Tyler Grimm
Automotive Engineering PhD Student
Graduate Research Assistant
Phone: (724)-480-9773
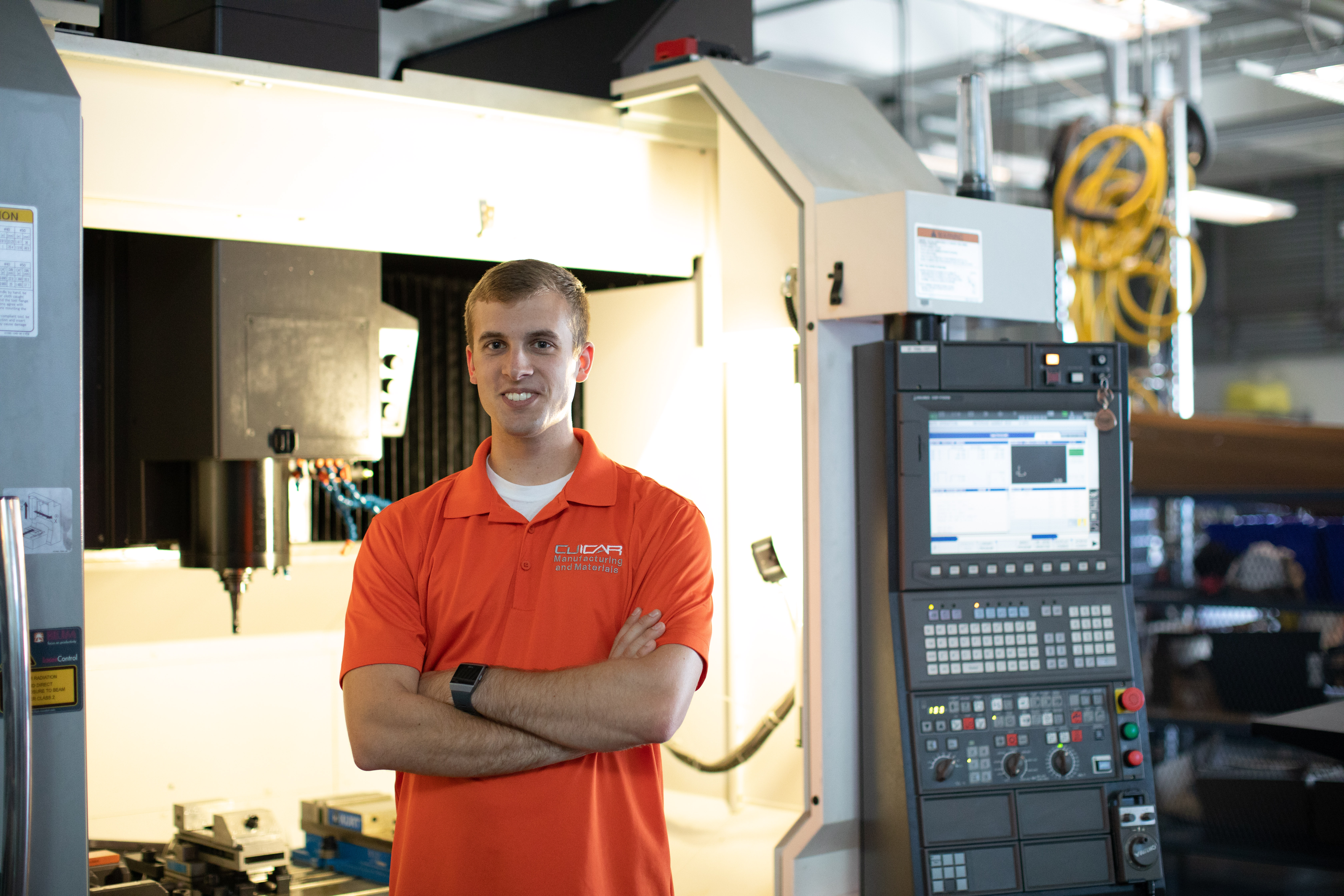
Bio
My interest in automotive manufacturing started at an early age. Working on cars with my dad allowed me to dissect the many systems within them and learn how they worked. In pursuing this interest, I attended college at Penn State Behrend for a bachelor’s degree in mechanical engineering. I quickly joined a manufacturing research group led by Dr. John Roth, an expert in this field. Over the next few years, my interest turned into a passion, and I was able to experience the remarkable influence academic research can have on industry. The research I am now conducting at Clemson University aims to improve advanced manufacturing processes for rapid implementation into domestic industries.
