Clemson University has several unique, state-of-the-art experimental and computational facilities that are available to the Advanced Combustion and Renewable Fuels (ACRF) team. These unique facilities include:
- The Advanced Combustion and Heat Transfer Test Cell
- The Advanced Powertrain (APT) Laboratory
- A 500 HP Chassis Dynamometer
- The Vehicle Propulsion Laboratory (VPL)
- The Palmetto High Performance Computing (HPC) Cluster
Each of these unique facilities are described in detail below.
The Advanced Combustion and Heat Transfer Test Cell
This test cell contains a 100 HP, active, double-ended dynamometer with two single cylinder research engines: a modern gasoline direct injection (GDI) engine (shown on the right) and a modern light-duty diesel engine (shown below on the left).
Single cylinder GDI engine: The GDI engine is a Ricardo Hydra engine block with a prototype GM engine head with a centrally mounted GDI injector and cam phasors. This head is instrumented with a side-mounted Kistler pressure transducer and a centrally mounted Kistler spark plug pressure transducer. Alternatively, the side-mounted pressure transducer can be replaced with a fast response heat flux probe that can measure the combustion chamber surface temperature and heat flux on a crank angle resolved basis.
There is the option to install a separate GDI head onto the Ricardo Hydra block. This second head has a side-mounted GDI injector, which is also a prototype GM engine head meant to mimic the 2.0L Ecotec engine head geometry. This engine head has a side-mounted Kistler pressure transducer with two separate heat flux probe mounting locations; one on the belt side and one on the flywheel side of the engine. The crankshaft has a Kistler shaft encoder. There is a high-speed intake and a high-speed exhaust pressure transducer installed on the engine.
Single Cylinder Diesel Engine: On the other side of the dyno is a single cylinder light-duty diesel engine based on a GM 1.6 liter diesel engine but with 3 cylinders deactivated and one cylinder installed over a single cylinder FEV engine block. The engine is instrumented with high speed cylinder pressure, intake pressure, exhaust pressure, and fuel rail pressure transducers from Kistler. Directly injected fuel flow is measured by a Micro Motion Coriolis flowmeter and pressurized via a production Bosch CP3 high pressure fuel pump. The engine has a Kistler crankshaft encoder.
Oil and coolant conditioning systems control the fluid stream temperatures for both engines in the Advanced Combustion and Heat Transfer Test Cell. Air flow is fed from a compressor and measured by an Alicat mass flow meter and controller and is heated and controlled to a setpoint temperature by PID control.
High speed measurements (cylinder, intake, exhaust, and fuel rail pressures) and low speed measurements (flowrates, temperatures, and subsystem pressures) are recorded with a custom National Instruments data acquisition system and engine controller. The LabView data acquisition and engine controller was written by the ACRF team and is one of the unique aspects of the single cylinder light-duty engine test cell facility because it allows complete control over engine operation and the experimental conditions. With this custom LabView code, the ACRF team can make changes to the data acquisition methodology, adding sensors or real-time calculations as needed to suit any particular experiment.
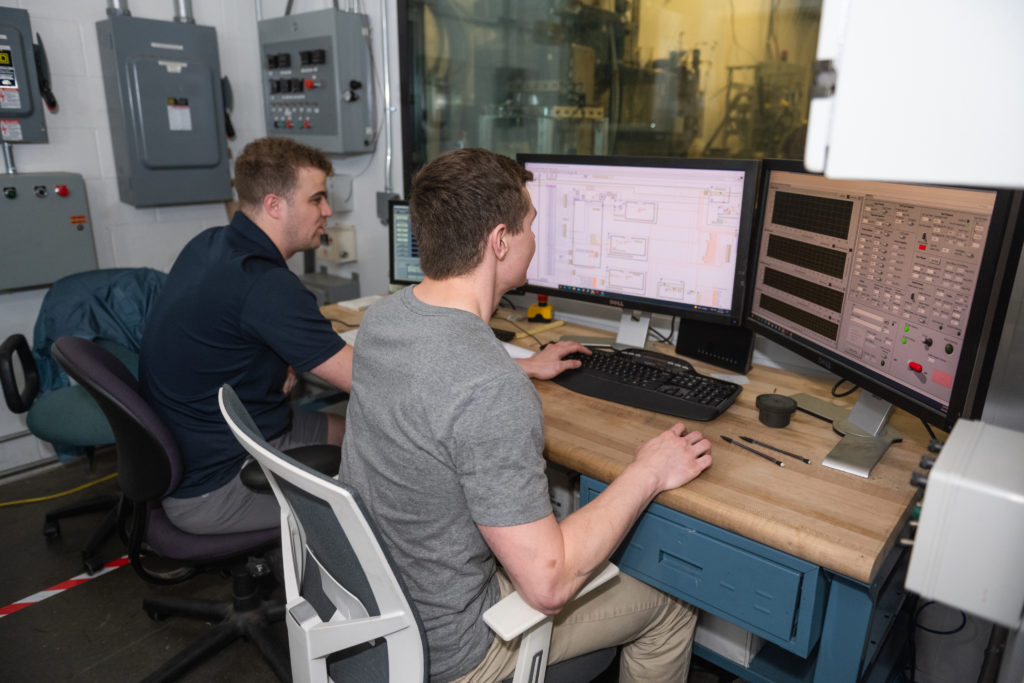
Although the Ricardo Hydra GDI engine is designed for spark ignition (SI) combustion, and the group has conducted projects related to SI combustion on that engine, the GDI engine is also capable of enabling a number of advanced combustion strategies and has been used for renewable alcohol combustion research. Similarly, the single cylinder FEV diesel engine is capable of conventional diesel combustion as well as advanced combustion concepts and has been used for renewable fuels studies.
