Engine and transmission systems are major sources of vibration in a vehicle.
They have a direct impact on the vehicle ride and comfort.
Conventional vibration isolation systems are passive systems with inherent limitations. Active Vibration Control (AVC) systems overcome many of these limitations using electronic controls.
Limitations of passive vibration isolation systems
It is important to first understand the limitations of the passive vibration isolation systems by understanding the relationship between damping and isolation. Consider the following plot for a regular spring damper system.
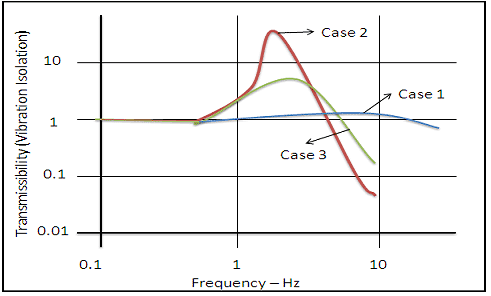
CASE 1 : When the damping is strong, the vibration isolation is low.
CASE 2 : When the damping is weak, a resonance peak is observed at some frequencies.
CASE 3 : A classical mount design tries to achieve a compromise between good damping and acceptable isolation.
Typically engines use passive rubber isolators that support the engine, limiting engine movement and isolating the engine from the chassis. Semi-active vibration damping is used in some vehicles. An example of this is the Porsche911 Dynamic Engine Mount System. In this system, engine mounts employ a magnetizable fluid and an electrically generated magnetic field that provide variable stiffness.
Working Principal of a Fully-Active Vibration Isolation System
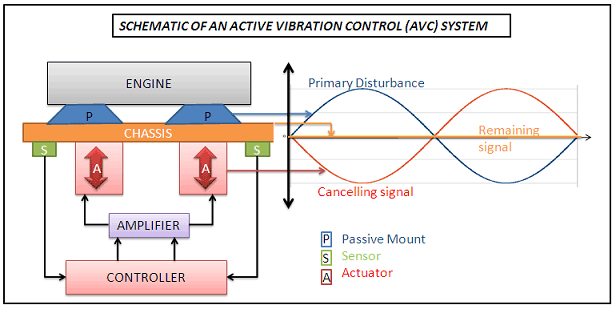
Active vibration isolation systems are closed loop feedback systems consisting of sensors, controllers and actuators. In most cases, the sensor is a piezoelectric accelerometer that senses the excitation of the passive engine mount. The acceleration signal is then processed by the controller. The controller generates a canceling signal that is fed to a power amplifier. The amplifier converts the controller's low-voltage signal to an actuator current. The actuators in most cases are electromagnetic transducers. The force generated by the actuator cancels the primary disturbance signal resulting in near zero chassis vibration.