Featured Research
Incremental Forming
Incremental forming is an advanced manufacturing process capable of rapid prototyping of sheet metal shapes. These logos of the major automotive OEM’s were each formed in less than 20 minutes, without any dedicated dies. Whether it’s a desk ornament or an experimental panel on a concept car, incremental forming provides an excellent solution.
Machining
When machining freeform surfaces, geometric errors known as scallops are inevitably formed. Traditional toolpaths, which form these scallops in repetitive patterns, can easily produce a maximum scallop height. We’ve developed an algorithm to randomly generate toolpaths, while still maintaining a specified tolerance. With a unique surface finish, this process has an aesthetic appeal in addition to industrial advantages.
Joining
The use of high-speed videography has been essential in our work related to Friction Element Welding (FEW), a multi-material joining process used to secure aluminum sheets to steel.
Electrically Assisted Manufacturing
Electrically assisted manufacturing, which is the application of an electric current during a manufacturing process, causes several different phenomena. Studying these effects is exceptionally difficult to perform experimentally. My work focuses on decoupling the influence of DC power supplies’ current output with flow stress reductions commonly seen in deformation studies. Power supplies normally used in electrically assisted manufacturing research are assumed to output a perfect, DC current. However, this is not true. The image shown here is the signal output from a very high current power supply. As can be seen, the output is clearly not stable.
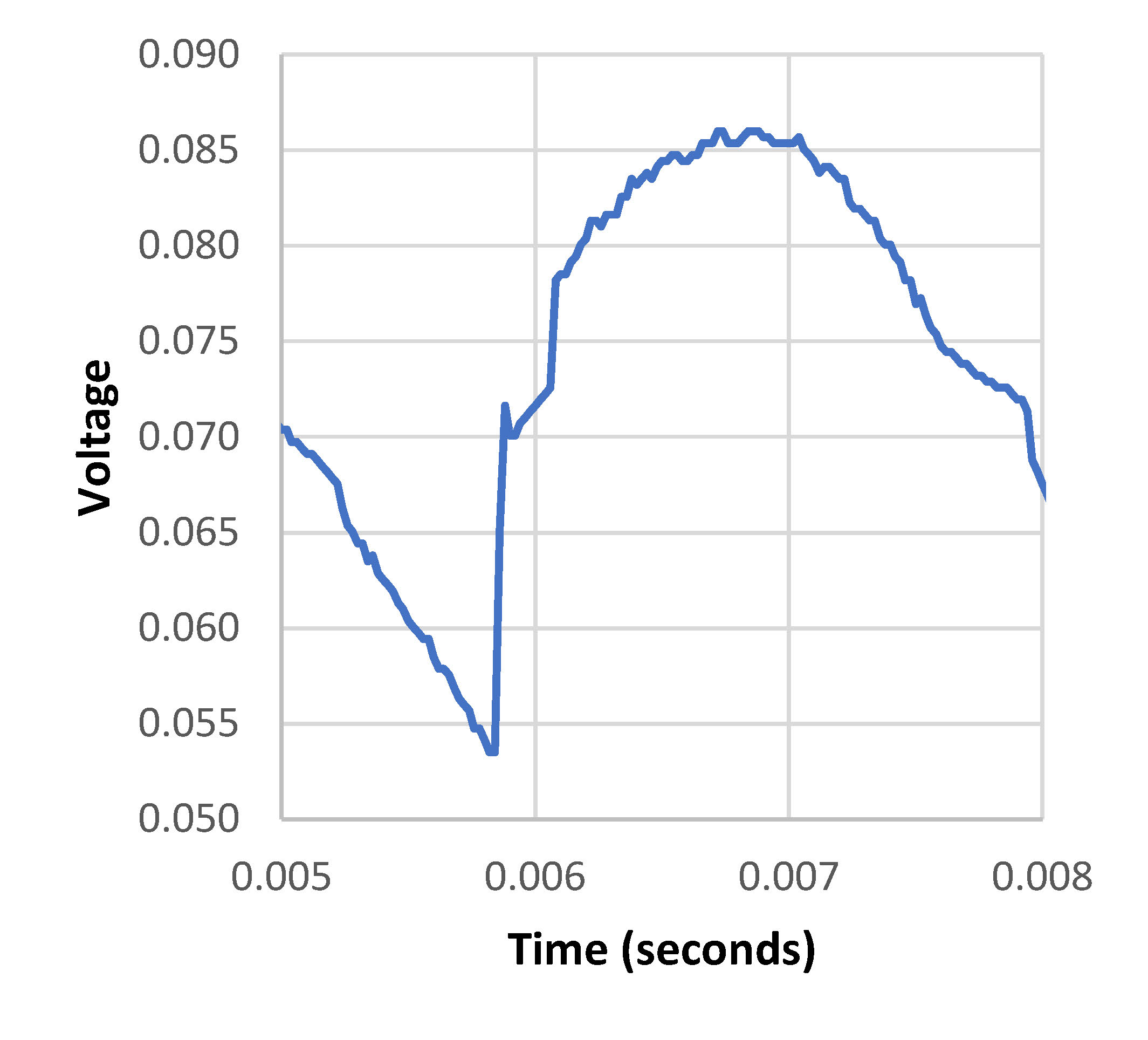
In Situ TEM
An electric current has been shown to change precipitates in aluminum alloys. The objective of this work is to observe precipitate evolution in situ with an electric current. This is performed by using a MEMS, electrically-biasing chip, which can be used to apply electric current to a TEM sample. A video summary of this work can be found Here.
