Electrically Assisted Manufacturing
Electrically assisted manufacturing (EAM) is broadly defined as the direct application of an electric current or electromagnetic field to a workpiece during a manufacturing process, which covers applications such as forming, forging, cutting, sintering, and heat treatment. In addition to resistive heating and electromigration, various anomalous effects, termed electroplastic effects, have been discovered. For over 60 years, the existence of these effects has been debated and several theories have been proposed to explain these observed behaviors.
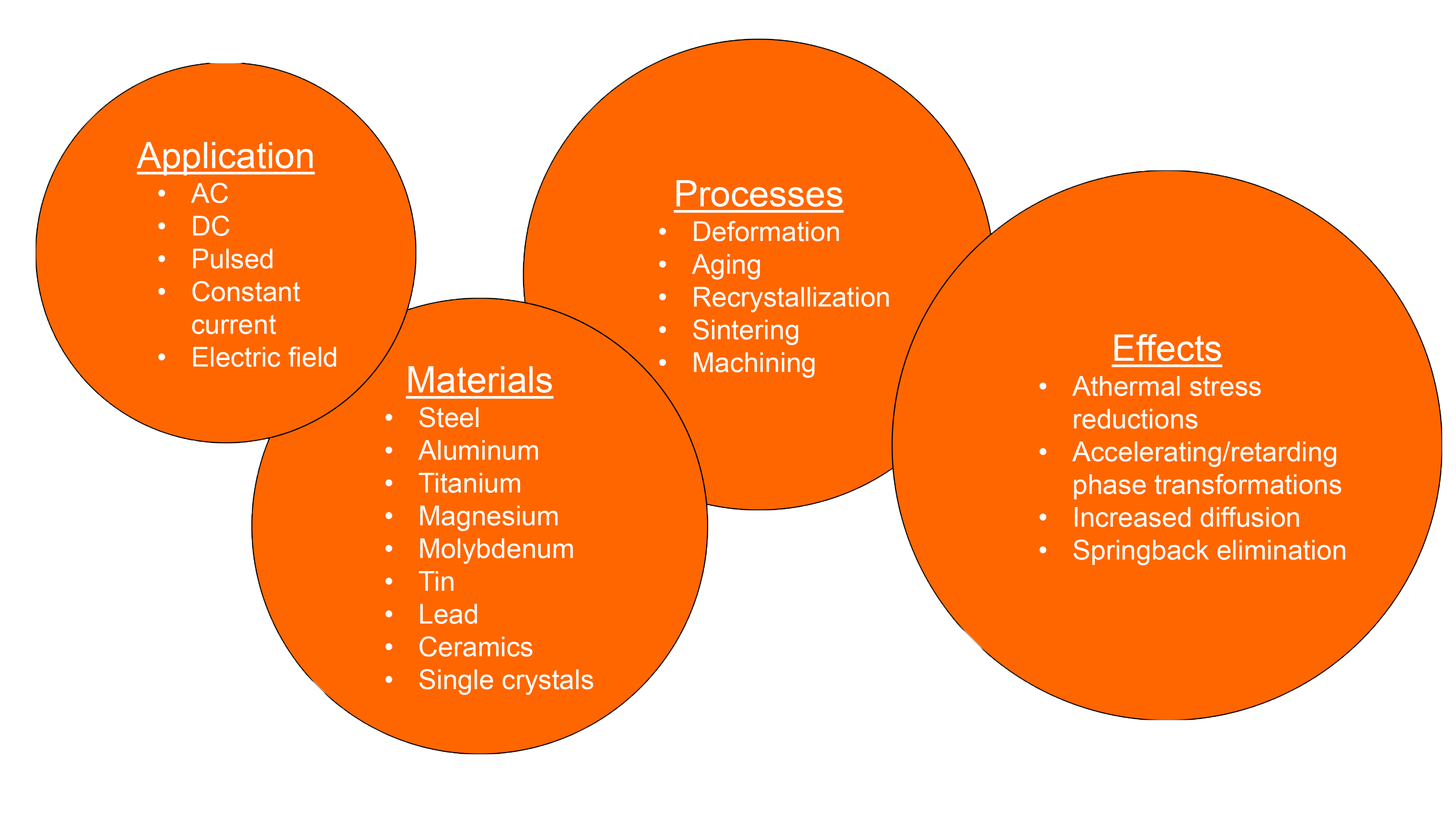
Effects of Power Supply
It is essential in research to consider all variables while testing. An overlooked variable in electrically assisted manufacturing is the output of the power supply. See in this image how a “DC” power supply can sometimes have fluctuations in the output signal.
This power supply can output up to 4,000 amps, a substantial load. Generally used within the electroplating industry, its practical use is not effected by this poor signal. However, it should be considered when used in research.
Even research grade power supplies, like this one shown here, can have this effect.
Another consideration with power supplies is that there is usually a delay between when the power supply is turned on and when the current begins to flow. In research, not accounting for this delay can throw off calculations, resulting in erroneous results.
