Ankit Agarwal
Postdoctoral Researcher
Department of Automotive Engineering
Clemson University International Center for Automotive Research
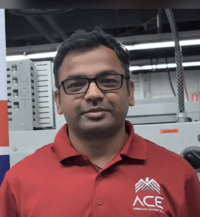
My decision to choose industry-oriented research as a professional career in the long term is based on moral values, outlook, and personal experiences. I always had a passion for learning how machines work and the evolution of new technologies from school days. This motivated me to choose Mechanical Engineering as a discipline during undergraduate studies. The laboratories of the undergraduate program were the most exciting part and helped me to develop an interest towards manufacturing processes and systems. I spent considerable time appreciating automation trends and CNC machine tools during undergraduate and postgraduate studies. Considering long-term career interests in the domain of advanced manufacturing, I opted for a doctoral degree program in the area of CNC Machine Tools and CAD/CAM at Indian Institute of Technology Jodhpur, India after postgraduate studies. The doctoral degree program helped me to transform from an enthusiastic student to a thoughtful researcher and appreciate the multidisciplinary nature of current research trends. I have developed good knowledge base in the domain of advanced machining, geometric tolerances, and application of machine learning in manufacturing. In subsequent years of professional career, I look forward to contribute meaningfully in the areas integrating smart manufacturing and data sciences.
Research Work
HG-XAI: Human Guided eXplainable Artificial Intelligence