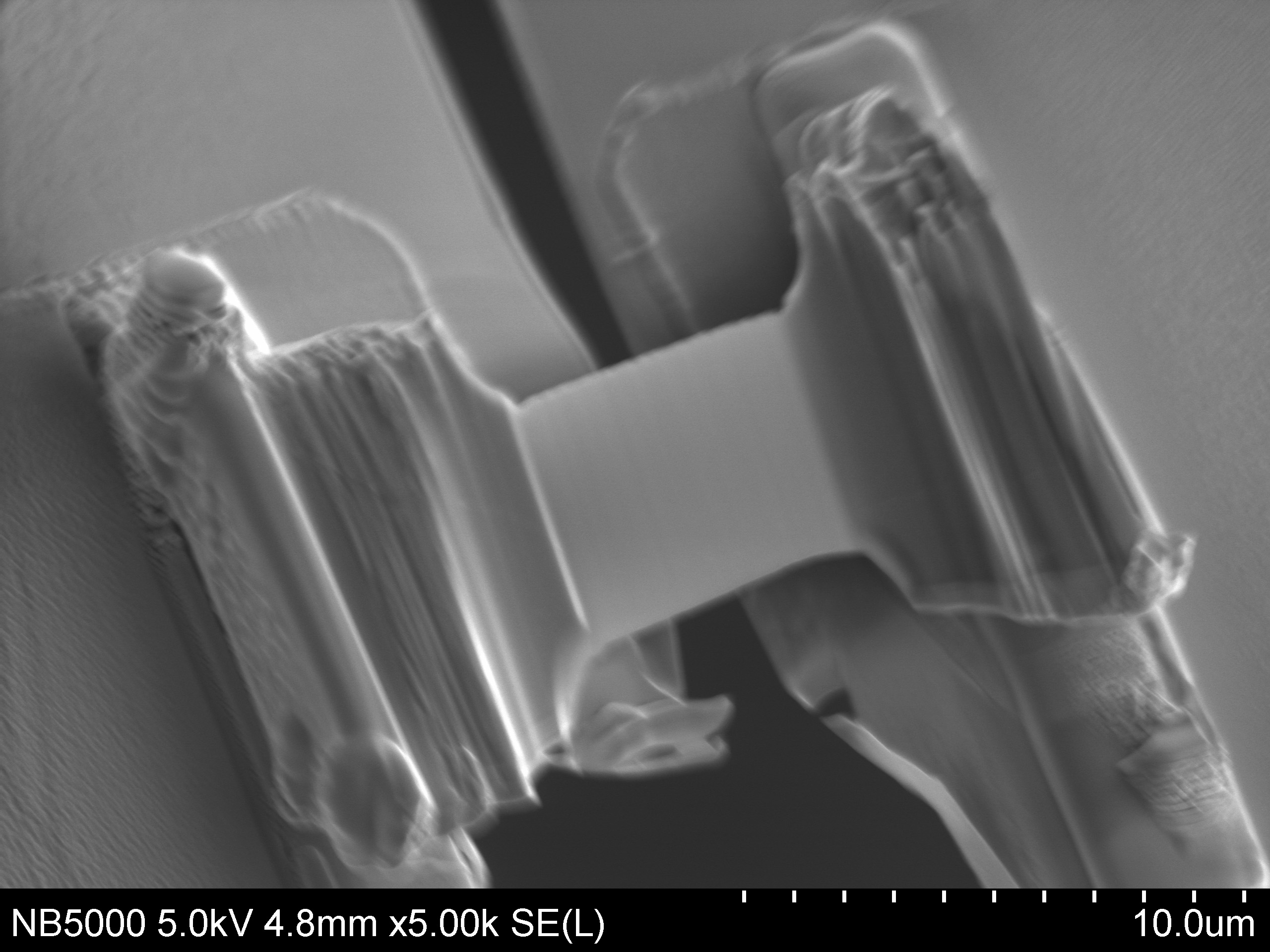
Open-Source Code
The voltage during a capacitor discharge can be described by the equation:
V(t)=c(e^(-at)-e^(-bt))
The variables a, b, and c must be determined such that a desired set of values (e.g. V_peak, t_peak, V_off, and t_Pulse Width) are produced by the equation. Since a general solution for this problem does not exist, a solution must be found programmatically.