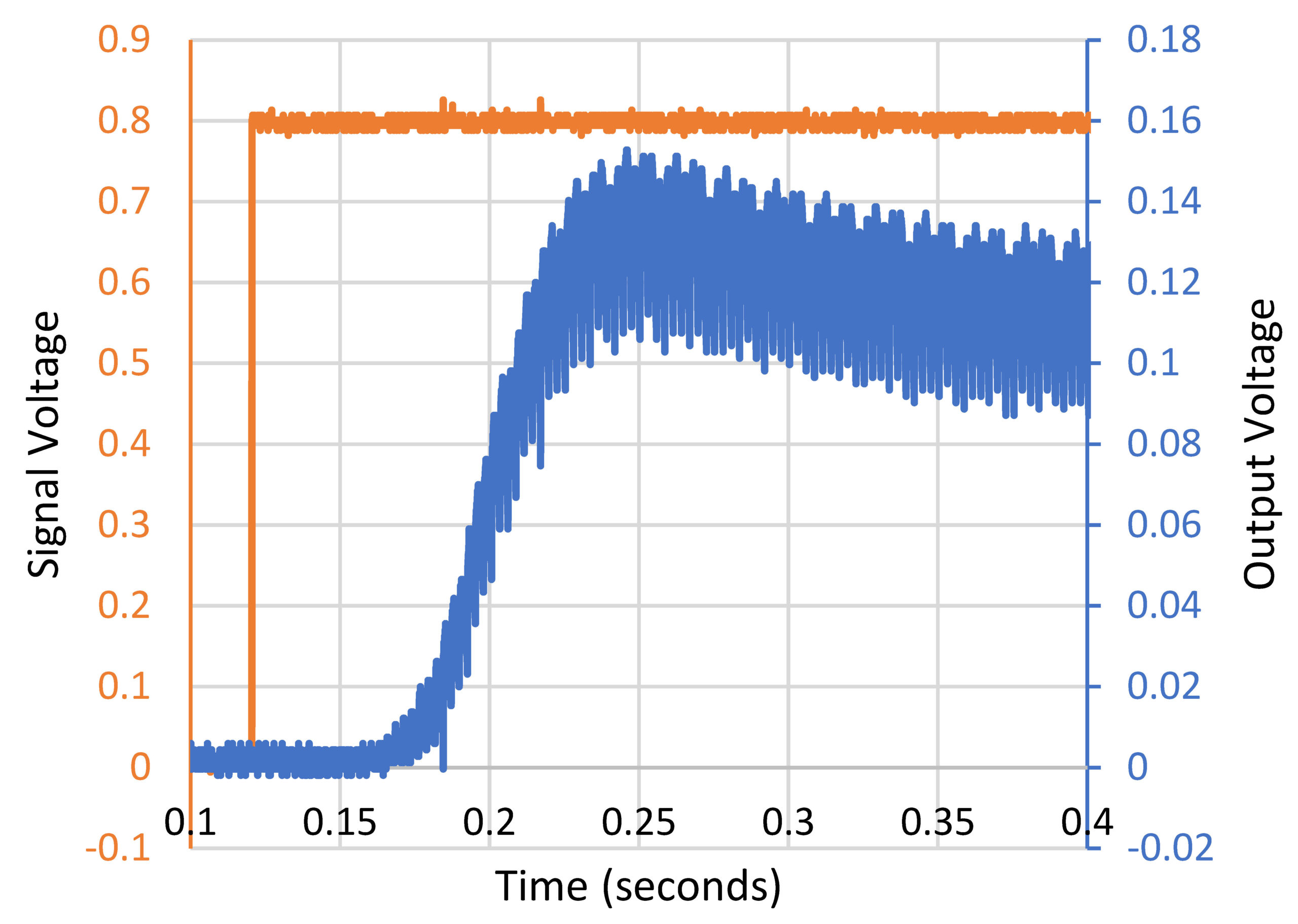
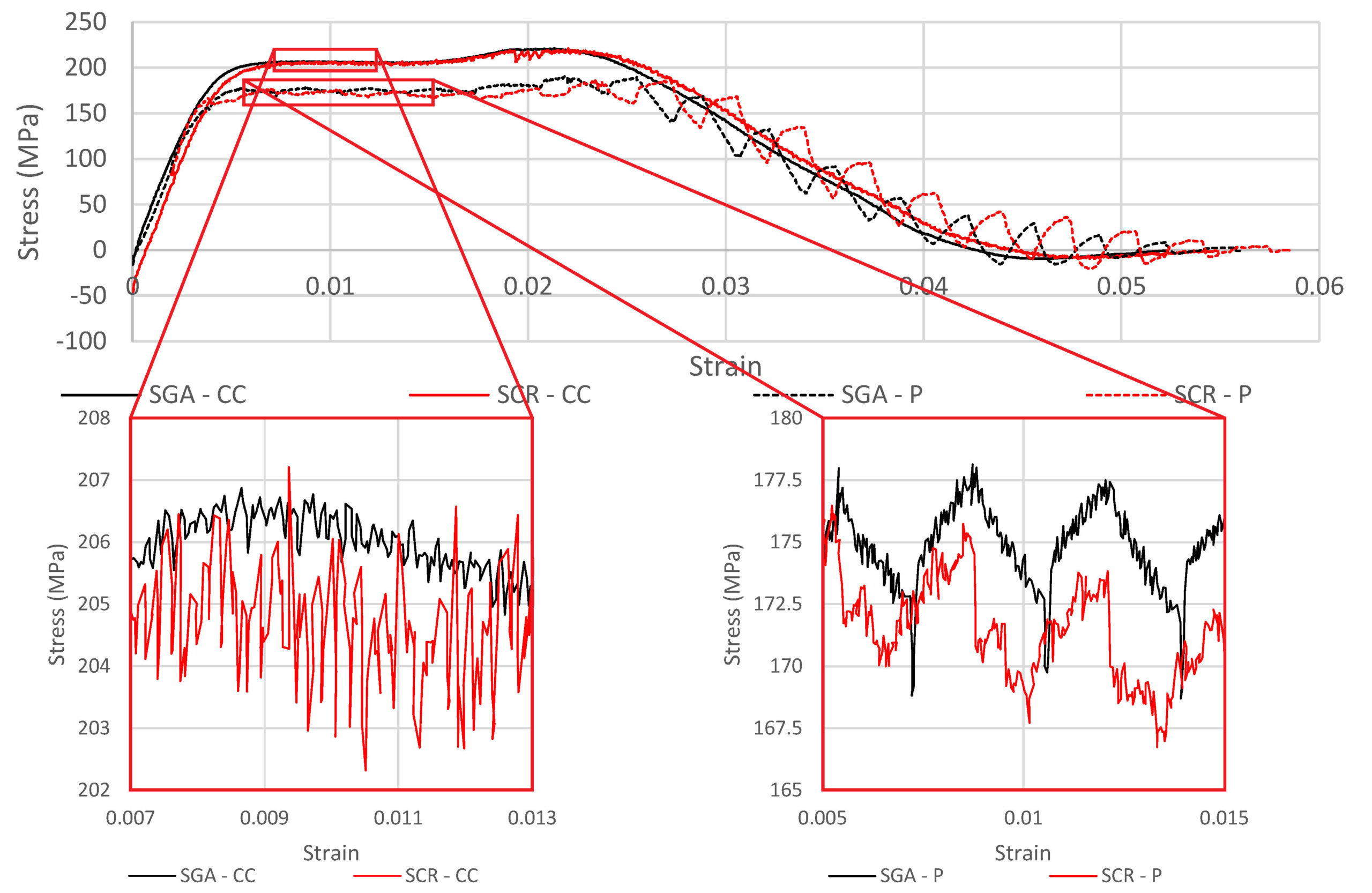
We’ve found that these signals can actually affect our testing. Here are the results of tensile tests that used a constant current amplitude and one that pulsed the current throughout the test. Note in this image the differences between the red and black lines, which represent two different power supplies.
