The Advanced Combustion and Renewable Fuels Laboratory has a number of active and past projects. The group closely collaborates with Professor Zoran Filipi and Professor Robert Prucka, who are both faculty members in the Automotive Engineering department at Clemson University. For more information on the collaboration between the ACRF and the other powertrain research groups in the Automotive Engineering department, please see the Contact page, which has links to other powertrain research areas at Clemson.
Below is an outline of the active research projects, followed by a more detailed expandable section for each project individually.
- Alcohol Compression Ignition: Determining the optimal compression ignition combustion strategy for renewable alcohol fuels / funded internally – actively seeking external partners and funding
- OP2S: New Two-Cylinder Prototype Demonstration and Concept Design of a Next Generation Class 3-6 Opposed Piston Engine / funded by the Department of Energy, collaboration with Achates Power, Inc.
- OP2S: Opposed-Piston 2-Stroke (OP2S) Hybrid Commercial Vehicle System / funded by the Department of Energy, collaboration with Achates Power, Inc.
- TBCs: Novel TBCs for Gasoline SI Engines / funded by the Department of Energy through the SBIR Program, collaboration with Solution Spray Technologies
- TBCs: Cold-start emissions and deposit growth with temperature-swing TBCs for SI combustion / funded by Ford Motor Company through their University Research Program (URP)
- TBCs: Investigation of the effects of TBCs on GCI combustion / funded by Aramco Services Company
- Autonomous Military Vehicles: VIPR-GS 2.3 – Power Generation and Propulsion Systems for Autonomous Off-Road Vehicles / funded by the U.S. Army through the VIPR-GS center at Clemson University
- Autonomous Military Vehicles: Smart Configuration Optimizer Through Transformative Analytics / funded by the Office of Naval Research, collaboration with Palo Alto Research Center (PARC)
Active Research Projects
Expand each research project below using the arrow on the left to learn more.
1. Alcohol Compression Ignition Combustion
Background: Current truck and passenger car regulations in the U.S. and Europe are based on tailpipe CO2 emissions which has motivated massive investments in electric vehicles as well as smaller investments in hydrogen and ammonia for combustion engines, since they do not produce any tailpipe CO2 emissions. However, the rising atmospheric CO2 level is not due to CO2 emissions from vehicle tailpipes specifically; it is due to a global imbalance in the natural carbon cycle.
Before industrialization, the carbon cycle consisted of plants absorbing CO2 through photosynthesis to form sugars, and those sugars reconverting to CO2 through animal and bacteria consumption (e.g., humans eating and breathing). In a balanced carbon cycle, the atmospheric CO2 level remains constant. The discovery and utilization of fossil fuels to industrialize human civilization released a large amount of stored carbon into the atmosphere, which, along with population growth and deforestation, caused an imbalance in the carbon cycle (i.e., the atmospheric CO2 level rose). Now, if human civilization honestly desires to stop the rise in atmospheric CO2 or reduce the CO2 level, regulations must be based on the carbon cycle that is currently imbalanced.
Although policies take time to adapt, researchers in the transportation field have already adopted terms for the impact of various activities on the carbon cycle, i.e., “net-carbon” or “lifecycle CO2” emissions. Lifecycle CO2 is a quantitative metric that considers the carbon cycle which could be used to guide future regulations.
If future regulations are based on lifecycle CO2 emissions rather than tailpipe CO2 emissions, then biofuels, like biodiesel and ethanol (which utilize plants to absorb CO2 from the atmosphere in an attempt to re-balance the carbon cycle), as well as e-fuels produced from renewable electricity and waste CO2 streams, like methanol, would be more attractive alternatives to fossil fuels for general transportation applications. As liquid fuels, their energy density is reasonably high, their storage and distribution are significantly simplified, including the potential to use the current distribution and refueling network with only minor changes, and their handling and pressurization on the vehicle do not incur a significant cost or energy burden like the gaseous renewable fuels.
Goal: The goal of this project is to determine the optimal compression ignition (CI) combustion strategy for renewable alcohol fuels, including methanol, ethanol, propanol, and butanol, and their blends. Ethanol is made by fermenting sugars or starches and then distilling to remove the water. It saves cost and energy to truncate the water removal process at some concentration of ethanol in water, which is sometimes referred to as “hydrous” ethanol or “wet ethanol” depending on the water content. We believe that 80% ethanol and 20% is water is the optimal concentration for a variety of reasons; therefore, most of our work has focused on Wet Ethanol 80 (WE80).