[Click on title to access files]
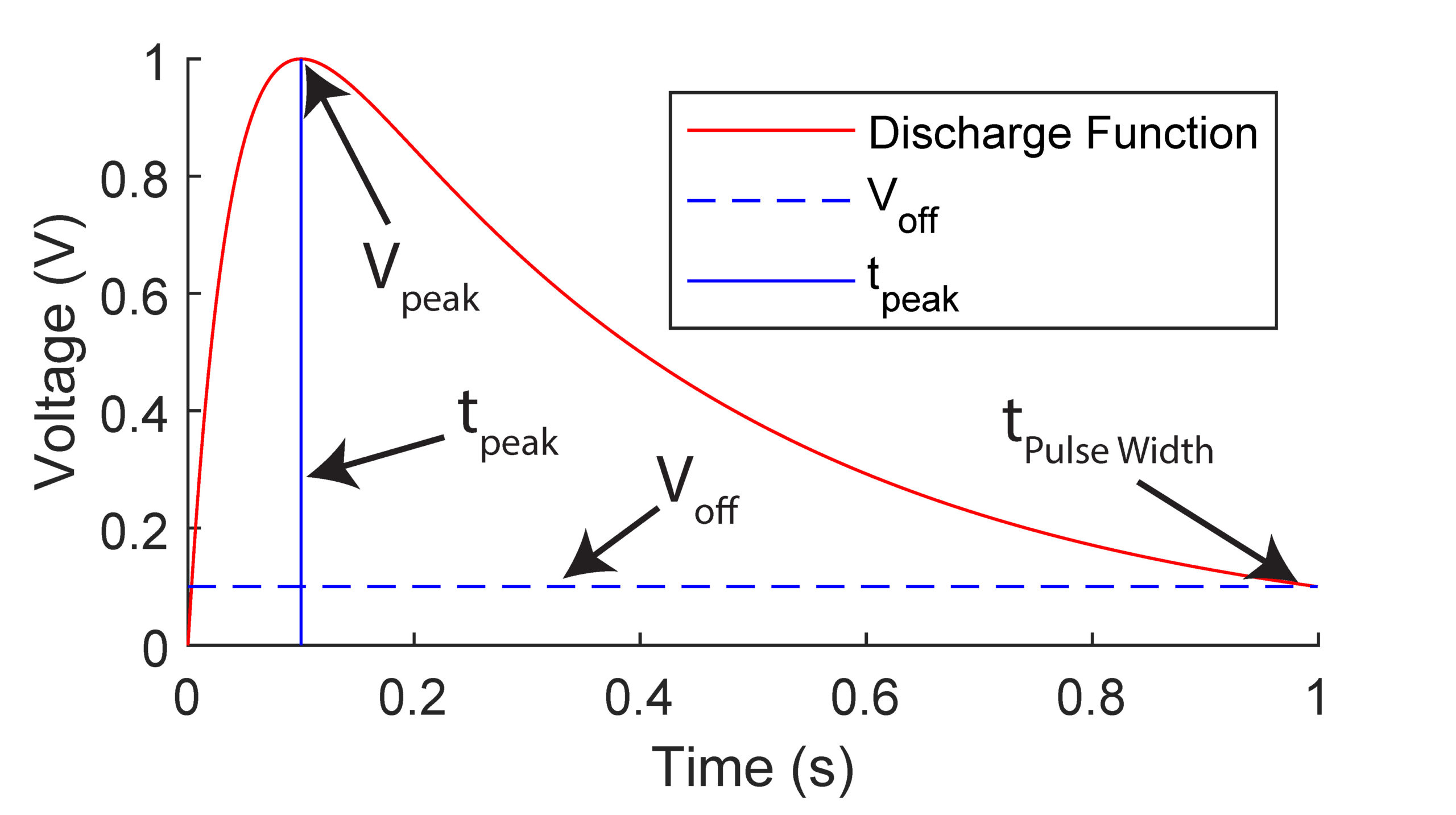
