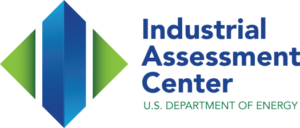
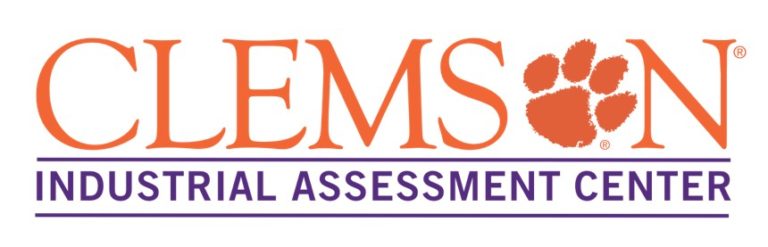
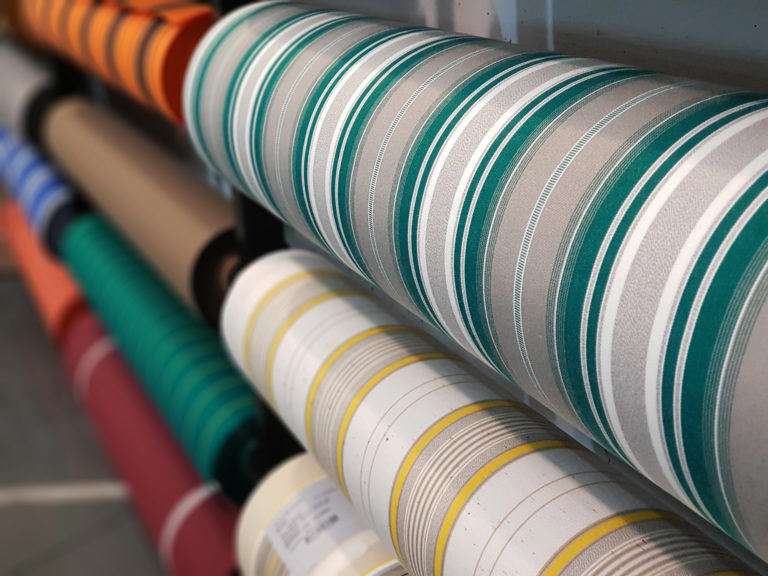
Carding, roving, spinning, doubling, weaving: just a few of the steps required to produce fabric. Such a long list of processes means that energy efficiency is incredibly important for fabric manufacturers, but creating a high-quality product while keeping costs low can be difficult. That’s why this manufacturer enlisted the help of Clemson University’s IAC for a free, energy-saving assessment.
According to the U.S. Department of Energy, about one-third of electric motors in the industrial and commercial sectors use belt drives, with the majority of them using V-belts. This manufacturer was not an exception. The issue with V-belts is that some of the work produced by the motor is lost as heat because the belt flexes and slips around pulleys. For this reason, the assessment team recommended upgrading to cogged belts, which have notches on their inner face that allow them to flex easier and consume less power, while also lasting longer than V-belts. The total cost of the cogged belts was calculated to be $28,500, with a yearly savings of $156,853.