Key Findings: This project has generated several key findings to-date. First, a conclusion of this project is that mixing controlled compression ignition (MCCI, i.e., conventional diesel combustion) of methanol and ethanol is possible. The benefits of MCCI with alcohols are:
- MCCI provides good control over the combustion process and robustness, and there is extensive heritage knowledge in industry about this combustion process
- Combustion of methanol and wet ethanol does not produce any particulate matter (PM, i.e., soot emissions)
- Finally, due to the lack of soot emissions, MCCI combustion of alcohols is more EGR-tolerant than conventional diesel or gasoline combustion, which leads to lower NOx emissions
These benefits are substantial and they provide a direct pathway for industry to reduce soot and NOx emissions from CI engines, while reducing lifecycle CO2 emissions by more than 40%. And it’s a solution that can be implemented today!
However, there are drawbacks associated with MCCI of alcohols and they are:
- MCCI of methanol and wet ethanol requires high intake valve closing (IVC) temperatures to ensure stable ignition. IF the IVC temperature needs to be over some threshold but doesn’t need to be controlled quickly, then this challenge is a solvable problem that only requires engineering solutions.
- There is a significant thermal efficiency penalty associated with evaporating the alcohols around top dead center. This is a larger problem in the interest of reducing greenhouse gas emissions and reducing cost of sustainable solutions.
- Although the PM emissions are essentially zero, the particulate number (PN) emissions from MCCI is non-negligible, even with alcohols.
- Although the NOx emissions are lower than conventional diesel, they can be reduced further with more clever combustion strategies (keep reading!).
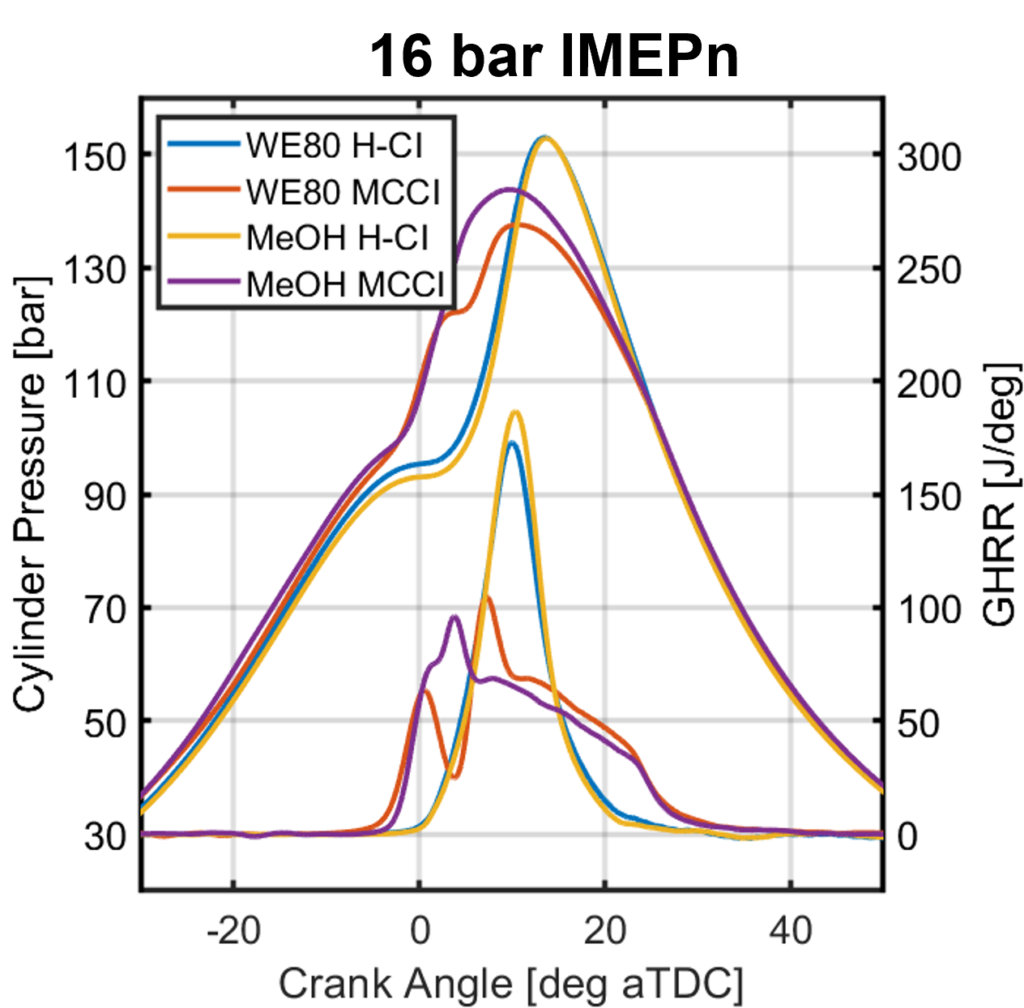
To improve the NOx emissions and PN characteristics, and resolve the efficiency penalty, we developed a hybrid compression ignition approach that combines MCCI with some advanced compression ignition strategies to maximize efficiency and minimizes NOx and PN in addition to PM, while maintaining combustion control and robustness. We have demonstrated this combustion process at full load (up to 25 bar IMEPn).