The Advanced Powertrain (APT) Laboratory
The Advanced Powertrain (APT) test cell at Clemson University’s Department of Automotive Engineering was constructed in 2013.
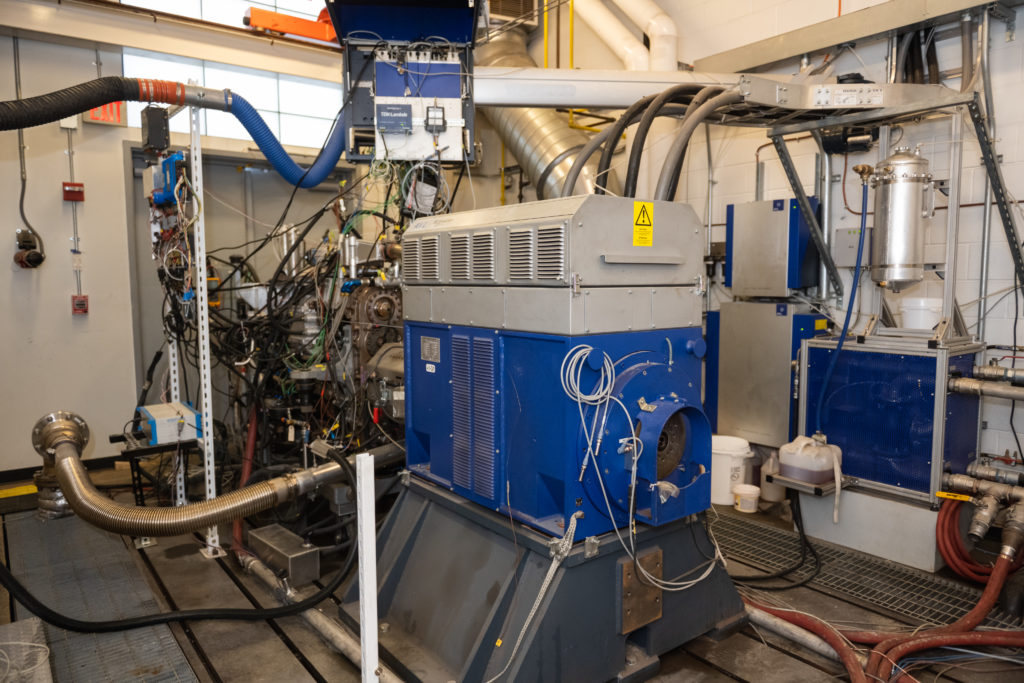
The vision for the test cell was to provide the capability to test light- to heavy-duty engines and various hybrid powertrain configurations through a combination of conventional engines and electric motors. The dynamometer is a double-ended transient AVL dynamometer rated at 440 kW (590 HP) and 1867 Nm of torque (continuously @ 4500rpm and 2250rpm, respectively) and capable of three millisecond response times with a torque accuracy of +/- 0.3%. The dyno and test cell are controlled by AVL’s PUMA Open integrated automation system which interfaces measuring devices and control and automation software. As such, it allows testing under any prescribed steady or transit conditions while orchestrating operation of test cell systems and data acquisition. In addition, it provides a link to open source model development and implementation, and interface with both dSPACE hardware and Matlab models. An IndiSet 672 Advanced Gigabit data acquisition system provides 24 high speed channels with 14-bit resolution and 800 kHz sampling rate, 32 multi-purpose analogue channels at 200Hz, 32 temperature inputs at 10Hz, and six counter inputs for speed and frequency measurements. The fuel measurement and conditioning system is capable of measuring 0-150kg/h with an uncertainty of less than 0.12% and temperature control from 10-80°C. Additionally, the fuel system is designed to be compatible with ethanol and methanol.
Vehicle Propulsion Laboratory (VPL)
The Vehicle Propulsion Lab is currently in the final stages of construction and commissioning. In terms of state approvals, budgets, architect plans, etc., the process has taken over two year. However, we are very excited for the final commissioning of the VPL. The VPL consists of two test chambers. The first to be commissioned is shown below and is specifically designed for high torque and high power, medium- and heavy-duty engines. The dyno is a double-ended AVL dyno capable of 3000 Nm of torque and 750 HP continuously. The coolant and oil conditioning system, data acquisition system and test cell automation, and fuel flow rate sensor are all from AVL.