The HG-XAI integrates human expertise with the CNN-based Efficient-Net-b0 model to identify tool wear states efficiently. The work employs two XAI concepts to integrate human expertise effectively with the Efficient-Net-b0 model. Firstly, the feature map depicting the region of an input image contributing the most to the identified wear state is extracted through the last convolutional layer using the Gradient Class Activation Maps (Grad-CAM) technique. Secondly, classification probabilities 𝑃 = [𝑃1, 𝑃2, 𝑃3, 𝑃4] of all wear states are recorded from the Softmax layer of the Efficient-Net-b0 model. The maximum classification probability (𝑚𝑎𝑥(𝑃 )) value is used to decide the human involvement in identifying the tool wear state. If the 𝑚𝑎𝑥(𝑃 ) is greater than the predefined threshold value, the classification result of the Efficient-Net-b0 model is considered as the final tool wear state. Alternatively, HG-XAI will seek the assistance of human expertise in deciding the tool wear state. The HG-XAI displays the captured image, feature map, and probability values of the two highest-ranked wear states to the human for making the final decision.
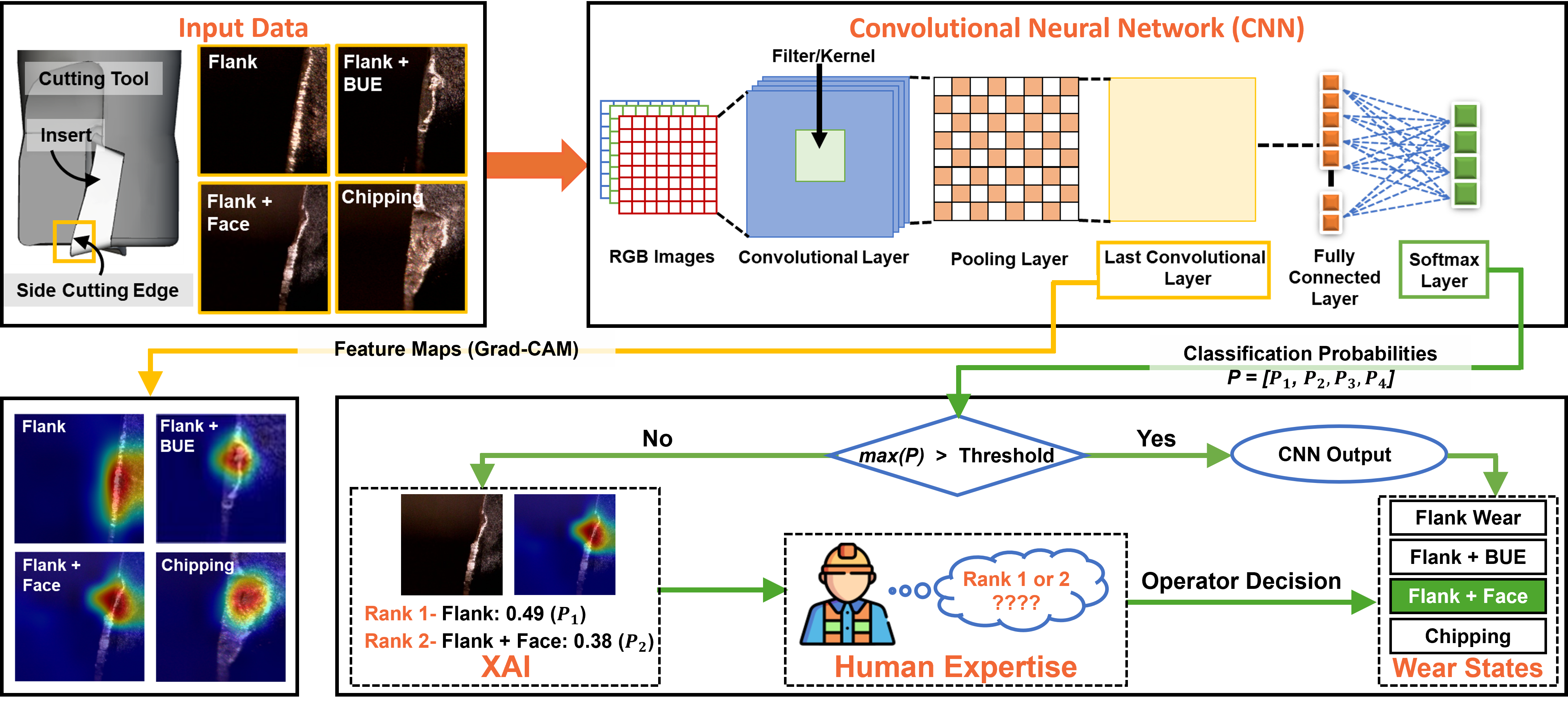
Design-as-a-Service (DaaS)
Cloud-based Design and Manufacturing (CBDM) has emerged as an enabler for product realization by integrating various service-based models. However, the existing framework does not thoroughly support the innovation ecosystem from concept to product realization by formally addressing economic challenges and human skillset requirements. Our work considers the augmentation of the Design-as-a-Service (DaaS) model into the existing CBDM framework for enabling systematic product innovations. The DaaS model proposes to connect skilled human resources with enterprises interested in transforming an idea into a product or solution through the CBDM framework. The model presents an approach for integrating human resources with various CBDM elements and end-users through a service-based model. It is established that the DaaS has the potential for rapid and economical product discovery and can be readily accessible to SMEs or independent individuals.
