Friction Element Welding (FEW)
EJOWELD Friction Element Welding (FEW) is a thermo-mechanical process capable of joining high-strength aluminum alloys to advanced high-strength steels/ultra-high-strength steels by the use of a friction element. FEW poses significant advantages over conventional joining techniques employed in the automotive industry.
- No need for pre-drilled holes and surface preparation.
- One of the few processes that can join AHSS.
- Very little processing time.
- The process is free of harmful expulsions (such as sparks in Resistance Spot Welding (RSW) ) and noise.
- No limit on the thickness and strength of the steel sheet.
It has four processing steps,
- Penetration – friction element penetrates the top sheet
- Cleaning – any coating on the cover sheet is removed
- Welding – friction element welds onto the cover sheet
- Compression – the element is compressed to close any gaps
Despite being an extremely robust process, it has two disadvantages. One, it is a two-sided process. It needs access from both sides to form a weld. This is not possible in a production environment where there might be limited access to the other side. Second, is the issue of chipping. Chipping is the formation of small hair-like whiskers that protrude from the weld pool. In an ideal process, it is desired to have all the chips enclosed underneath the head of the fastener. But, these small hair-like structures extrude away from the weld pool. This causes accelerated crevice corrosion and diminishes the aesthetic appeal of the joint.
You can learn more about chipping in friction element welding here.
Chipping Reduction in FEW
Chipping accelerates corrosion and is an undesirable characteristic for a good weld. It has been found to be caused by the eccentric motion of the element as it progresses during the processes. This eccentric motion is the result of a loose tolerance between the bit and the element which has been intentionally kept to avoid the element adhering to the bit. So, research has been carried out by the group to eliminate this chipping behavior without modifications to the equipment itself. It has been found that chipping is influenced only by the penetration step.
Thermal Assistance
Chipping is seen predominantly in the higher strength alloys of aluminum than the softer ones. Augmentation by thermal assistance temporarily reduces the strength of the aluminum and improves ductility. At increased ductility, the material flows easily around the shaft, and chipping is reduced. As the temperature of the aluminum prior to the joining process increased, the chipping also reduced. Learn more about chipping reduction through thermal augmentation here.
Conduction Heating
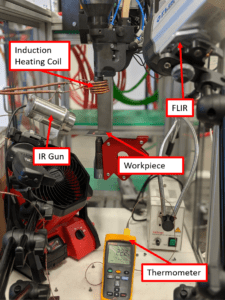
This iteration of thermally assisted FEW involves heating the workpiece through the method of conduction. This involves the design and fabrication of a modified downholder for the Ejoweld equipment made of tool steel which will be heated using an induction heater. The downholder will then come and conduct heat to the workpiece. This is a simple plug-and-play installation and could be easily employed in the industry.
Laser Heating
The conduction FEW had the disadvantage of increased process time. The time to heat the downholder, the time of contact with the aluminum workpiece, and the actual process all added to about a total process time of 1 minute. To overcome this disadvantage, a rapid more localized method of heating was selected. Laser has the advantage of heating the workpiece locally at the contact of the friction element. The CO2 laser employed heated the aluminum workpiece locally at the desired spot in under 10 seconds. This time will be further reduced by using a higher power laser heater.

Resistive Heating

The heating method explored herein was resistive heating achieved through electrical current. A clear distinction must be made between the present method and a concept known as electrically assisted manufacturing (EAM). EAM is typically performed by passing an electric current through the workpiece during processing. This method differs in that the electric current is turned off before the process is performed. EAM has also been used to describe processes in which materials were altered prior to processing using electric currents. This has mainly been achieved through high current pulses.
Key Contributors: