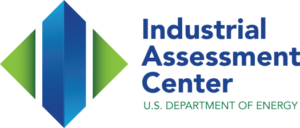
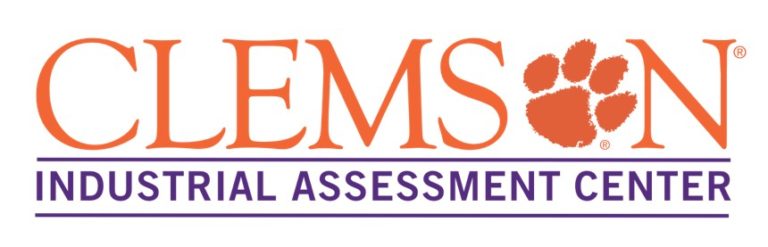
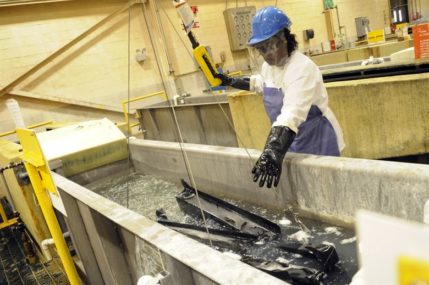
Metal finishing, the process of changing the surface of an object to improve its material properties, is quite energy-intensive. A variety of specialized equipment must be used to achieve satisfactory results. This means that energy costs can run high. With the help of Clemson University’s IAC, this particular shop was able to reduce those costs.
Immersion heaters are devices that are installed in containers to raise the temperature of a liquid. Metal finishing shops have many tanks that require heating, so they usually have several of these devices. The shop that is the focus of this study had 24. Such a high number of immersion heaters meant that there was likely an opportunity for energy savings, which the assessment team was determined to find. The team was able to calculate the minimum required energy consumption needed to heat the various solutions in the shop and compared that with the actual energy consumption of the immersion heaters. They found that some of the heaters were oversized and could be replaced by smaller units, while two heaters could be removed entirely. Implementing this recommendation was calculated to cost only $14,300, with a total savings of $40,277 per year.
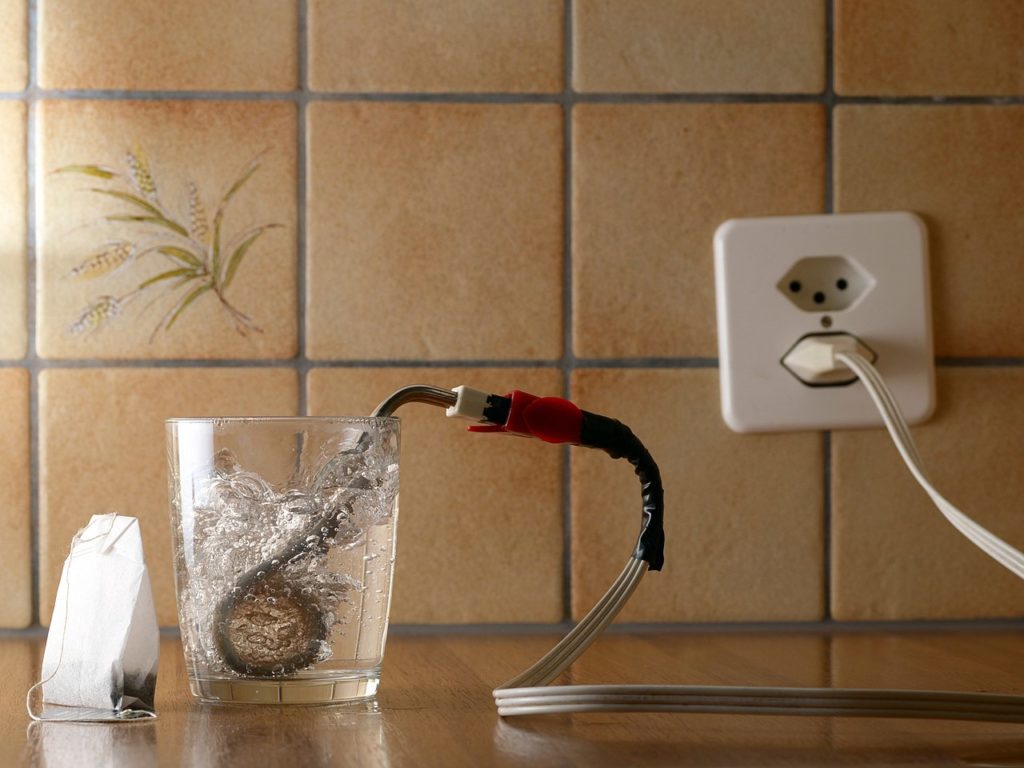
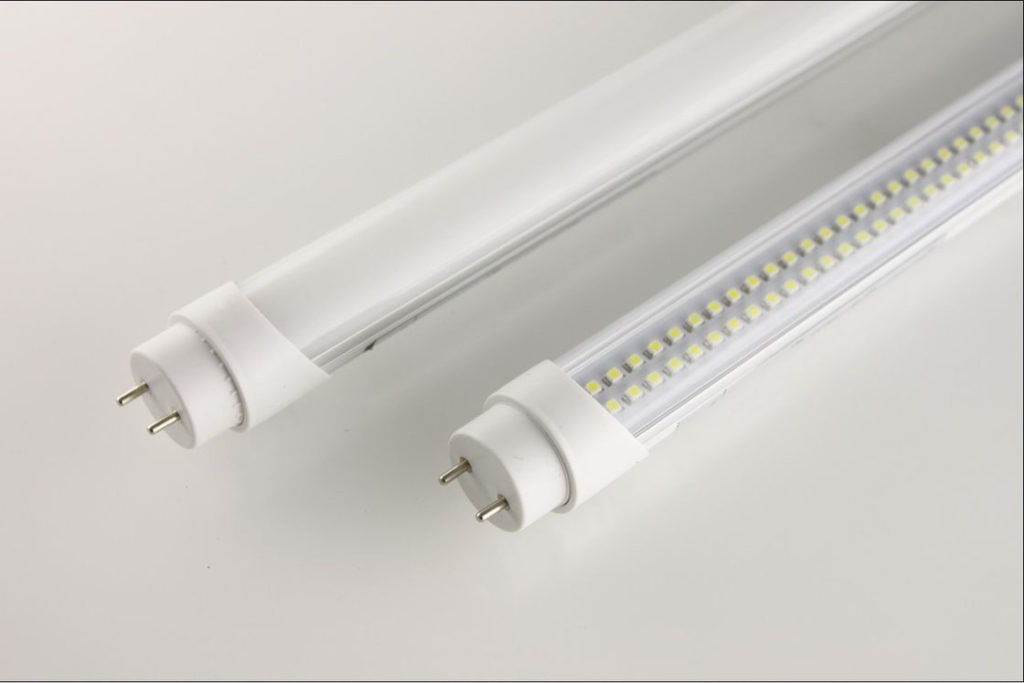
While at the plant, the assessment team noted that the shop planned to use natural light in several areas to save on lighting costs. Efficient lighting is an important part of reducing energy costs, as lighting is often one of the largest energy consumers for companies. The team recommended replacing metal-halide and fluorescent lamps with LED fixtures and installing occupancy sensors in low usage areas to further improve efficiency. The total savings for this recommendation was calculated to be $9,517 per year, with a one-time implementation cost of $9,852.