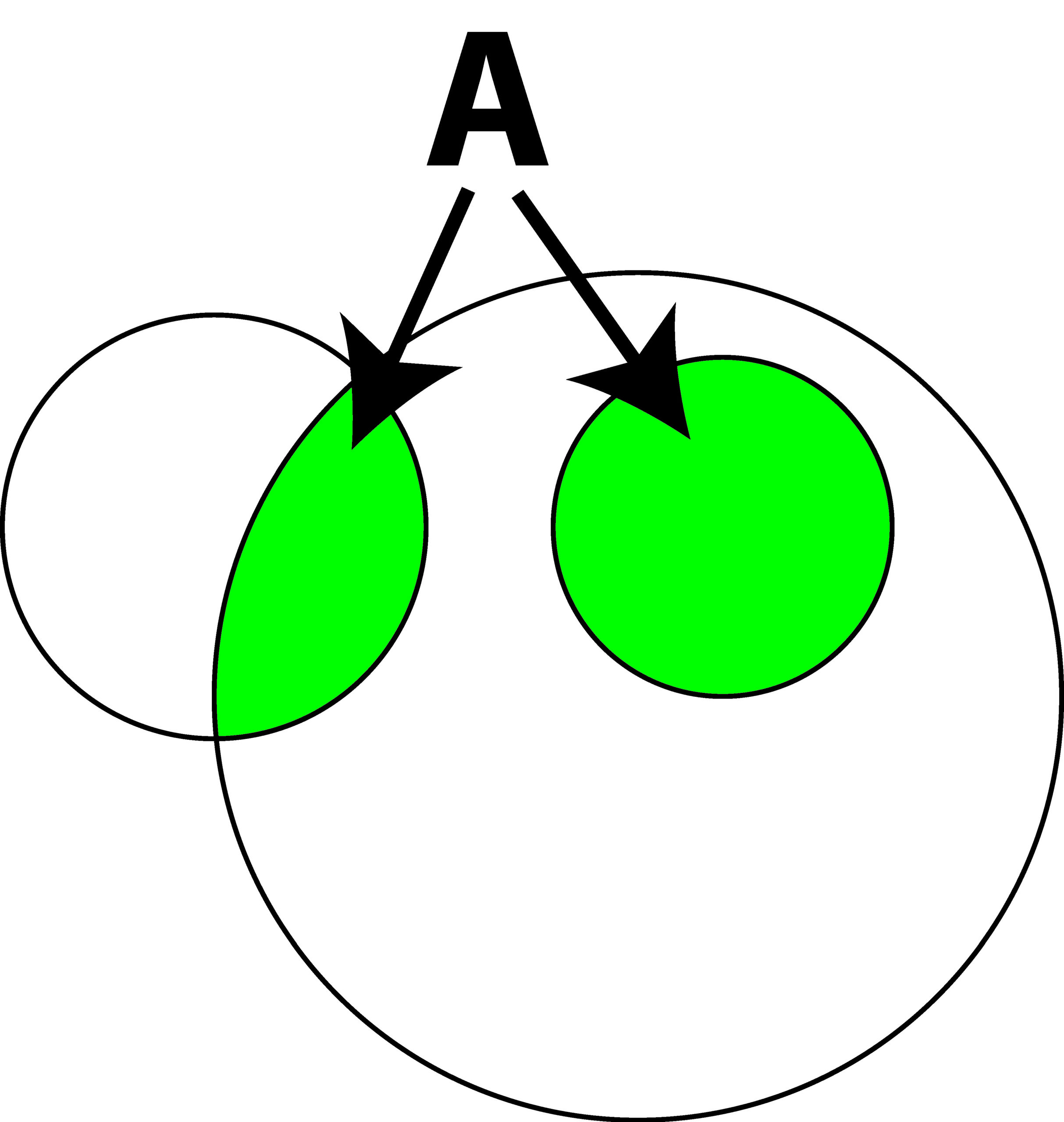
A MATLAB function for finding the area between two intersecting circles.