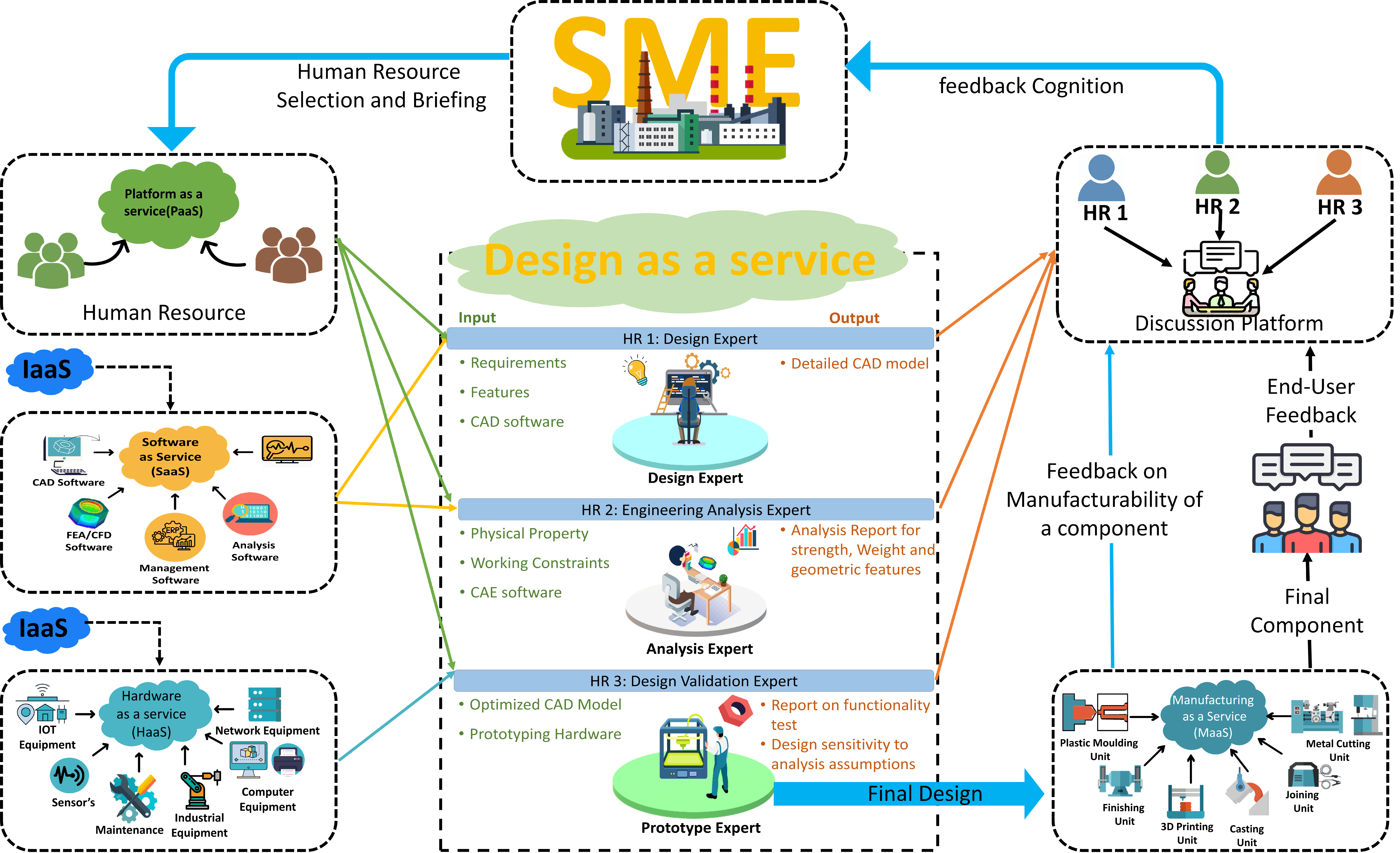
Contrived Tool Wear Methodology
The stochastic nature of the tool wear makes it difficult to model and requires a significant number of cutting tests and machining of a large volume of material that incurs high cost and time. To avoid such time-consuming and cost-intensive cutting tests, the methodology is developed to generate tool wear artificially using a grinding process. The tools are worn by taking several passes over a grinding wheel in a controlled environment. The performance of contrived and naturally worn tools is compared by analyzing various parameters such as process force, wear topography and chip formation, which shows a good agreement. Also, it is realized that the contrived wear method enables a consistent starting point while studying any wear stage of the worn-out tool, thereby decoupling the stochastic nature of tool wear.
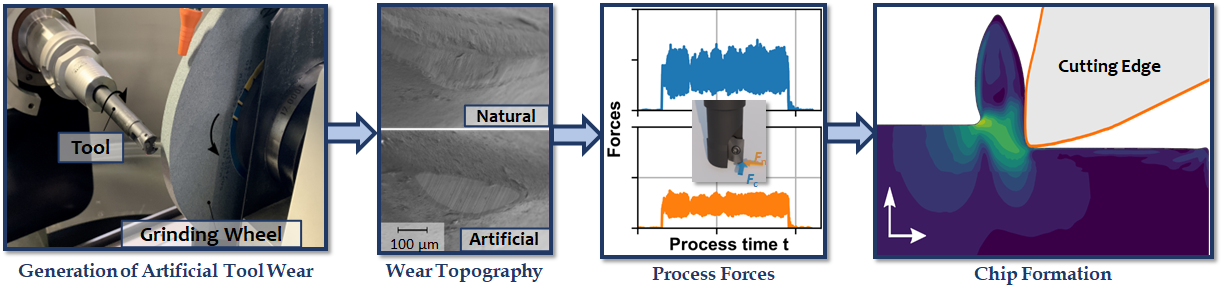
Evolution of Tool Wear in Machining of Inconel 718
In recent years, machine vision techniques are becoming predominant for various manufacturing applications, such as identifying machine setup abnormalities, tool status monitoring, and machined surface analysis. An image recognition-based method is developed to measure the flank wear width/area during trochoidal milling of Inconel 718. The proposed method is implemented as an automated computational program, and a series of experiments are performed to analyze the progression of the tool flank wear area over the volume of material removed. The developed image processing method is able to evaluate the flank wear width/area accurately and efficiently.