More information on this work can be found here.
One of the very few ways to produce a clean DC output is to use batteries. In order to have full control of the specifications of our battery, we designed and built our own! Find more information related to our battery bank here.
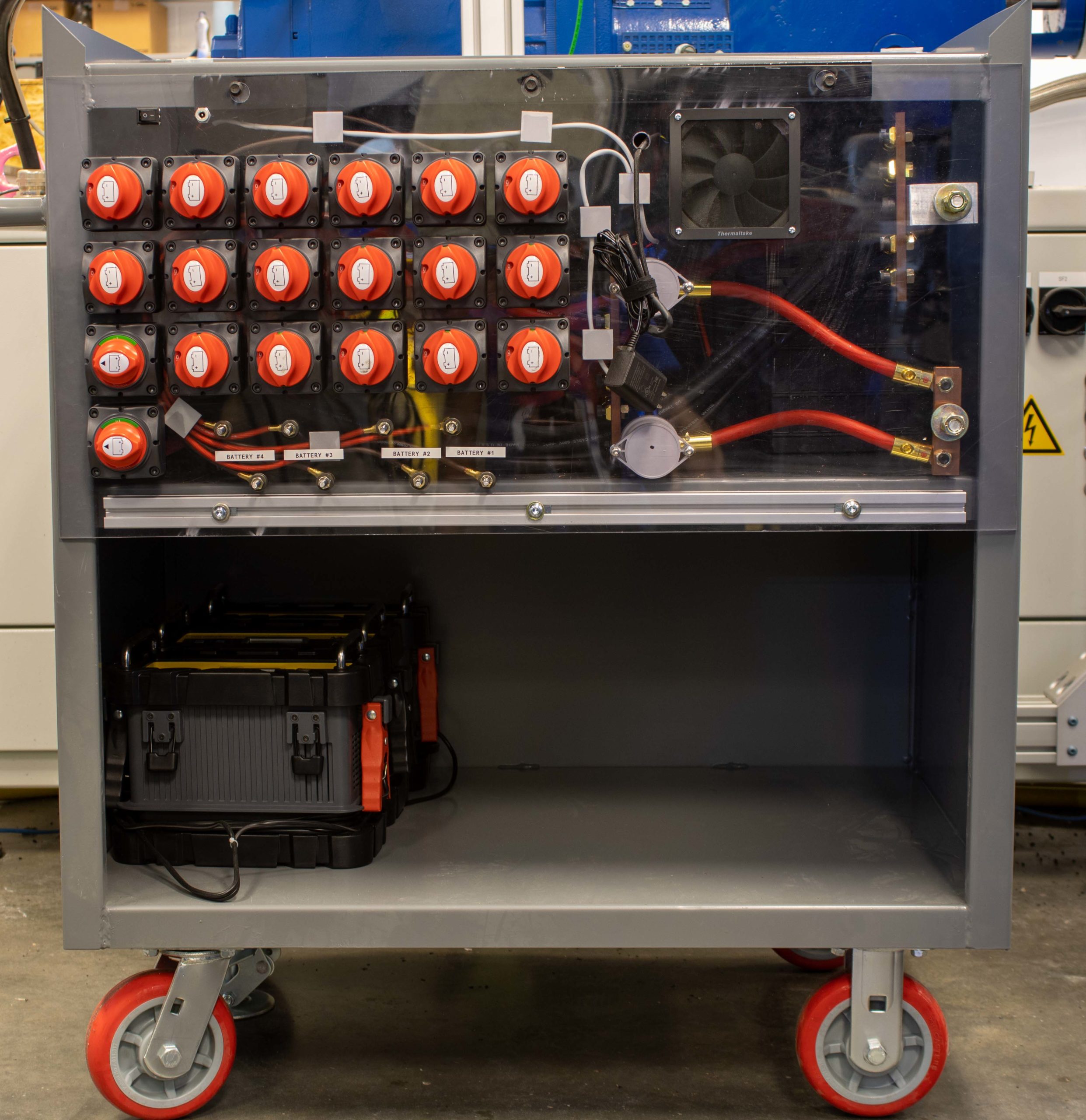
Another method we’ve explored for making clean, DC currents is through a homopolar generator. See more about this device here.
Electrically Assisted Manufacturing Controls
The use of electrically assisted manufacturing enables very rapid heating, offering another level of control during processes. For example, as metal becomes hotter, it becomes easier to deform. We can take advantage of this fact and adjust the strength of materials in real-time during processing.
In this research, we have implemented a feedback control loop which enables the user to define the force at which they want their material to deform. Use the slider to see the difference between a normal test and one that we have used our control method on.