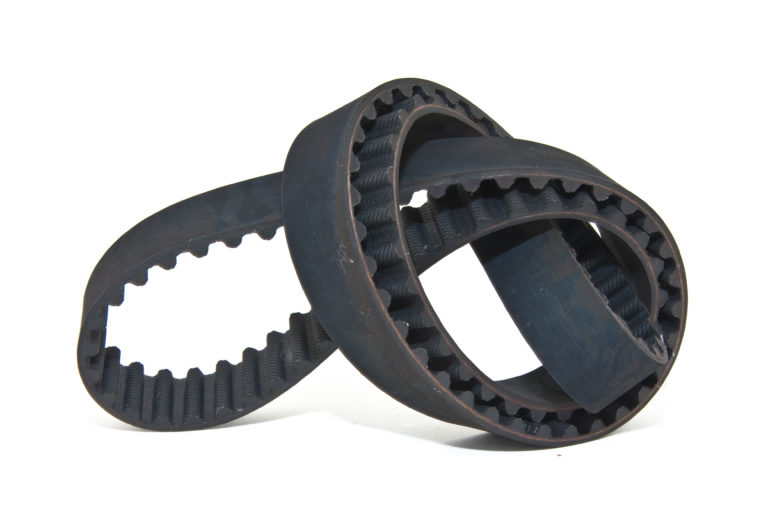
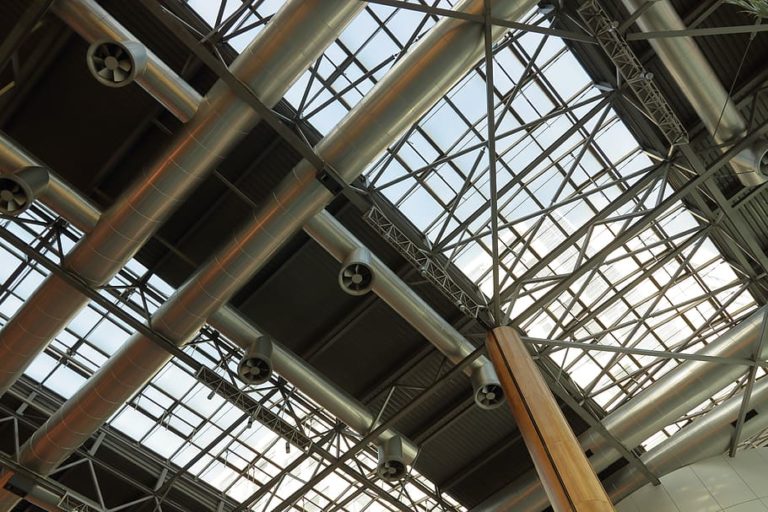
Lighting finds its way into just about every assessment and for good reason. Though the manufacturer had already installed some LEDs, they were still spending almost $100,000 every year on lighting. To help bring that number down, the assessment team recommended replacing fluorescent and metal-halide lamps with LEDs, installing occupancy sensors in low usage areas, expanding the use of natural lighting, and turning off the exterior floodlights during the day. This would save $46,306 per year, with an implementation cost of $184,601.
Boiler systems can be major energy consumers, which is why it is good practice to ensure that they are running efficiently. This manufacturer had well-insulated boiler piping, tuned their boiler several times a year, and made sure to shut off their boiler water pump when it was not in use. The assessment team found efficiency could be further improved through the installation of economizers. An economizer is a device that captures the heat of the boiler exhaust gas and transfers it to the water entering the boiler. This reduces the amount of energy needed for heating, as the water entering the boiler is preheated. Economizers were calculated to save this manufacturer $42,335 per year, with a cost of $15,500.
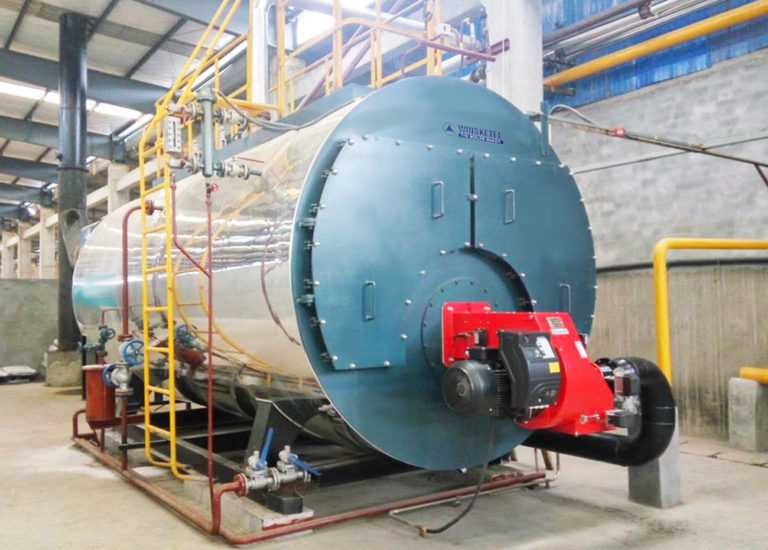
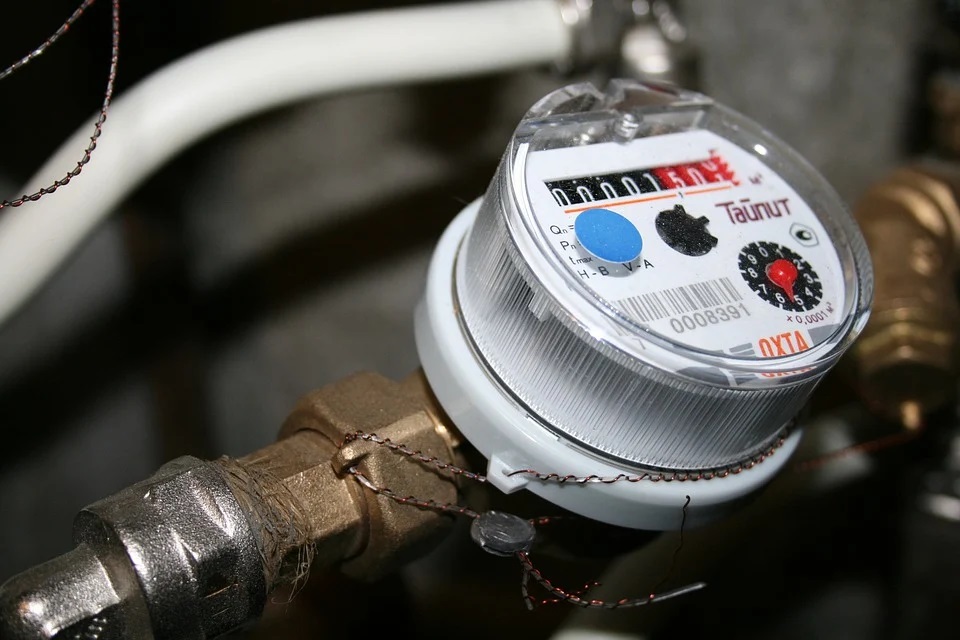
