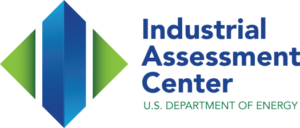
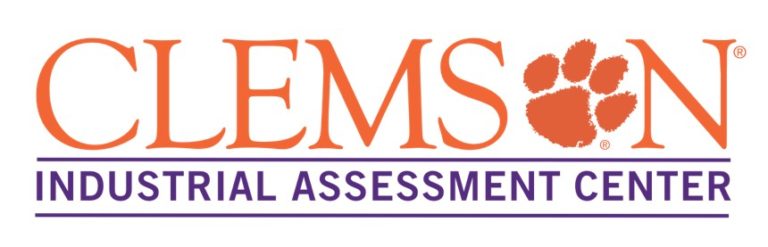
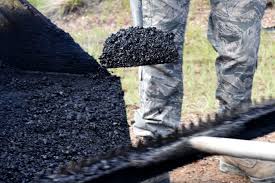
The production of asphalt is a highly energy-consuming process. Raw materials have to be thoroughly heated, mixed, and dried to create a quality product. Employing energy-saving measures can help keep costs under control, so this asphalt producer reached out to Clemson’s IAC to help them improve their energy efficiency.
As with other assessments, lighting was a key area for potential energy savings. This facility already had some LEDs and occupancy sensors installed. The assessment team recommended that they continue to upgrade their lighting until they had a full-LED system, and that they install occupancy sensors in all low usage areas. To avoid increased energy costs due to overlighting, it was recommended that the number of LED lamps in the fixtures be reduced so that the lighting was not too intense. It was also recommended that dusk-to-dawn sensors be installed on certain exterior lights to ensure that they were not on at all times. The total savings of this recommendation were $3,757, with an implementation cost of $4,162.
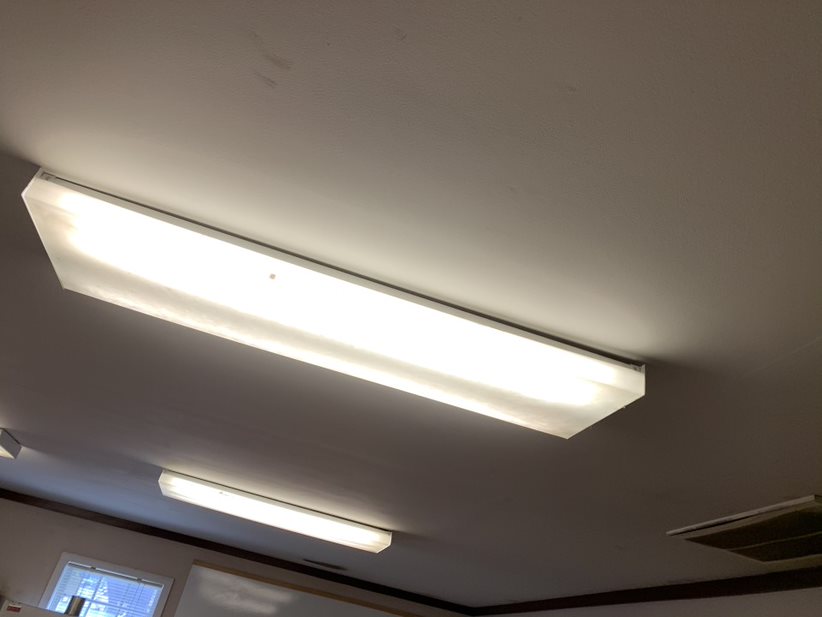
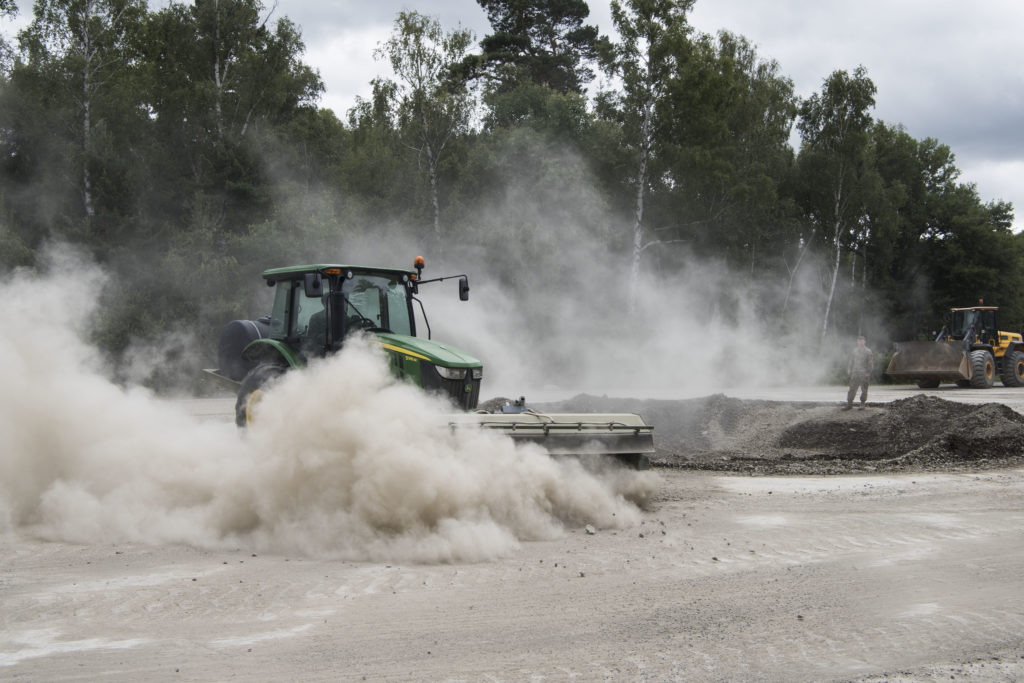
Dust is a common issue for asphalt plants. When heavy machinery is used to move materials, settled dust on roads can be kicked up and become a nuisance. Water is often sprayed to help with dust suppression. This producer had four sprinklers for this purpose. These sprinklers were left on during all hours of operation, even when materials were not being moved. The assessment team recommended installing a hose timer that would regulate how often the water sprayed. This