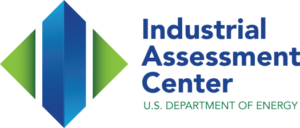
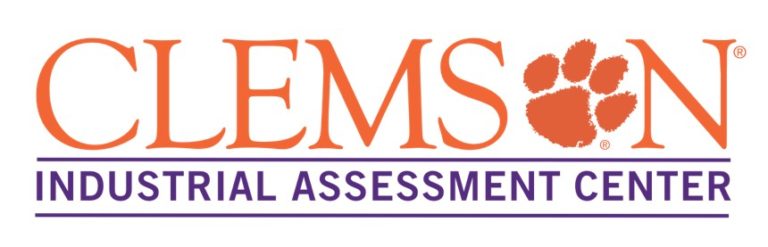
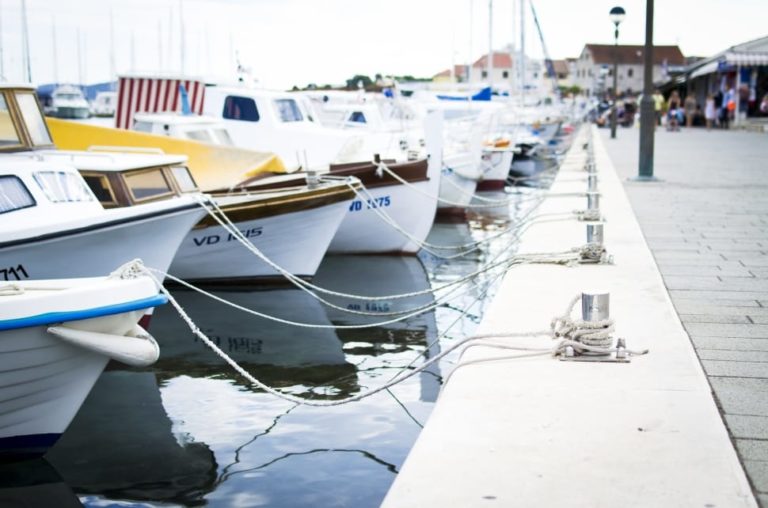
Boat manufacturers have to juggle creating a high-quality, safe product with keeping their costs down, a task made difficult by the size and complexity of boats that often have to be built in large factories, where energy costs can grow immensely if left unchecked. With guidance from Clemson University’s IAC, this boat manufacturer was able to control those costs without sacrificing product quality.
Efficient lighting is a vital part of creating energy efficient facilities. This manufacturer had installed LEDs but still used metal-halide and fluorescent lamps in a number of areas, so the assessment team recommended upgrading to a full-LED lighting system. While LEDs use much less energy than other fixtures, overlighting can still lead to unnecessary costs. That is why the team recommended reducing the number of LED bulbs in areas where the lighting was too intense as well as installing occupancy sensors in low usage areas. The total savings for this recommendation were calculated to be $35,719 per year, with an implementation cost of $44,796.
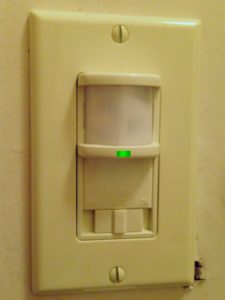
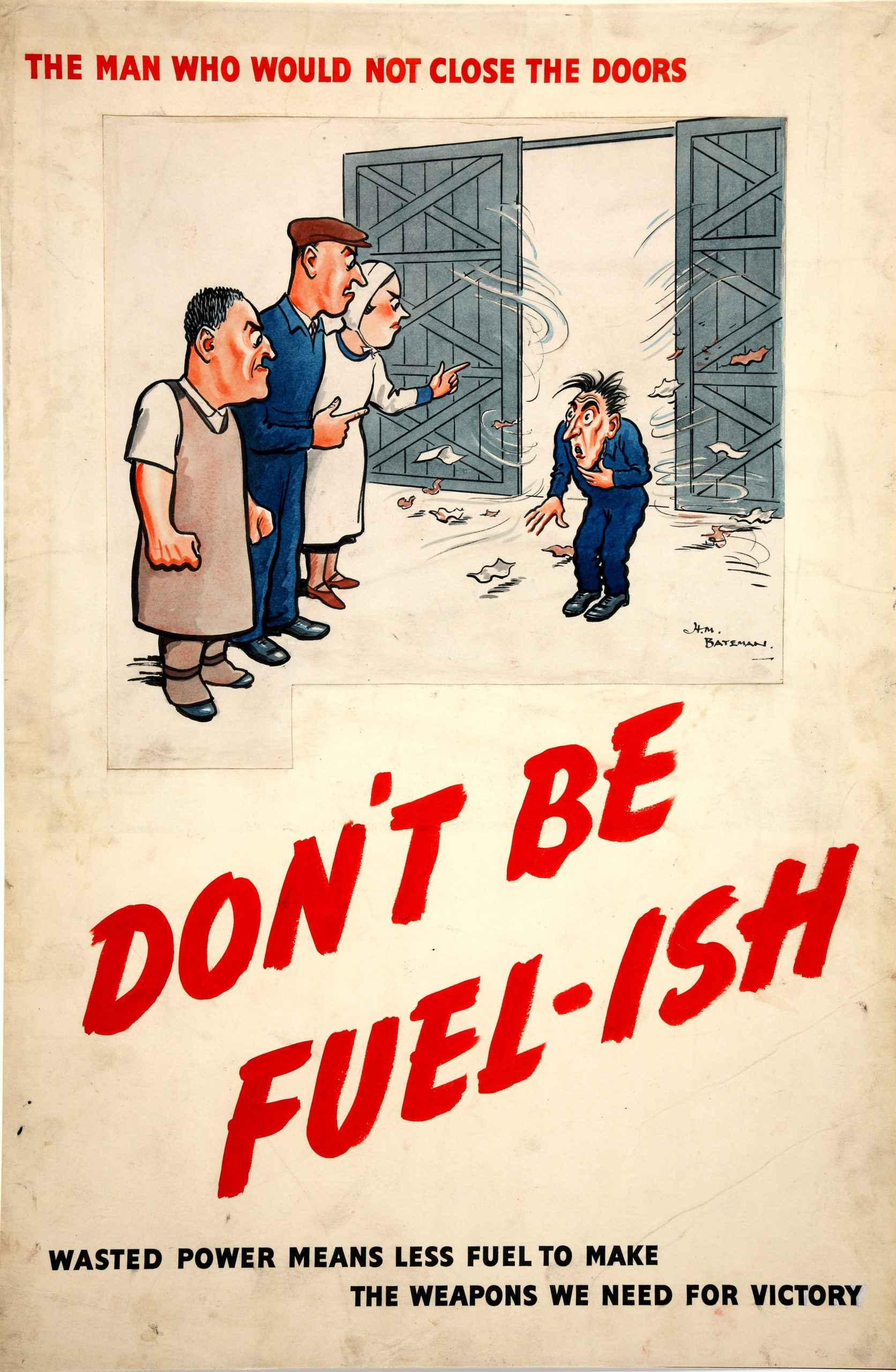