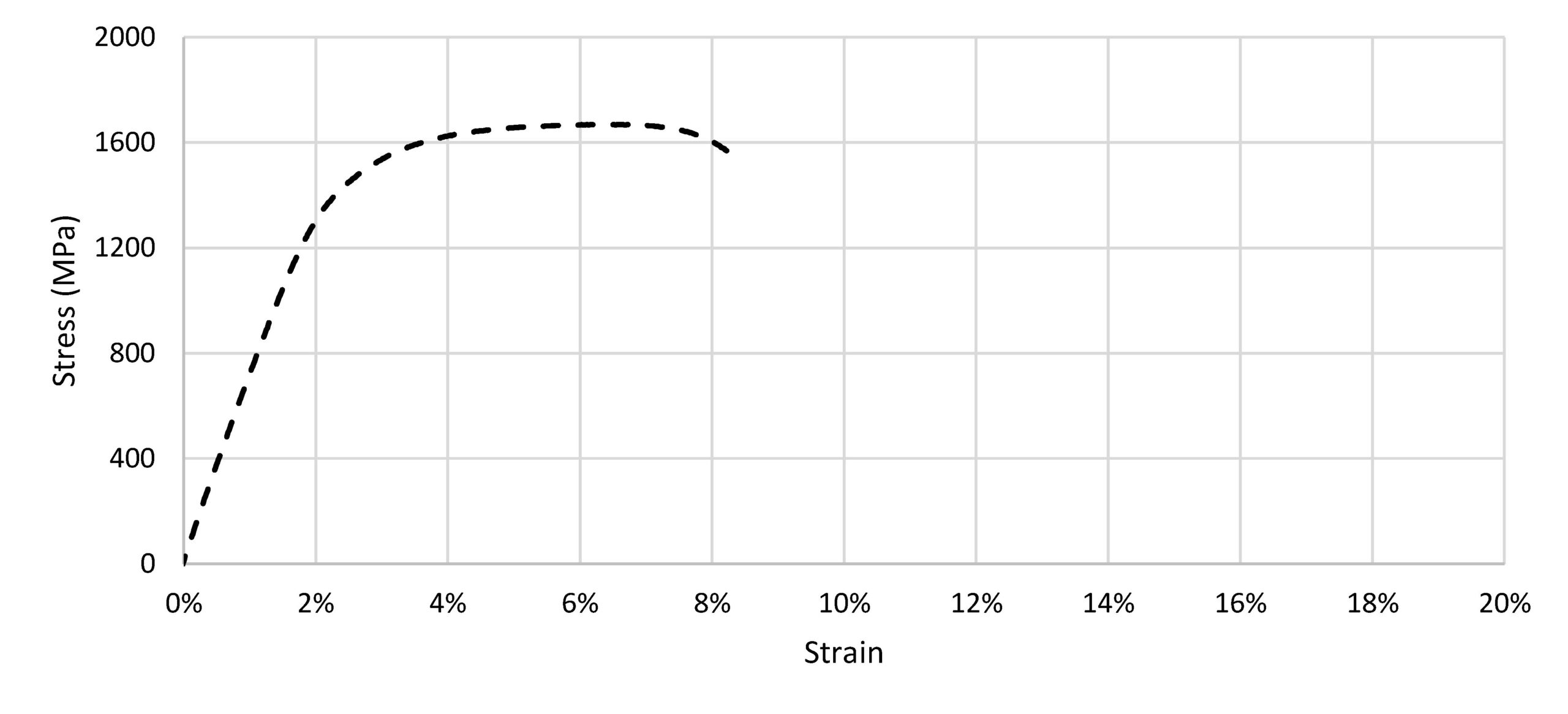
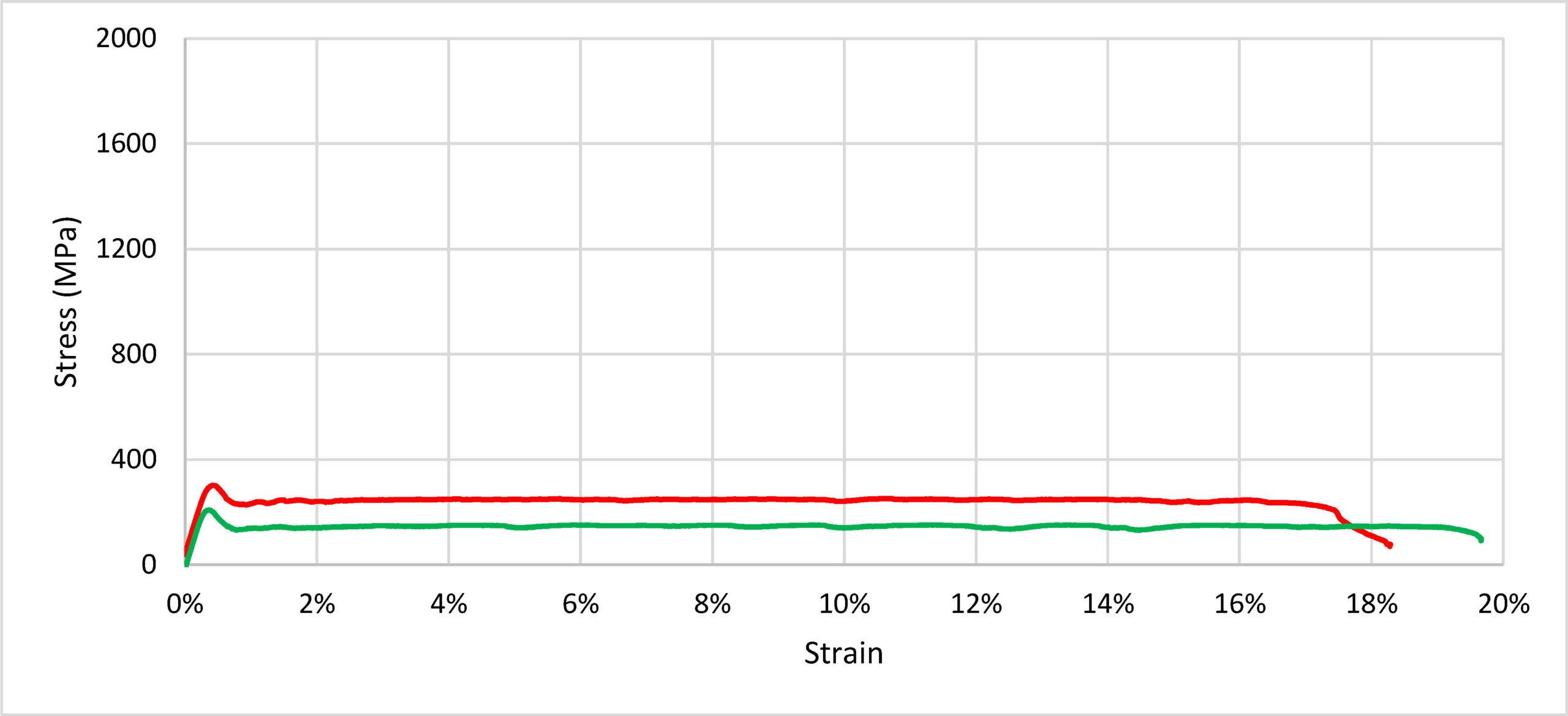
Another control method we’ve explored in electrically assisted manufacturing is to send pulses of electricity once a certain force is reached in a tensile test. This method may be better suited when the operator doesn’t have complete control over the power supply output or would like to use capacitors to output high-energy pulses.