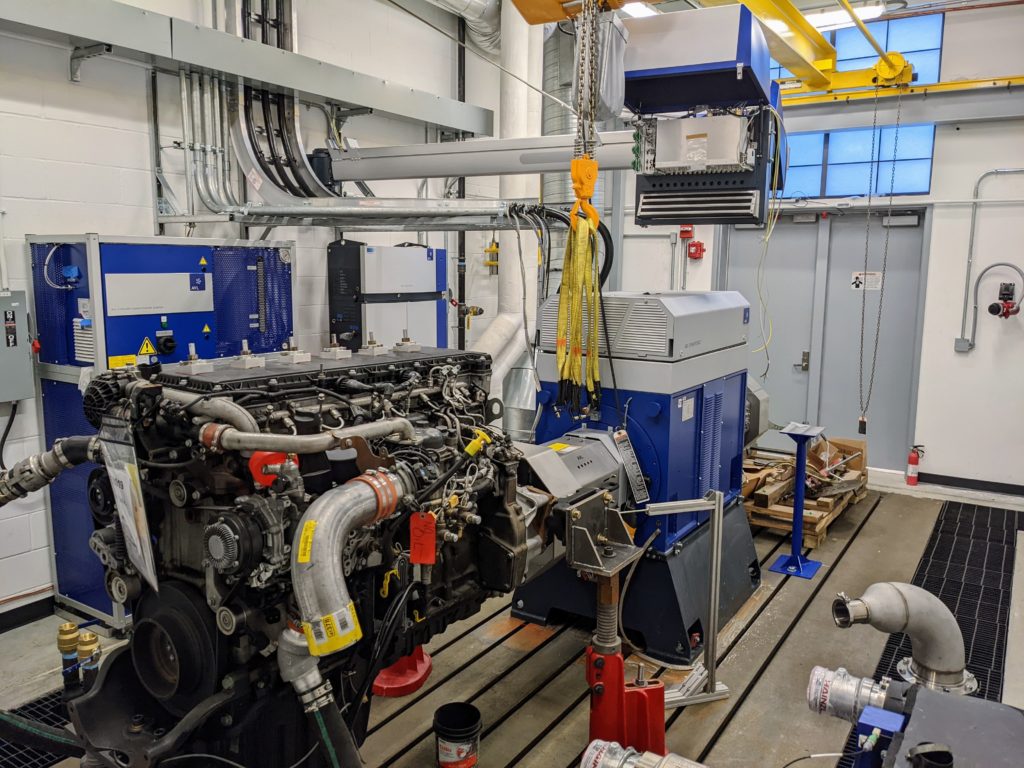
The second chamber associated with the VPL will be commissioned later in 2023. It will include a 250 kW battery tester emulator from AVL, and a 200 HP e-motor dyno. This electrified powertrain equipment will be used to test and characterize battery packs and electric motors from hybrid electric or electric vehicles. The second test chamber will be controlled through the same AVL PUMA test cell automation platform as the engine test cell shown above. This way, the two test cells can be coordinated and tested simultaneously to simulate hybridized vehicle using hardware-in-the-loop testing and characterization.
Chassis Dynamometer
The ACRF team has access to a state-of-art Renk Labeco 4-Wheel 500 HP chassis dyno contained in a Faist Semi-Anechoic Chamber.
The Renk system is a low-noise chassis dynamometer housed in a semi-anechoic chamber. This test facility is capable of driveline noise studies, fuel mileage/range investigations, emissions assessments, sound measurements, and all other chassis dynamometer and sound room-related test activities. The chassis dynamometer includes state-of-the art data acquisition from AVL or National Instruments as well as other advanced sensor systems and instrumentation including AVL FTIR or 5-gas emissions analyzers, engine crank angle resolved data acquisition and sensors, fuel flow rate measurements, and sound characterization equipment. A driver aid system can conduct specific, transient drive cycles (e.g., the EPA certification cycles) with the chassis dynamometer.
Emissions Characterization Equipment
Several different types of emissions characterization devices are available across all of the test cells. A HORIBA 7100D-EGR emissions bench is available to measures the CO, CO2, NOX, O2, and UHC emissions across the test cells. An AVL SESAM 4 FTIR provides an independent confirmation of exhaust emissions and speciates the unburned hydrocarbon (UHC) emissions into CH4, C2H2, C2H4, C2H6, C3H6, C3H8, C4H6, and C4H8. An AVL Micro Soot Sensor, an AVL Smoke Meter, and a Wager Opacity Meter can be used to measure the soot emissions in the exhaust. Finally, a differential mobility spectrometer (Cambustion DMS 500) is available to measure exhaust nanoparticle concentration and transient particulate size distributions across all of the test cells.
Palmetto High Performance Computing (HPC) Cluster
In addition to all of the experimental facility described above, Clemson has a world-class high-performance computing (HPC) cluster.
The Palmetto HPC cluster is comprised of 2115 compute nodes (totaling 32600 CPU cores) and 1278 NVIDIA GPUs. It has 10 and 25 Gbps Ethernet, and 56 and 100 Gbps Infiniband networks. The Palmetto HPC cluster is ranked 4th among the public academic institutions in the US on the Top500 list. It has been benchmarked at benchmarked at 1.4 PFlops (44,016 cores from Infiniband part of Palmetto).