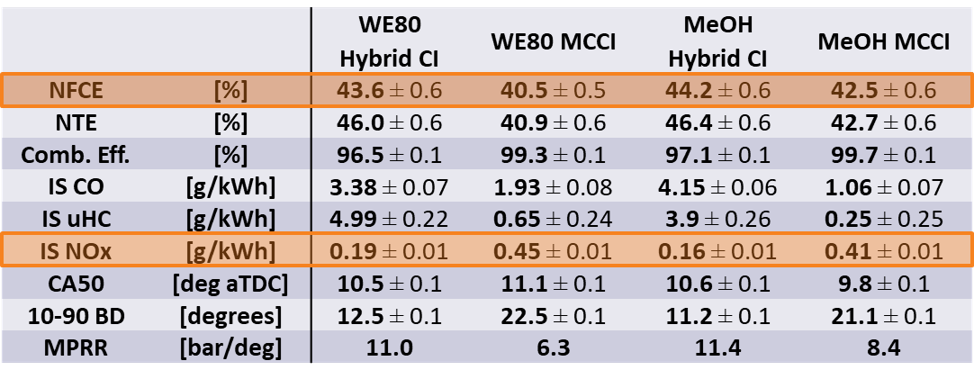
Publications related to this project:
(current group members are bolded)
- Gainey B, Gandolfo J, Yan Z, Lawler B. Mixing controlled compression ignition with methanol: An experimental study of injection and EGR strategy. International Journal of Engine Research. June 2022. doi:10.1177/14680874221105161
- Gainey, B.; Yan, Z.; Gandolfo, J.; Lawler, B. High Load Compression Ignition of Wet Ethanol Using a Triple Injection Strategy. Energies 2022, 15, 3507. https://doi.org/10.3390/en15103507
- Gainey, B., Hoth, A., Waqas, M., Lawler, B. et al., “High Temperature HCCI Critical Compression Ratio of the C1-C4 Alcohol Fuels,” SAE Int. J. Adv. & Curr. Prac. in Mobility 3(4):1495-1507, 2021, https://doi.org/10.4271/2021-01-0511.
- Gainey, B., Moser, S., Lawler. B., “Autoignition characterization of wet isopropanol-n-butanol-ethanol blends for ACI,” SAE Technical Paper 2021-24-0044, 2021.
- Gainey, B., O’Donnell, P., Yan, Z., Moser, S., Lawler, B., “LTC performance of C1–C4 water-alcohol blends with the same cooling potential,” Fuel, Volume 293, 2021, 120480, ISSN 0016-2361, https://doi.org/10.1016/j.fuel.2021.120480.
- Gainey, B., Yan, Z., Lawler, B., “Autoignition characterization of methanol, ethanol, propanol, and butanol over a wide range of operating conditions in LTC/HCCI,” Fuel, Volume 287, 2021, 119495, ISSN 0016-2361, https://doi.org/10.1016/j.fuel.2020.119495.