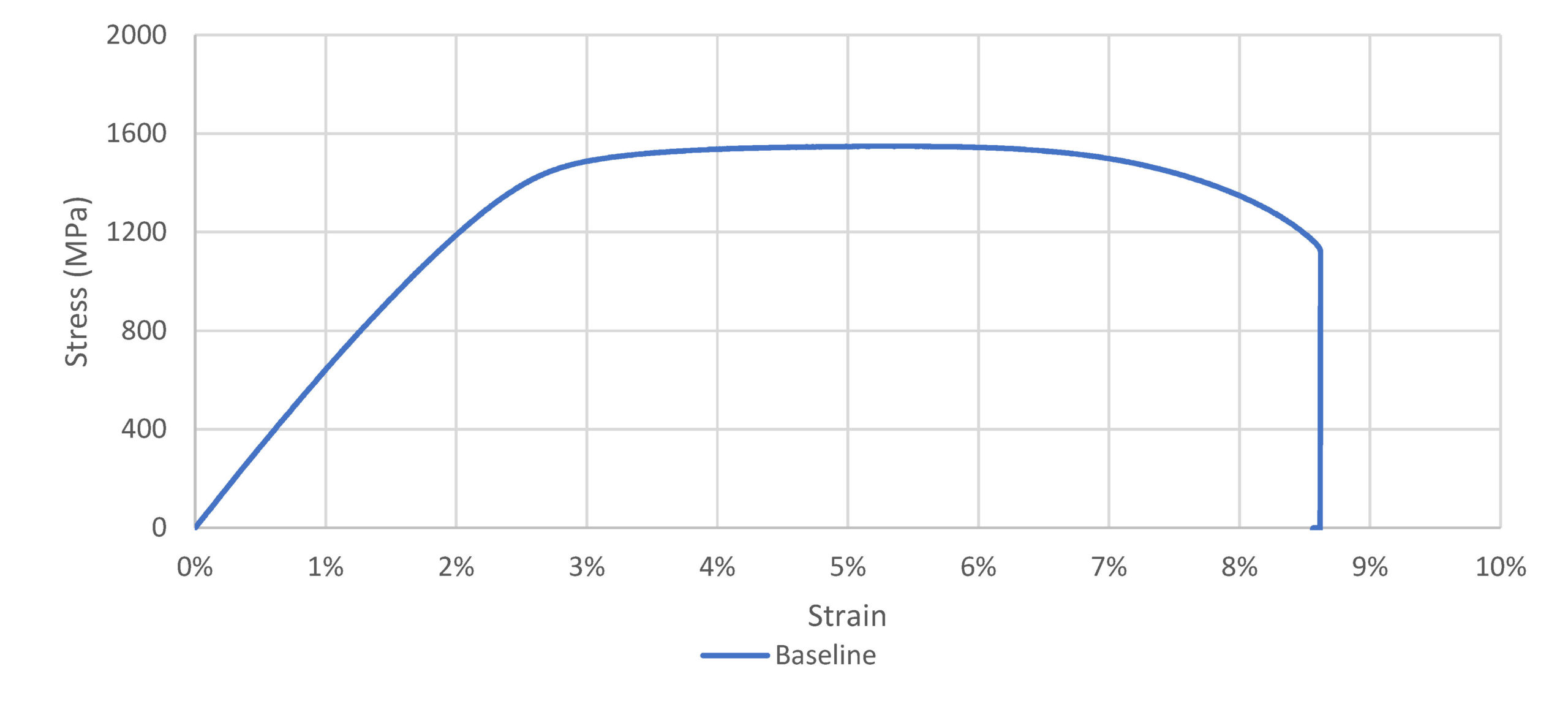
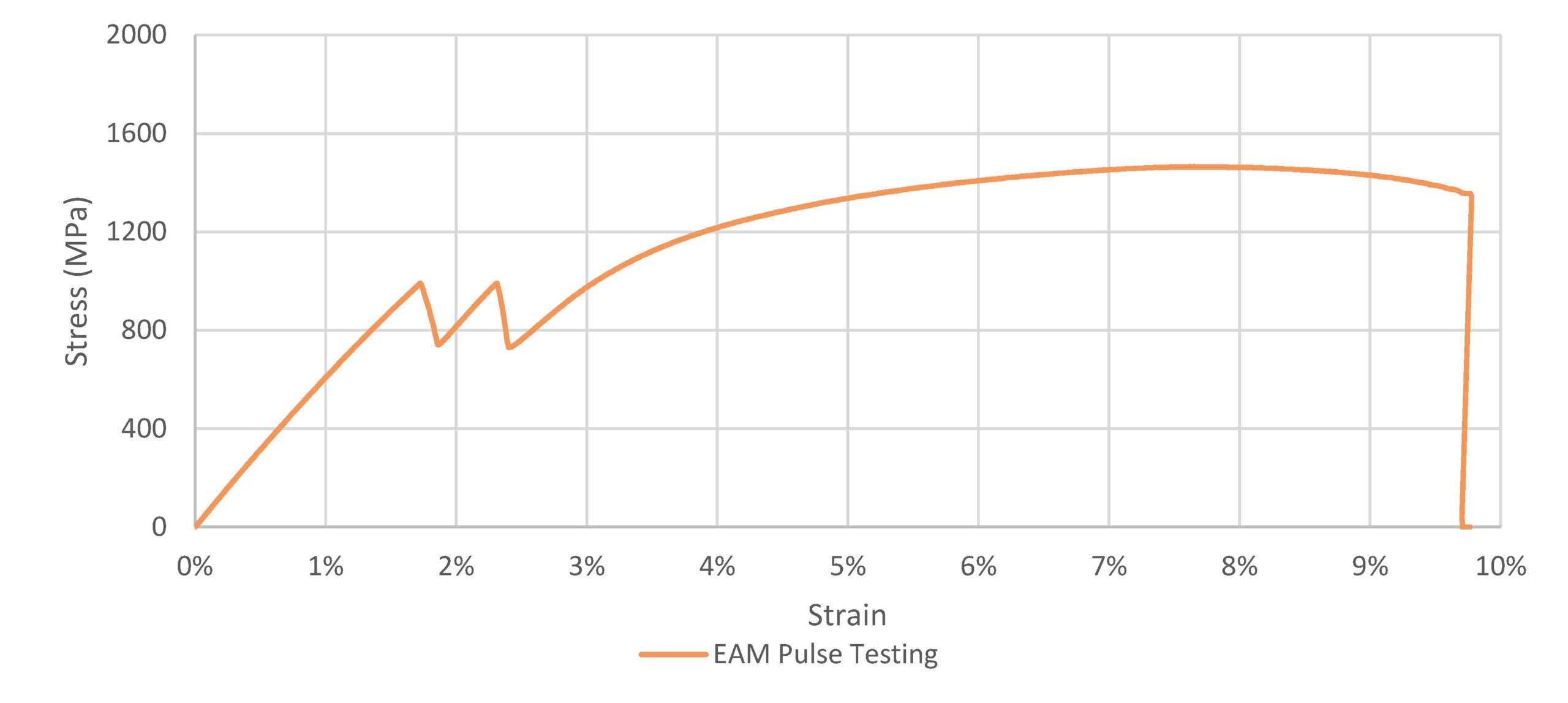
Conflicting Results – Electrically Assisted Wire Drawing
Electrically assisted manufacturing literature is riddled with conflicting results. One example of this is found in electrically assisted wire drawing. The results of applying an electric current during wire drawing is a significant reduction in drawing force. What was observed experimentally was that changes in polarity also change drawing force reductions. This should not occur according to our current understanding of electroplasticity. Therefore, either our theories are wrong, or we are making false conclusions about this testing.