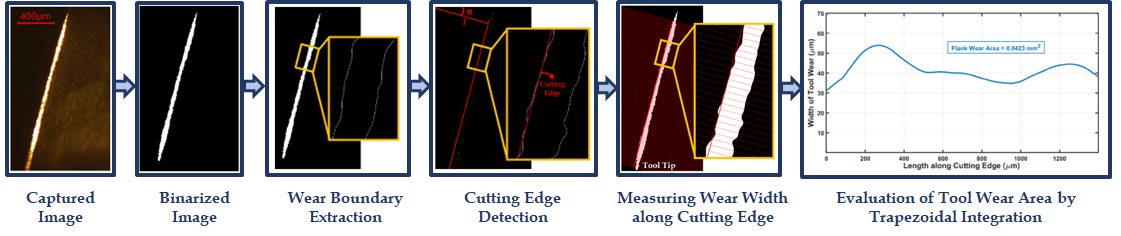
Stochastic Machining
The concept of stochastic machining aims to introduce stochastic nature to the toolpath. The toolpath strategy involves random movement of the tool over the surface. It is hypothesized that the random motion of the tool avoids resonance by continuously varying the direction of cutting force and thereby reduces chatter. Also, the tool often passes over already machined regions of the workpiece and enables rapid dissipation of heat. The stochastic toolpath strategy devised herein is applied to generate toolpath for 3-axis ball-end milling of 2-Dimensional (2D) and free form surfaces.
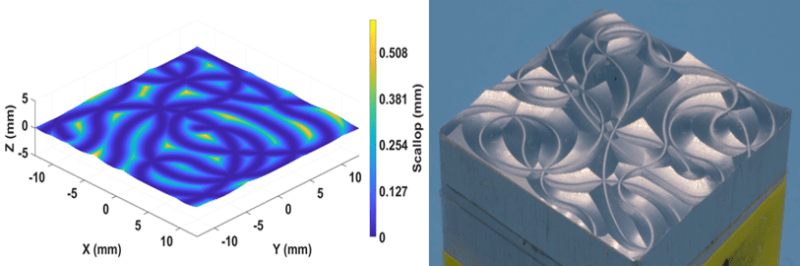
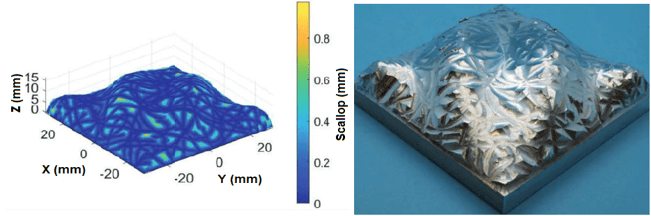
Machining of Thin-walled Components
-
Predictive Framework for Estimation of Geometric Tolerance
A computational framework is realized to estimate static tool and workpiece deflection-induced geometric tolerances during end milling of thin-walled straight and constant curvature or circular components. The framework requires systematic integration of several computational models to predict cutting forces, estimate coordinates representing distorted machined surface due to the tool and workpiece deflections, and a mechanism to transform distorted coordinates into geometric tolerances for straight and circular thin-walled components.