would conserve water while still keeping the pavement wet. They also recommended that the height of the sprinklers be reduced so that they were not spraying into the raw material bins. This would decrease the moisture in the raw materials, thereby reducing the amount of energy required to process them. This recommendation was calculated to cost $1,750, with an annual savings of $1,166.
A large cylindrical drum is used to mix liquid asphalt at this facility. This drum has to be heated to a certain temperature to remove moisture from the mixture. The assessment team noted that the drum lacked insulation. Given its size, with the drum being 8 feet in diameter and 40 feet in length, this meant that large amounts of heat was escaping from it, forcing the producer to increase energy usage to maintain the required temperature. It was recommended that the drum be insulated, which would save $5,433 a year, with a total cost of $15,806.
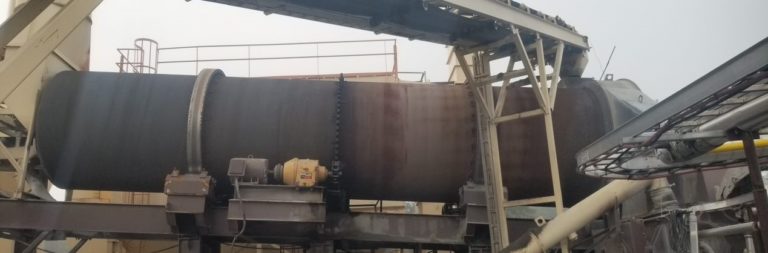
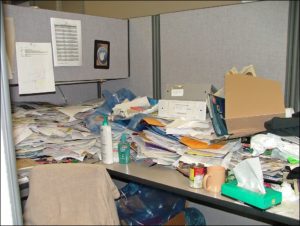
While reviewing this client’s utility bills, the assessment team observed that they were charged a late fee. Oversights like these lead to unnecessary expenses but can be easily avoided by keeping track of bills and staying organized. It was calculated that this client could save $103 per year by paying their bills on time, with an implementation cost of $0.
The asphalt producer implemented all of the recommendations described above. Before the assessment, they had an annual energy cost of $383,047. Through the implementation of Clemson IAC’s recommendations, that has been reduced to an estimated $372,588, once again showing that lowering energy consumption is a great way to save money.