell leads research aimed at ensuring sustainability in the environment
A team that has included more than 85 researchers from three South Carolina universities is receiving $2 million to continue investigating how buried nuclear waste would react with soil and groundwater if it were to leak into the environment.
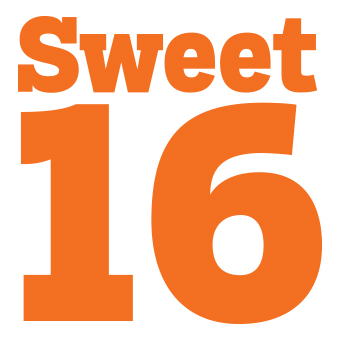
The Glenn Department of Civil Engineering brings home award
A team lead by associate professors Brad Putman and Jennifer Ogle, from the Glenn Department of Civil Engineering, are bringing home an AASHTO Sweet Sixteen Award from the American Association of State Highway and Transportation Officials.
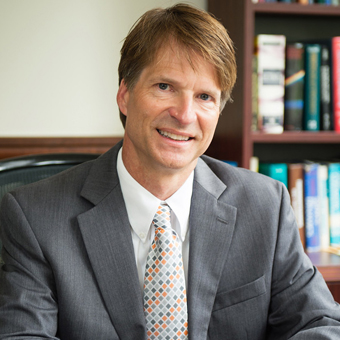
Randy Collins elected chairman of Global Engineering Education Exchange
Engineering students around the world could find new opportunities to study and work abroad as part of an exchange program that serves more than 250 students from 24 countries each year and counts Randy Collins of Clemson University as one of its key leaders.
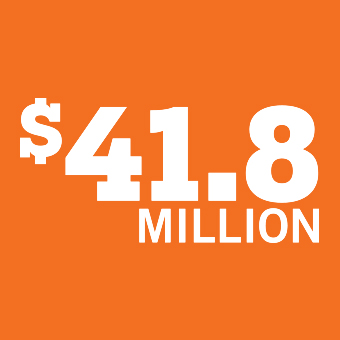
Funding could bring new business to the state of SC
The $41.8 million that has flowed into Clemson for three separate research centers could be the beginning of a larger enterprise that brings South Carolina new business, improved patient care and lower health care costs.
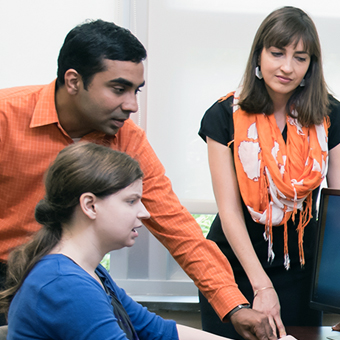
Protecting Children
Deaths that have been tied to social media challenges are capturing the attention of Clemson University researchers who want to begin developing new ways of protecting adolescents and young adults from harming themselves.
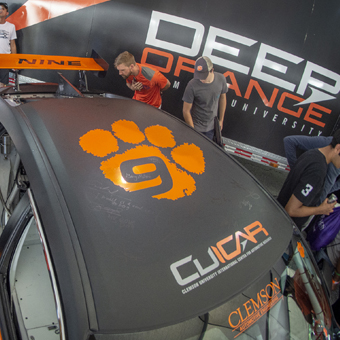
ExxonMobil sponsors Deep Orange sustainability concept vehicle at Clemson University
Clemson students are partnering with industry leaders in an effort to create sustainable solutions for the lifecycle of vehicles. Sponsored by ExxonMobil, graduate automotive engineering students in the University’s flagship Deep Orange program will develop a next-generation sustainable concept vehicle.
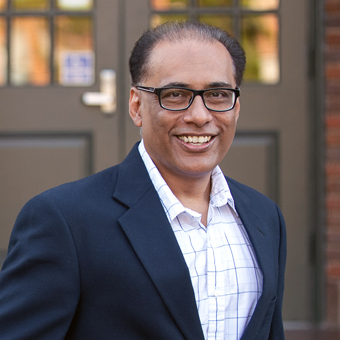
Clemson graduate returns to alma mater as SCE&G Distinguished Professor of Power Engineering
A Clemson University graduate has returned to his alma mater as one of the nation’s few professors to specialize in protecting the electrical grid and other power systems from disturbances that can lead to blackouts.
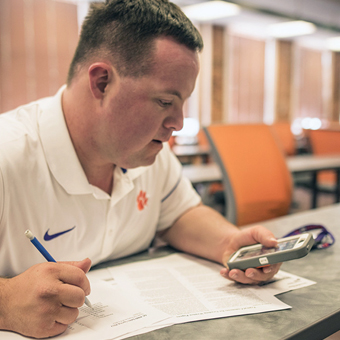
Study finds smartphone app may be the best job aid for people with intellectual disabilities
A study of the effectiveness of the Clemson-developed smartphone app Task Analysis Lite for people with intellectual disabilities has yielded impressive results. The app assists users in the completion of everyday tasks for home and work.
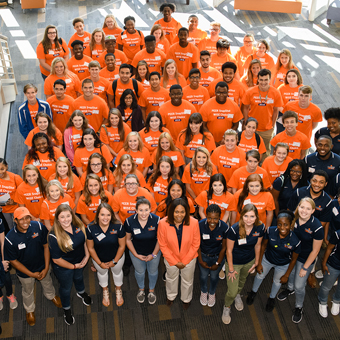
PEER & WISE cited in diversity award given to Clemson University
INSIGHT Into Diversity magazine named Clemson University a recipient of its Higher Education Excellence in Diversity (HEED) Award for the second year in a row.
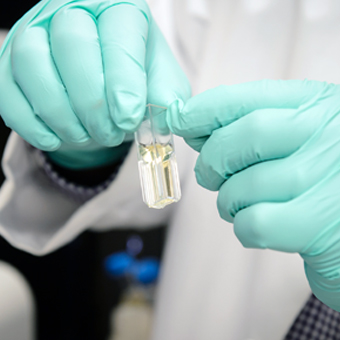
Troubling statistics spark new effort to recruit chemical engineers
Mark Blenner, the McQueen-Quattlebaum Associate Professor in chemical and biomolecular engineering, is leading a team working to increase diversity in chemical engineering by recruiting students who will work toward doctoral degrees and then pursue careers in education and research.
Faculty Spotlight
Delphine Dean, right and Brij Korana examine the contents of a test tube in Rhodes Engineering Research Center. Dean, the Gregg-Graniteville Associate Professor, is leading a growing collaboration with the Indian Institute of Technology to create new medical devices and sensors.
“The Most Marvelous Car at SEMA”
Deep Orange 9, a high-performance rallycross prototype vehicle sponsored by Honda R&D Americas Inc., was a showstopper at the SEMA Show in Las Vegas. The vehicle was designed and built by automotive engineering students at the Clemson University International Center for Automotive Research. The Deep Orange program challenges Clemson students to address real-world challenges related to sustainable mobility, as well as current and future social trends. Deep Orange 9 demonstrates that extreme performance demands can be addressed in a safe, clean way.