- Gainey, B., Yan, Z., Moser, S., Lawler, B., “Lean flammability limit of high-dilution spark ignition with ethanol, propanol, and butanol,” International Journal of Engine Research, February 2021, doi:10.1177/1468087421993256.
- Gainey, B., Lawler, B., “The role of alcohol biofuels in advanced combustion: An analysis,” Fuel, Volume 283, 2021, 118915,ISSN 0016-2361, https://doi.org/10.1016/j.fuel.2020.118915.
- O’Donnell, P., Rahimi Boldaji, M., Gainey, B., Lawler, B., “Varying Intake Stroke Injection Timings with Wet Ethanol in LTC: A CFD Simulation Study,” SAE Technical Paper 2020-01-0237, 2020.
- Gainey B, Hariharan D, Yan Z, Zilg S, Rahimi Boldaji M, Lawler B. A split injection of wet ethanol to enable thermally stratified compression ignition. International Journal of Engine Research. 2020;21(8):1441-1453. doi:10.1177/1468087418810587
- Gainey, B., Yan, Z., Rahimi-Boldaji, M., and Lawler, B. “On the Effects of Injection Strategy, EGR, and Intake Boost on TSCI with Wet Ethanol,” ASME. J. Eng. Gas Turbines Power. August 2020, doi: https://doi.org/10.1115/1.4048150.
- Gainey, B., Yan, Z., Moser, S., Vorwerk, E., Lawler, B., “Tailoring Thermal Stratification to Enable High Load Low Temperature Combustion with Wet Ethanol on a Gasoline Engine Architecture,” International Journal of Engine Research, 2020, https://doi.org/10.1177/1468087420945960.
- Gohn, J., Gainey, B., Zainul, S., Lawler, B., “Wet ethanol in LTC: How water fraction and DTBP affect combustion and intake temperature at naturally aspirated and boosted conditions,” Fuel, Volume 267, 2020, 117094, ISSN 0016-2361, https://doi.org/10.1016/j.fuel.2020.117094.
- Yan, Z., Gainey, B., Gohn, J., Hariharan, D., Saputo, J., Schmidt, C., Caliari, F., Sampath, S., Lawler, B., “The Effects of Thick Thermal Barrier Coatings on Low-Temperature Combustion,” SAE Int. J. Adv. & Curr. Prac. in Mobility 2(4):1786-1799, 2020, https://doi.org/10.4271/2020-01-0275.
- Rahimi Boldaji, M., Gainey, B., O’Donnell, P., Gohn, J., Lawler, B., “Investigating the Effect of Spray Included Angle on Thermally Stratified Compression Ignition with Wet Ethanol Using Computational Fluid Dynamics,” Applied Thermal Engineering, Volume 170, 2020, 114964, ISSN 1359-4311, https://doi.org/10.1016/j.applthermaleng.2020.114964.
- Gainey, B., Gohn, J., Hariharan, D., Rahimi-Boldaji, M., Lawler, B., “Assessing the impact of injector included angle and piston geometry on thermally stratified compression ignition with wet ethanol,” Applied Energy, Volume 262, 2020, 114528, ISSN 0306-2619, https://doi.org/10.1016/j.apenergy.2020.114528.
- Gainey, B., Gohn, J., Yan, Z., Malik, K. Rahimi Boldaji, M., Lawler, B., “HCCI with Wet Ethanol: Investigating the Charge Cooling Effect of a High Latent Heat of Vaporization Fuel in LTC,” SAE Technical Paper 2019-24-0024, 2019, doi:10.4271/2019-24-0024.
- Gainey, B., Hariharan, D., Zilg, S., Rahimi Boldaji, M., Lawler, B., “TSCI with Wet Ethanol: an investigation of the effects of injection strategy on a diesel engine architecture,” SAE Technical Paper 2019-01-1146, 2019, https://doi.org/10.4271/2019-01-1146.
- Rahimi Boldaji M, Sofianopoulos A, Mamalis S, Lawler B, “A CFD Investigation Comparing the Effects of Fuel Split Fraction on Advanced Low Temperature Combustion with a Primary Reference Fuel versus Ethanol”, Frontiers in Mechanical Engineering, Volume 4, 2018, ISSN 2297-3079, 10.3389/fmech.2018.00006, https://www.frontiersin.org/article/10.3389/fmech.2018.00006
2. New Two-Cylinder Prototype Demonstration and Concept Design of a Next Generation Class 3-6 Opposed Piston Engine
Background: Opposed-piston two-stroke (OP2S) engines promise several advantages over conventional engine architectures including reduced heat transfer losses and better control over the in-cylinder scavenging process with the option to only partly scavenge the cylinder at light loads.