-
Control of Geometric Tolerances
The rigidity of the thin-walled component varies considerably with the change of workpiece curvature and reduces as machining progresses due to material removal. This variation leads to a violation of geometric tolerances envisaged by the designer. The research work devised a Rigidity Regulation Approach (RRA) to obtain the semifinished geometry at the end of roughing operation. The finish cutting sequence is performed subsequently on the geometry for achieving optimal geometric tolerances.

Publications
Journal
- Aitha Sudheer Kumar, Ankit Agarwal, Vinita Gangaram Jansari, K.A. Desai, Chiranjoy Chattopadhyay, Laine Mears, Realizing on-machine tool wear monitoring through integration of vision-based system with CNC milling machine, Journal of Manufacturing System, 78, 283-293, 2025.
- Aitha Sudheer Kumar, Ankit Agarwal, Vinita Gangaram Jansari, K.A. Desai, Chiranjoy Chattopadhyay, Laine Mears, HG-XAI: Human-guided tool wear identification approach through augmentation of explainable artificial intelligence with machine vision, Journal of Intelligent Manufacturing, 2024.
- Ankit Agarwal, Karan Bhuta, Tyler Grimm, Laine Mears, ‘Investigating the effect of nanobubble-based cutting fluid on tool wear and cutting forces in milling of Inconel 718’ Manufacturing Letters 41, 1676-1682, 2024.
- Nilesh Ashok Kharat, Ankit Agarwal, Tyler Grimm, Laine Mears, Investigation of stochastic toolpath strategy in 3-axis ball-end milling of 2D and free-form surfaces, Proceedings of the IMechE, Part B: Journal of Engineering Manufacture, 238(11), 1709-1723, 2024.
- Aash M. Shah, Ankit Agarwal, Laine Mears, Tool wear area estimation through in-process edge force coefficient in trochoidal milling of Inconel 718, Manufacturing Letters 35, 391-398, 2023.
- Nils PotthoffAnkit AgarwalFlorian WöstePetra Wiederkehr Laine Mears, Evaluation of contrived wear methodology in end milling of Inconel 718, ASME Journal of Manufacturing Science and Engineering, 145(10), 101002, 2023.
- Ankit Agarwal, Pratik C. Sorathiya, Shubham Vaishnav, K. A. Desai, and Laine Mears, Design-as-a-service framework for enabling innovations in small-and medium-sized enterprises, ASME Journal of Mechanical Design 145(4), 044501, 2023.
- Ankit Agarwal, Nils Potthoff, Aash M. Shah, Laine Mears, and Petra Wiederkehr, Analyzing the evolution of tool wear area in trochoidal milling of Inconel 718 using image processing methodology, Manufacturing Letters, 33, 373-379, 2022.
- Nils Potthoff, Ankit Agarwal, Florian Wöste, Jan Liß, Laine Mears, and Petra Wiederkehr, Experimental and simulative analysis of an adapted methodology for decoupling tool wear in end milling, Manufacturing Letters, 33, 380-387, 2022.
- Ankit Agarwal, K.A. Desai, Effect of component configuration on geometric tolerances during end milling of thin-walled parts, The International Journal of Advanced Manufacturing Technology, 118(11-12), 3617–3630, 2022.
- Ankit Agarwal, K.A. Desai, Rigidity regulation approach for geometric tolerance optimization in end milling of thin-walled components, ASME Journal of Manufacturing Science and Engineering, 143(11), 111006, 2021.
- Ankit Agarwal, K.A. Desai, Modeling of flatness error in end milling of thin-walled components, Proceedings of the IMechE, Part B: Journal of Engineering Manufacture, 235(3), 543-554, 2021.
- Ankit Agarwal, K.A. Desai, Predictive framework for cutting force induced cylindricity error estimation in end milling of thin-walled components, Precision Engineering, 66, 209-219, 2020.
- Ankit Agarwal, K.A. Desai, Importance of bottom and flank edges in cutting force models for end milling operation, The International Journal of Advanced Manufacturing Technology, 107(3), 1437-1449, 2020.
- Shubham Vaishnav, Ankit Agarwal, K.A. Desai, Machine learning based instantaneous cutting force model for end milling operation, Journal of Intelligent Manufacturing, 31(6), 1353-1366, 2020.