As our first step in investigating this work, we performed several analyses of the available literature to determine if something was previously missed. We determined that none of the existing theories can be directly applied to explain these results. For example, this figure shows the trend line which should be produced when joule heating is considered. Since these lines are not similar, there must be something else that is occurring.
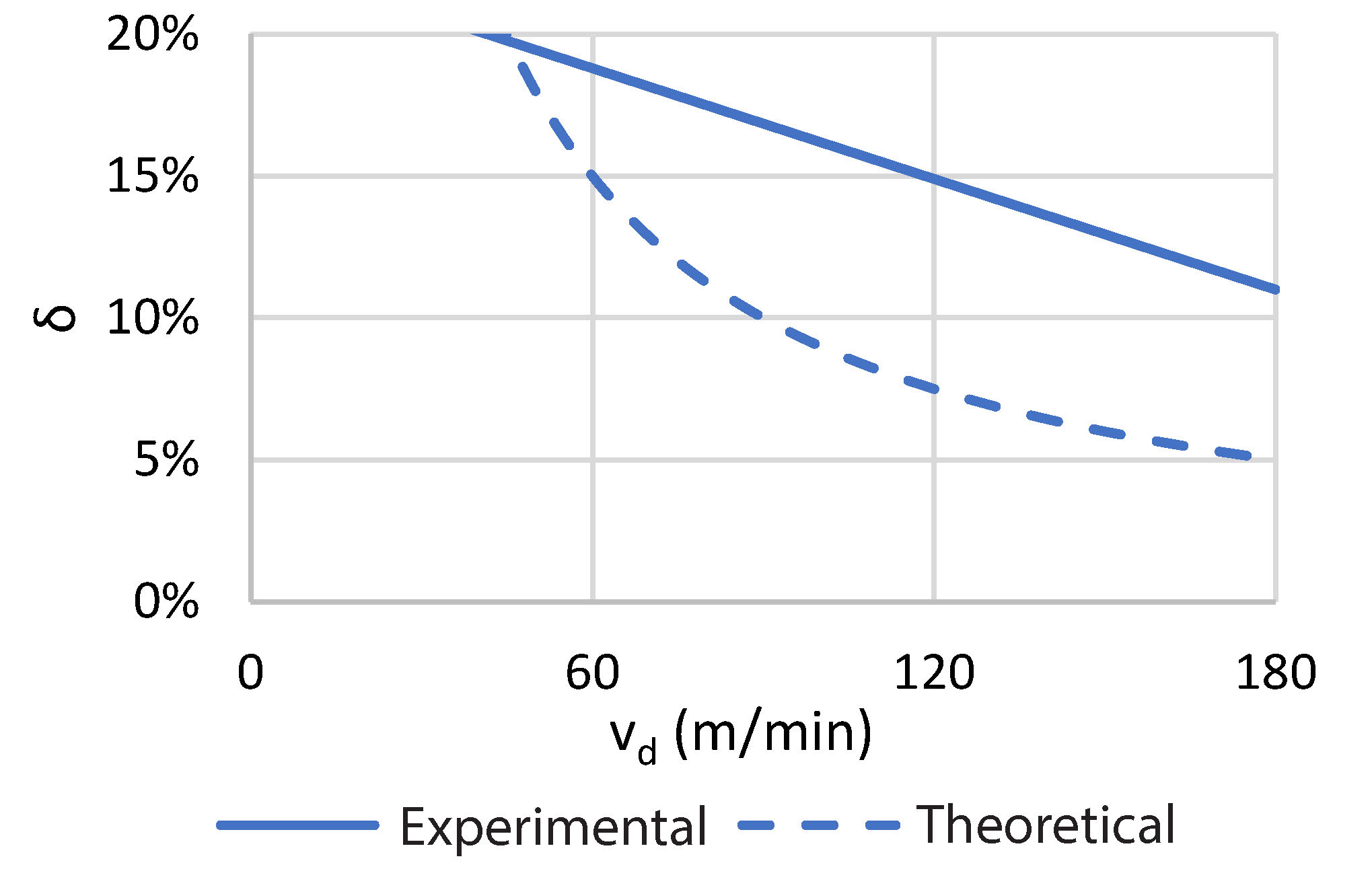
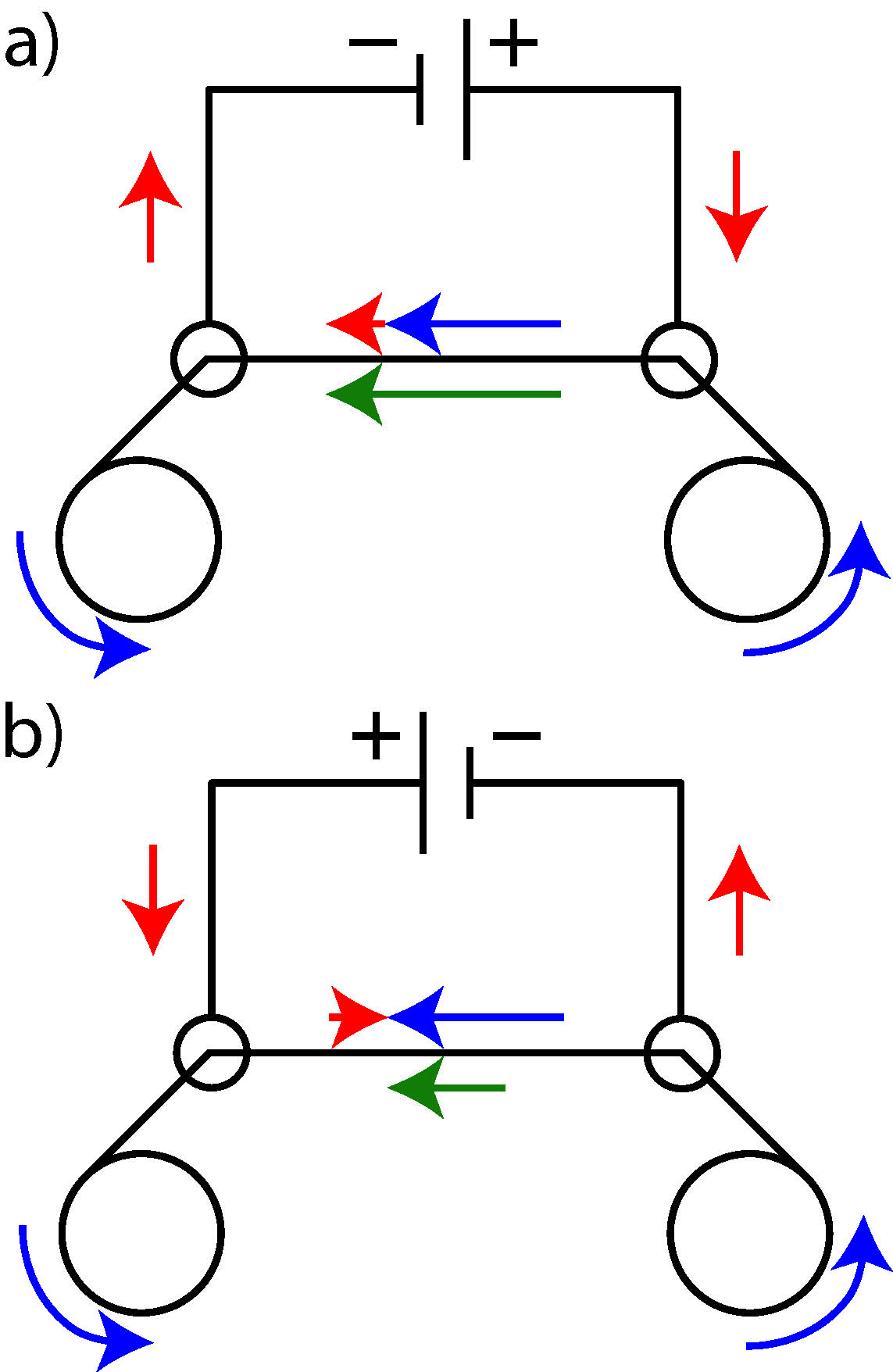
Electrically assisted wire drawing presents a very unique circuit; a wire moving between two stationary electrodes. Therefore, there could be something more fundamental that is being overlooked, since we don’t know much about this process. We decided to investigate what is happening with the electric current magnitude between the electrodes. We thought it could be possible to interpret the electric current like a boat traveling in a river. A fast boat moving upstream will appear slow from the shore. Conversely, a slow boat moving downstream will appear fast. Could something similar be happening in our wire?
Since we’re not sure if anyone has explored this concept before, we tested it ourselves experimentally. We created a fixture which moves a wire between two electrodes and measured the electric current through the wire. To construct this fixture, two fishing reels were used and a servo motor was used to precisely control the drawing velocity.
From this testing, we found that our theory is incorrect; the current passing through the wire remained the same, regardless of its motion.
