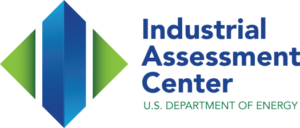
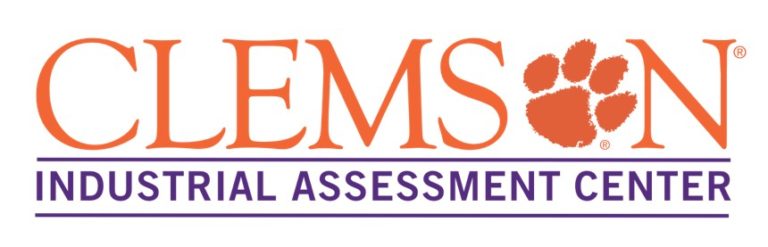
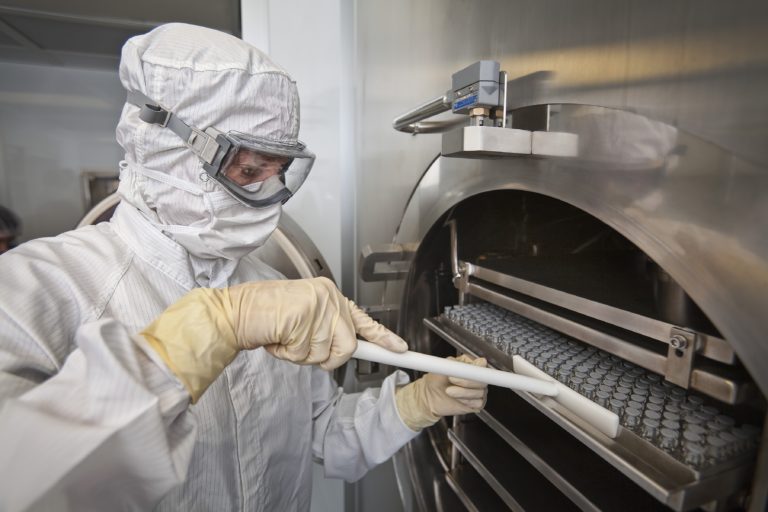
Pharmaceutical manufacturers have to adhere to some of the most stringent guidelines of any industry. Complying with these rules and regulations can be expensive, so they have to identify where they can safely cut costs in order to maximize profit. This manufacturer aimed to save money by reducing their energy consumption, so they contacted Clemson’s IAC for an energy-saving assessment.
One of the best ways to improve efficiency in a facility is to install LEDs in place of less efficient lighting. This manufacturer had already upgraded some interior and exterior fixtures, so the assessment team recommended they continue until all of them had LEDs. A way to improve upon the efficiency of LEDs is to make sure that they are not too bright and are only on when needed. That is why it was recommended that illumination be reduced in areas where the lighting was too intense and for occupancy sensors to be installed in low usage areas. The total cost of this recommendation was $15,294, with an annual savings of $17,417.
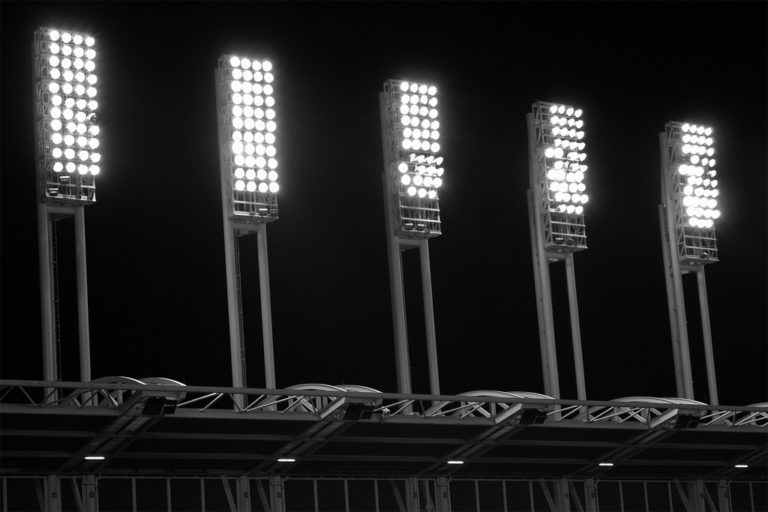
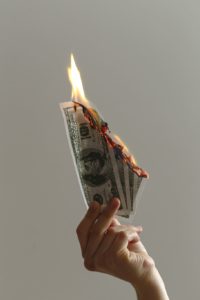
Leaks are like burning money: you’re left with less cash and nothing to show for it. While even the most inefficient and costly manufacturing processes serve a purpose, leaks just waste energy and drive up costs. That is why it is so important to identify and quickly seal them. During this assessment, a steam leak was discovered in a courtyard. The assessment team was able to estimate the amount of steam being released by the leak, which allowed them to calculate how much it was costing the company. They determined that fixing the leak would save $3,542 per year, with a cost of $2,040.