- Neha Arora, Ankit Agarwal, K.A. Desai, Modeling of static surface error in end milling of thin-walled geometries, International Journal of Precision Technology, 8(2-4), 107-123, 2019.
Conferences
- Ankit Agarwal, Aitha Sudheer Kumar, Vinita Gangaram Jansari, K.A. Desai, Laine Mears, ‘Improving vision-based tool wear state identification under varying lighting conditions using human guided-explainable AI approach’, 53rd North American Manufacturing Research Conference 2025. (Accepted for Presentation)
- Sujay BJ, Swarit Anand Singh, Ankit Agarwal, K.A. Desai, Laine Mears, ‘Identifying tool wear stages in turning process through machined surface image analysis using convolutional neural network’, 53rd North American Manufacturing Research Conference 2025. (Accepted for Presentation)
- Tyler Grimm, Ankit Agarwal, Laine Mears, ‘Brief Paper: Electric pulse assisted milling’, ASME Manufacturing Science and Engineering Conference 2025. (Accepted for Presentation)
- Amaninder Gill, Ankit Agarwal, Vijayanth Tummala, Seung-Jin Lee, Laine Mears, ‘Comparison of explainable AI for image classification to human perception: A case study of threaded fasteners’, ASME International Mechanical Engineering Congress & Exposition (IMECE), Portland, USA, November 2024.
- Shubham Vaishnav, Ankit Agarwal, Pratik C. Sorathiya, K. A. Desai, Laine Mears, ‘Research2market Connect: Cloud-based platform to connect academic research with SMEs for accelerated innovations‘, ASME International Design Engineering Technical Conferences & Computers and Information in Engineering Conference (IDETC/CIE), Washington, USA, August 2024.
- Aitha Sudheer Kumar, Ankit Agarwal, Vinita Gangaram Jansari, K. A. Desai, Chiranjoy Chattopadhyay, Laine Mears, ‘Vision-Based Tool Wear Classification During End-Milling of Inconel 718 Using a Pre-Trained Convolutional Neural Network’, ASME International Mechanical Engineering Congress & Exposition (IMECE), New Orleans, Louisiana, USA 2023, pp. V003T03A016.
- Ankit Agarwal, K.A. Desai, Amalgamation of physics-based cutting force model and machine learning approach for end milling operation, 53rd CIRP Conference on Manufacturing Systems (CIRP CMS), Chicago, USA, July 2020 Procedia CIRP, 93, 1405-1410.
- Ankit Agarwal, K.A. Desai, Tool and workpiece deflection induced flatness errors in milling of thin-walled components, 53rd CIRP Conference on Manufacturing Systems (CIRP CMS), Chicago, USA, July 2020 Procedia CIRP, 93, 1411-1416.
- Ankit Agarwal, K.A. Desai, Effect of workpiece curvature on axial surface error profile in flat end milling of thin-walled components, 48th SME North American Manufacturing Research Conference, (NAMRC 48), Cincinnati, USA, June 2020 Procedia manufacturing, 48, 498-507.
- Neha Arora, Ankit Agarwal, K.A. Desai, Modeling of static surface error in end milling of thin-walled geometries, 10th International Conference on Precision, Meso, Micro and Nano Engineering (COPEN 10), IIT Madras, December 2017.
Work Experience
Postdoctoral Fellow (March 2021 – Present)
Department of Automotive Engineering
Clemson University International Center for Automotive Research
Greenville, SC, USA
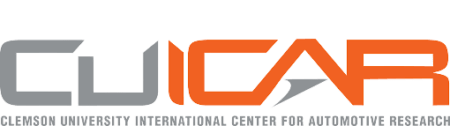
Assistant Professor (January 2021 – March 2021)
Department of Manufacturing Engineering
Central Institute of Petrochemicals Engineering & Technology
Ahmedabad, India
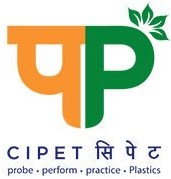
Teaching Assistant (January 2016 – December 2020)
Department of Mechanical Engineering
Indian Institute of Technology Jodhpur
Rajasthan, India
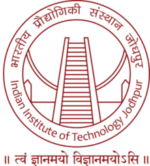