According to the U.S. Department of Energy, space conditioning (heating, cooling, and ventilating) accounts for about 40 percent of total commercial energy use in the United States. Oversights with HVAC systems often lead to energy costs that could have been avoided if greater care was taken. The assessment team noted that this manufacturer made sure to keep doors closed when they were not in use, which may seem like a small action but can go a long way in saving energy. The team also noted, however, that the plant used six spot heaters which were left on during non-working hours. The team calculated that $2,689 could be saved every year, with an implementation cost of $0, if the heaters were only used during working hours.
The complexity of compressed air systems often makes them a focal point of energy audits. Whether it be outdated technology or leaks, there is usually some way in which they can be improved. At this facility, the air compressor being used was oversized given the required amount of airflow. The assessment team recommended purchasing a smaller compressor and upgrading from a modulating compressor to a variable-frequency drive compressor, which can adjust its speed in response to air demand, thus saving energy. This would save the company $13,034 per year, with a one-time cost of $38,500.
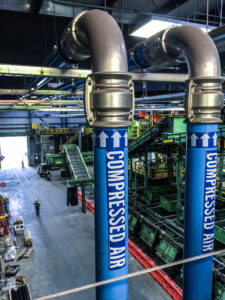
The manufacturer implemented all three of the recommendations described above. Before the assessment, they had a yearly energy cost of $185,363. With Clemson IAC’s help, that has been reduced to an estimated $133,921, showing just how important energy efficiency is for keeping costs low.