Goal: The goal of this project is to better understand the operational characteristics of the OP2S engine including the thermodynamics and the combustion and scavenging (i.e., breathing) processes using reduced-order modeling, high fidelity Computational Fluid Dynamics (CFD) modeling, and experimental research methods.
Key Findings: There are inherent tradeoffs associated with swirl, where the scavenging process generally prefers lower levels of swirl to minimize short circuiting losses, while the closed cycle combustion process generally prefers higher levels of swirl to improve mixing and expedite the combustion process. An example CFD simulation of the scavenging process with a moderate swirl level is shown on the right.
Funding: Clemson’s share: $1.625M. This project is funded by the Department of Energy’s Vehicle Technologies Office through Achates Power, Inc.
Publications related to this project:
(current group members are bolded)
- O’Donnell, P., Gandolfo, J., Gainey, B., Vorwerk, E., Prucka, R., Filipi, Z., Lawler, B., Hessel, R., Kokjohn, S., Huo, M., Salvi, A., “Effects of Port Angle on Scavenging of an Opposed Piston Two-Stroke Engine,” SAE Technical Paper 2022-01-0590, 2022.
3. Opposed-Piston 2-Stroke (OP2S) Hybrid Commercial Vehicle System
Background: Opposed-piston two-stroke (OP2S) engines have not been studied in hybrid vehicle applications to-date.
Goal: The goal of this project is to investigate the interaction between vehicle hybridization and the OP2S engine. Specifically, we’ll strive to understand how to use commercial vehicle hybridization to minimize the emissions associated with a diesel OP2S engine, which maximizing fuel economy.
Key Findings: This project started in the spring of 2022. Key findings will be added throughout the course of the project.
Funding: Clemson’s share: $750k. This project is funded by the Department of Energy Vehicle Technologies Office through Achates Power, Inc.
4. Novel TBCs for Gasoline SI Engines
Background: Temperature-swing thermal barrier coatings (TBCs) have the potential to block heat transfer losses in engines, thereby improving their efficiency. Gasoline spark ignition (SI) engine are the engine architecture found in the majority of vehicles worldwide. Therefore, adding TBCs to gasoline SI engine could result in a significant energy consumption reduction. However, SI engines are constrained by end-gas knock and TBCs pose the risk of negatively impacting knock.
Goal: The goal of this project is to better understand the effects of adding TBCs to various engine components in a gasoline SI engines. The effects on efficiency, charge heating and knock, and exhaust enthalpy will be explored using both experimental research methods and modeling (reduced-order and CFD/FEA).
Key Findings: This project has generated several key findings. First, together with our thermal spray partner Solution Spray Technologies, we developed and tested a novel material that can be applied to aluminum combustion chamber surfaces (i.e., the piston and head). The specific material is considered proprietary. Second, we found that knock is not negatively impacted if the coating thickness is approximately equal to the penetrative depth of the coating material. Thicker coatings do negatively impact knock. Finally, we’ve found that it’s important to maximize the coated surface area to maximize the benefits of the coatings.
Funding: Clemson’s share: $375k. This project is funded by the Department of Energy through their Small Business Innovation Research (SBIR) Phase II program. Clemson is a subcontractor to our thermal spray partner, Solution Spray Technologies (SST).
Publications related to this project:
(current group members are bolded)
- Motwani, R., Gandolfo, J., Gainey, B., Levi, A., Moser, S, Filipi, Z., Lawler, B., “Assessing the Impact of a Novel TBC Material on Heat Transfer in a Spark Ignition Engine through 3D CFD-FEA Co-Simulation Routine,” SAE Technical Paper 2022-01-0402, 2022, https://doi.org/10.4271/2022-01-0402.
5. Cold-start emissions and deposit growth with temperature-swing TBCs for SI combustion
Background: This project is a supplement to the SBIR Phase II project described in #4. There are open questions about the effects of combustion chamber deposit (CCD) growth on the surface of TBCs and how the CCDs might change the material properties of the layer. Additionally, the temperature swing nature of TBCs might assist with cold-start emissions.