Compressed air is used in a wide variety of industrial applications and can be found in just about every facility. It is often accompanied by leaks, leading to large amounts of waste and increased energy costs. The assessment team identified four such leaks at this shop. They recommended fixing the leaks they had found as well as purchasing an ultrasonic leak detector and establishing a bi-weekly or monthly preventative maintenance program to identify and repair future leaks. This recommendation had an implementation cost of $2,080, with savings of $4,656 per year.
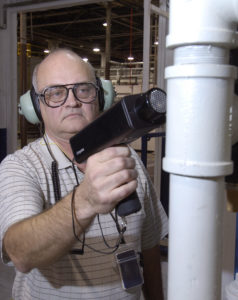
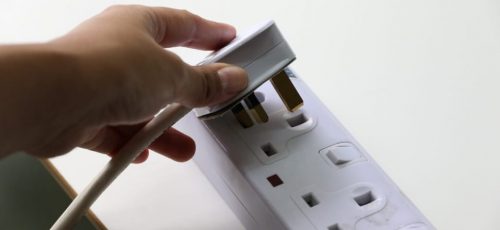
A “phantom load” is a small amount of stand-by power that an appliance uses when it is not running but is still plugged-in. It may seem negligible at first, but as time passes by, this lost energy can have a noticeable effect on costs. This facility had eight hoists which were continuously left plugged-in. The assessment team noted that these hoists are only used for about 30 minutes to one hour each day, so they recommended turning them off when they are not in use. Doing so would cost the company nothing but had an estimated savings of $386 per year.
Of the four recommendations described above, the company implemented all of them. Before the assessment, it had an annual energy cost of $174,879. The implementation of these energy saving measures has reduced that to an estimated $120,043, a significant decrease that shows just how important energy efficiency is.