The assessment team also found thirteen compressed air leaks at the facility. These often overlooked leaks may seem insignificant, but they can add up to large amounts of waste over time. That is why the assessment team recommended sealing the leaks that they had found as well as purchasing an ultrasonic leak detector and establishing a monthly preventative maintenance program to identify and repair future leaks. This was estimated to cost $2,080, with a yearly savings of $647.
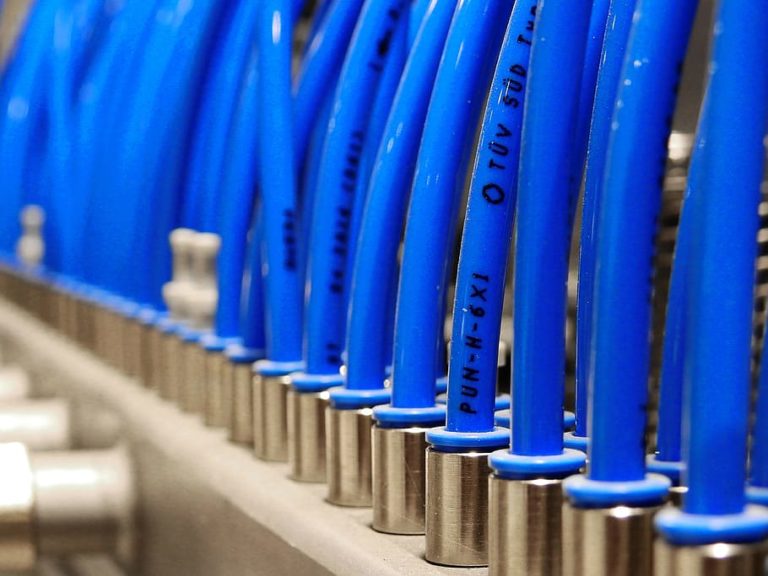
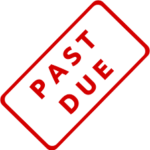
The manufacturer had several months where their utility bills were not paid on time. Small oversights like this can quickly add up to thousands of dollars in fees that could have been easily avoided. It was calculated that the manufacturer would save $2,971 per year if they paid their bills on time, with an implementation cost of $0.
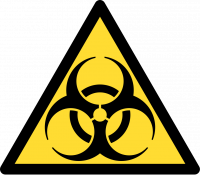
The production of pharmaceuticals creates hazardous waste, which has to be carefully disposed of. This can be quite costly, especially when large amounts of product is being made. This manufacturer was spending over $1,000,000 a year on waste disposal, so the assessment team was determined to help reduce this cost. They learned that 55-gallon drums were being used for waste disposal. These drums were sealed off for transport at the time of disposal regardless of how filled they were, leading to many unfilled drums and wasted money. It was recommended that the manufacturer move towards using 330-gallon bulk containers made of high-density polyethylene, which allows them to be washable for reuse. These containers have the same volume as six drums but are more cost-effective. It was determined that the cost of this recommendation is simply the logistical costs of switching from drums to bulk containers, which was estimated to be $600. The total savings was calculated to be $143,304 per year.
Of the five recommendations described above, the manufacturer implemented three of them. They did not upgrade their lighting system or change their method of waste disposal due to their facility partially closing. Before the assessment, this client’s annual energy cost was $1,853,658. With the help of Clemson’s IAC, that has been reduced to an estimated $1,846,498.