As water flows through a pipe, turbulence creates air bubbles. When a water meter tries to measure the volume of the flowing water, these bubbles are included in the reading. This leads to inflated costs because the billed amount of water is more than the amount of water actually used. Flow management devices are designed to fix this issue. They reduce turbulence, leading to fewer air bubbles and more accurate readings. It was recommended that the manufacturer install a flow management device on their water supply line, which would save an estimated $39,409 per year, with an implementation cost of $3,050.
Much like boiler systems, chiller systems can be quite energy-intensive. The two chillers used to supply cooling water to this plant were its third largest energy consumers, so the assessment team was determined to improve their efficiency. Their solution was to replace them with a cooling tower. Cooling towers remove heat from liquids by passing it into the atmosphere through evaporation. They require less energy to do the same amount of work as chillers, allowing for money to be saved over time. This recommendation was calculated to cost $42,000, with a yearly savings of $34,121.
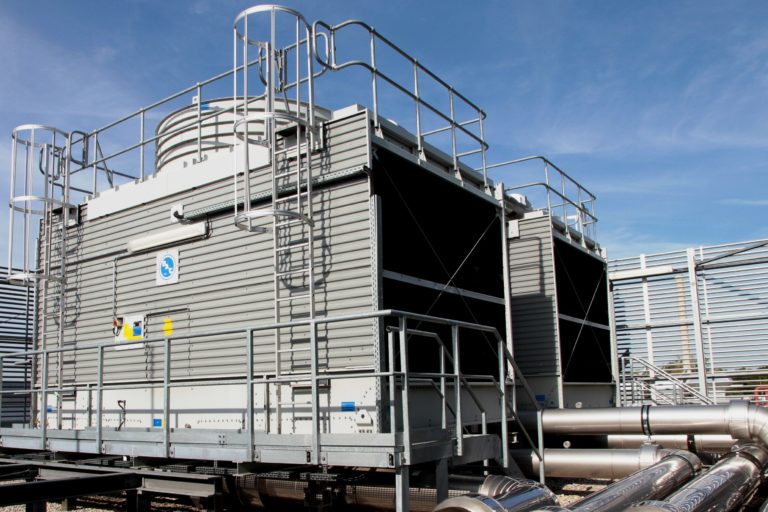
Three of the five recommendations described above were implemented. The manufacturer did not install economizers on the boilers that were assessed because their entire boiler system was upgraded, and they did not replace their chillers with a cooling tower because its visual appearance could possibly conflict with the rest of the facility. Before the assessment, this client’s annual energy cost was $4,482,272. With the implementation of these three recommendations, that has been reduced to an estimated $4,239,704.