Goal: The goal of this project is to help answer these open questions about cold-start emissions with TBCs and CCD growth on the layer of the TBC and how it impacts properties.
Key Findings: This project has learned that CCDs do form on the surface of TBCs and the conductivity of the CCDs can be similar to or lower than the TBCs, which could improve the material properties of the layer. However, CCDs add variability/uncertainty in that their equilibrium layer thickness is a strong function of the operating conditions (i.e., driving styles). TBCs can mimic the benefits of CCDs but remove some of the variability so that the “clean” state is not bare metal.
Funding: $50k. This project is funded by Ford Motor Company through their University Research Program (URP).
6. Investigation of the effects of TBCs on GCI combustion
Background: Gasoline compression ignition (GCI) is an advanced combustion strategy with the potential to lower engine-out NOx and soot emissions compared to conventional diesel combustion. Unlike some of the earlier advanced combustion strategies, GCI has complete load flexibility and similar control authority to conventional combustion modes. The goal of GCI is to achieve diesel-like efficiency levels, or higher, with soot and NOx emissions that are equal to or lower than conventional diesel combustion. TBCs can help push the efficiency of GCI even higher. Additionally, GCI requires slightly elevated intake temperatures to achieve stable ignition, and TBCs can help ensure combustion robustness.
Goal: The goal of this project is to understand the material choice and thickness of TBCs that maximize the benefit with GCI combustion specifically. The ACRF is using both experimental and computational research methods to help achieve this goal.
Key Findings: The key findings to date are again the development and exploration of materials (considered proprietary) that are not conventionally used in the gas turbine industry, but are well-suited to reciprocating internal combustion engine applications. Additionally, we’ve learned that the high boost levels of GCI help counteract any potential charge heating, favoring slightly thicker coatings than SI or conventional diesel might, if the boost level is lower.
Funding: $1.0M. This project is funded by Aramco Services Company.
7. Power Generation and Propulsion Systems for Autonomous Off-Road Vehicles
Background: Next generation ground vehicles for military applications have unique requirements that necessitate unique solutions. Two examples of these unique requirements are that military vehicles require high power density propulsion systems and they will be hybridized to meet the high electrical loads.
Goal: The goal of this project is to develop a modeling and simulation framework for powertrain layout assessment with experimental validation and hardware-in-the-loop (HIL) evaluation.
Key Findings: (Results of this project are considered confidential)
Funding: This project is funded by the U.S. Army through the Virtual Prototyping for Autonomous Ground Systems (VIPR-GS) center at Clemson University.
Publications related to this project:
(current group members are bolded)
- Zhu, Q., Kumar, A., Sundar, A., Egan, D., Mirzaei, H., Chang, D., Schmid, M., Prucka, R., Lawler, B., Paredis, C., “ON-DEMAND ONLY: Development of a Series Hybrid Electrified Powertrain for a High Speed Tracked Vehicle Based on Driving Cycle Simulation,” SAE Technical Paper 2022-01-0367, 2022, https://doi.org/10.4271/2022-01-0367.
8. Smart Configuration Optimizer Through Transformative Analytics
Background: Manned ships have personnel onboard to perform maintenance or repairs in the event of an engine fault/failure. Unmanned ships need smarter algorithms that can sense degradation and predict faults before they occur so that maintenance can be performed in port.
Goal: The goal of this project is to understand what sensors need to be added to an unmanned ship’s engine to be able to predict faults and component degradation.
Key Findings: (Results of this project are considered confidential)
Funding: This project is funded by the Office of Naval Research (ONR) in collaboration with Palo Alto Research Center (PARC).
The Advanced Combustion and Renewable Fuels Lab is very grateful for the financial and technical support of all of its funding sponsors and project collaborators.
Special thanks to the funding sources:
- The Department of Energy (DOE) Vehicle Technologies Office (VTO)
- Ford Motor Company
- Aramco Services Company
- The U.S. Army – Ground Vehicle Systems Center (GVSC)
- The Office of Naval Research (ONR)
And to the project teaming partners:
- Achates Power, Inc.
- Solution Spray Technologies (SST)
- Palo Alto Research Center (PARC)
Thank you!