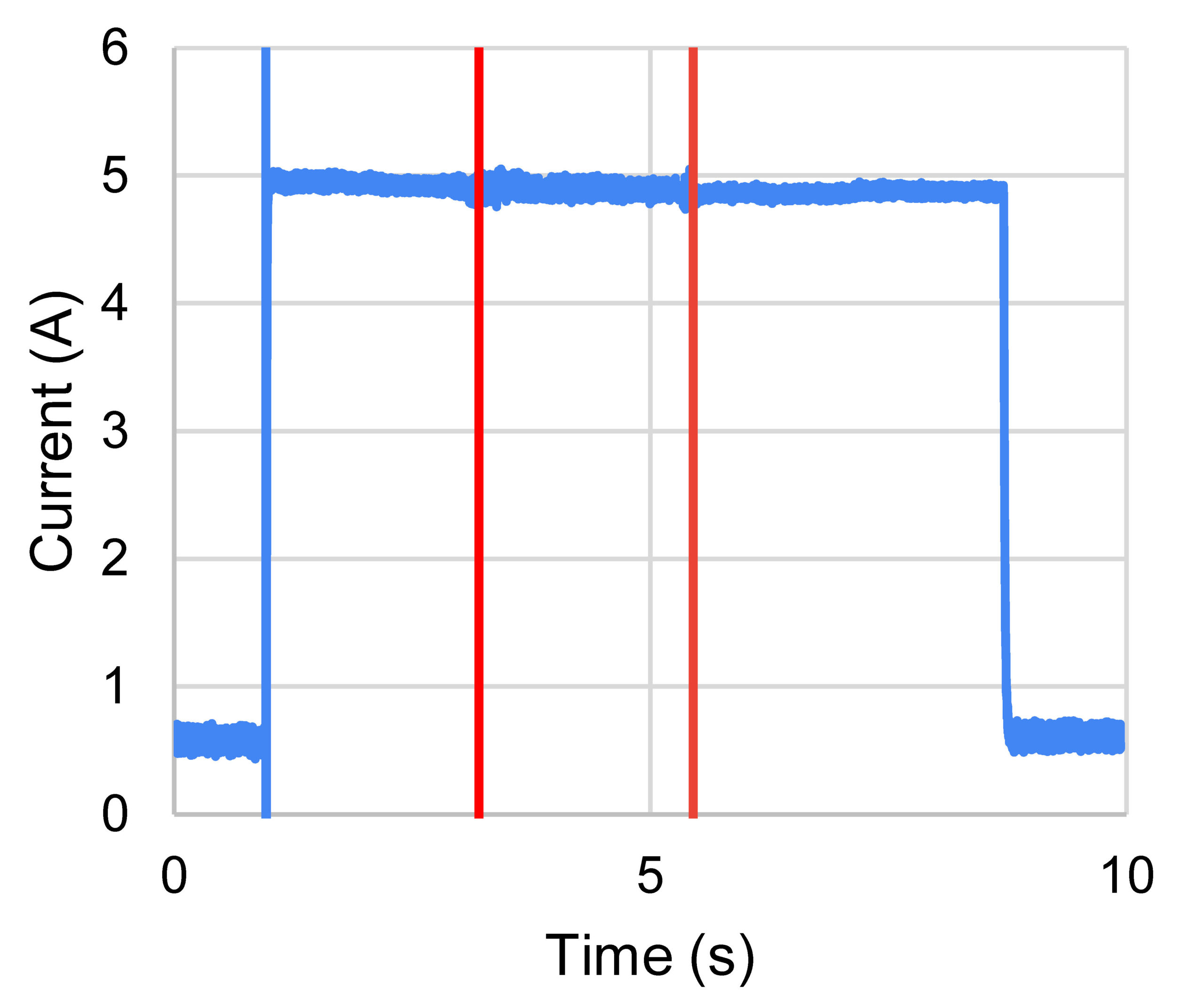
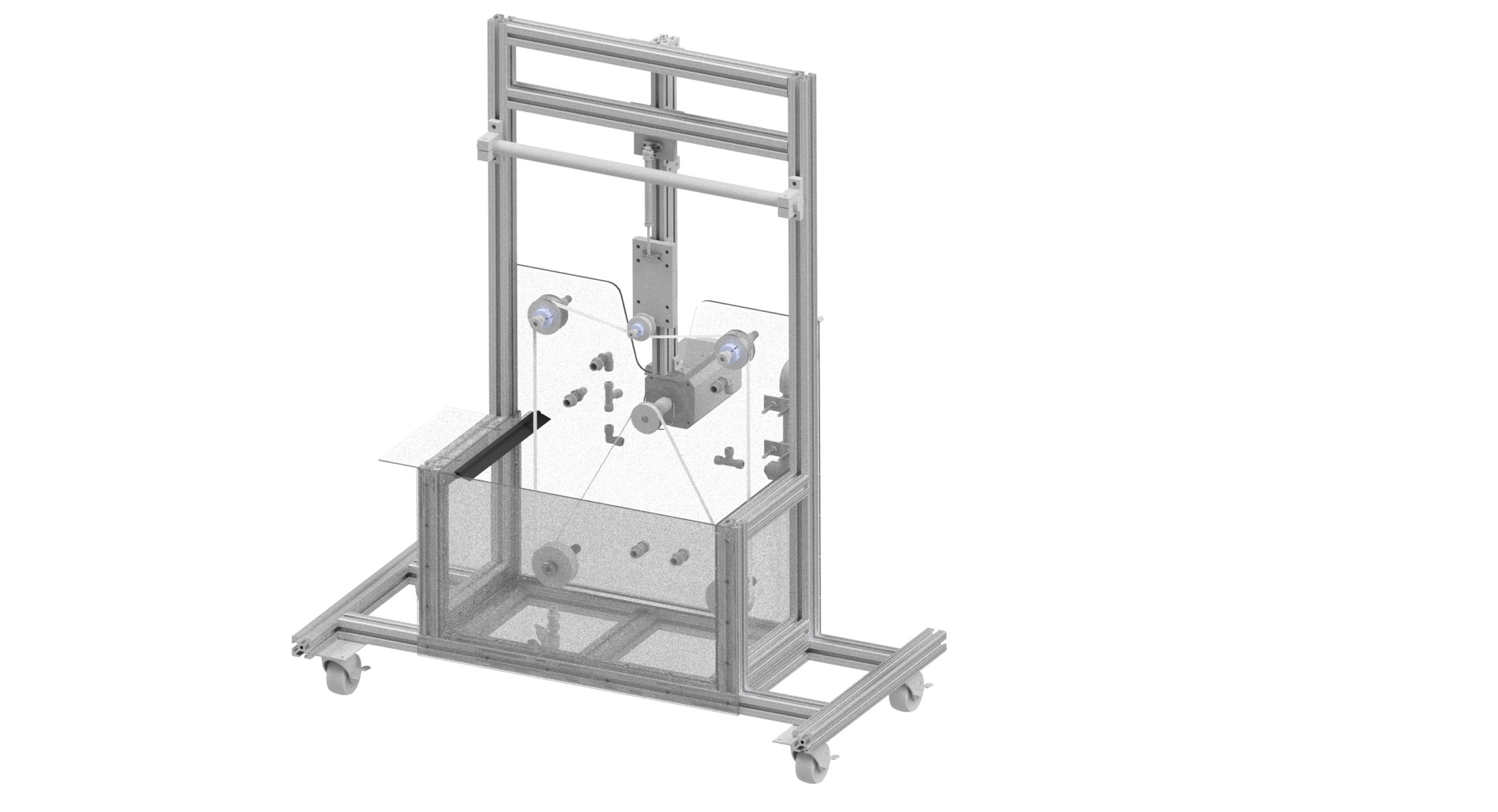
For our future work, we plan to further investigate thermal effects using a fixture that replaces the wire with a band. The use of a band should enable easier thermal measurements.