[Click on title to access files]
This program was built for experimental skin effect determination. A wire bundle was separated in one section such that individual wires can be probed for current. By probing many of these wires in concentric rings, the heterogeneous current density distribution could be determined. This code determines which wires should belong in each ring and what percentage of current through these wires should contribute to the ring.
[Click on title to access files]
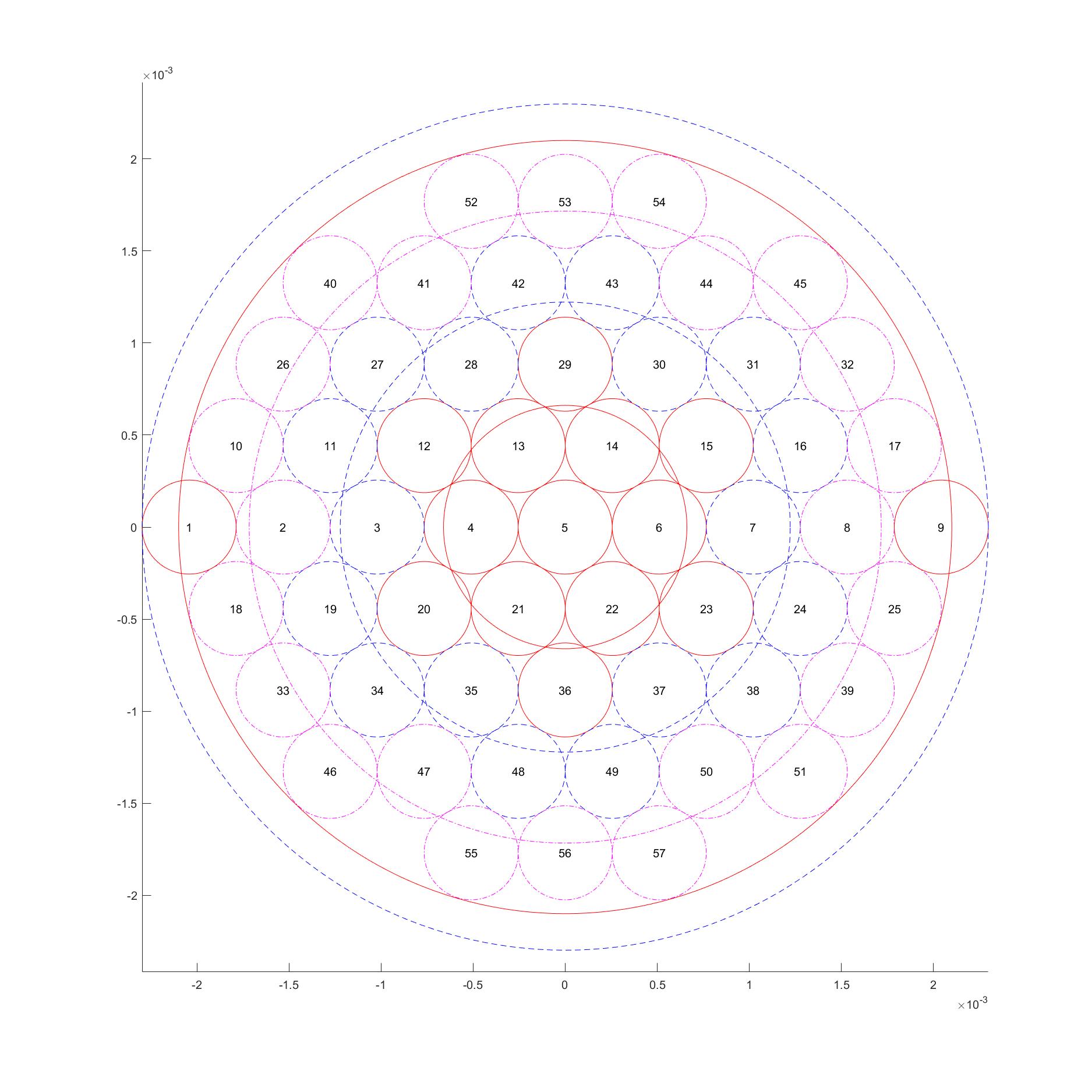
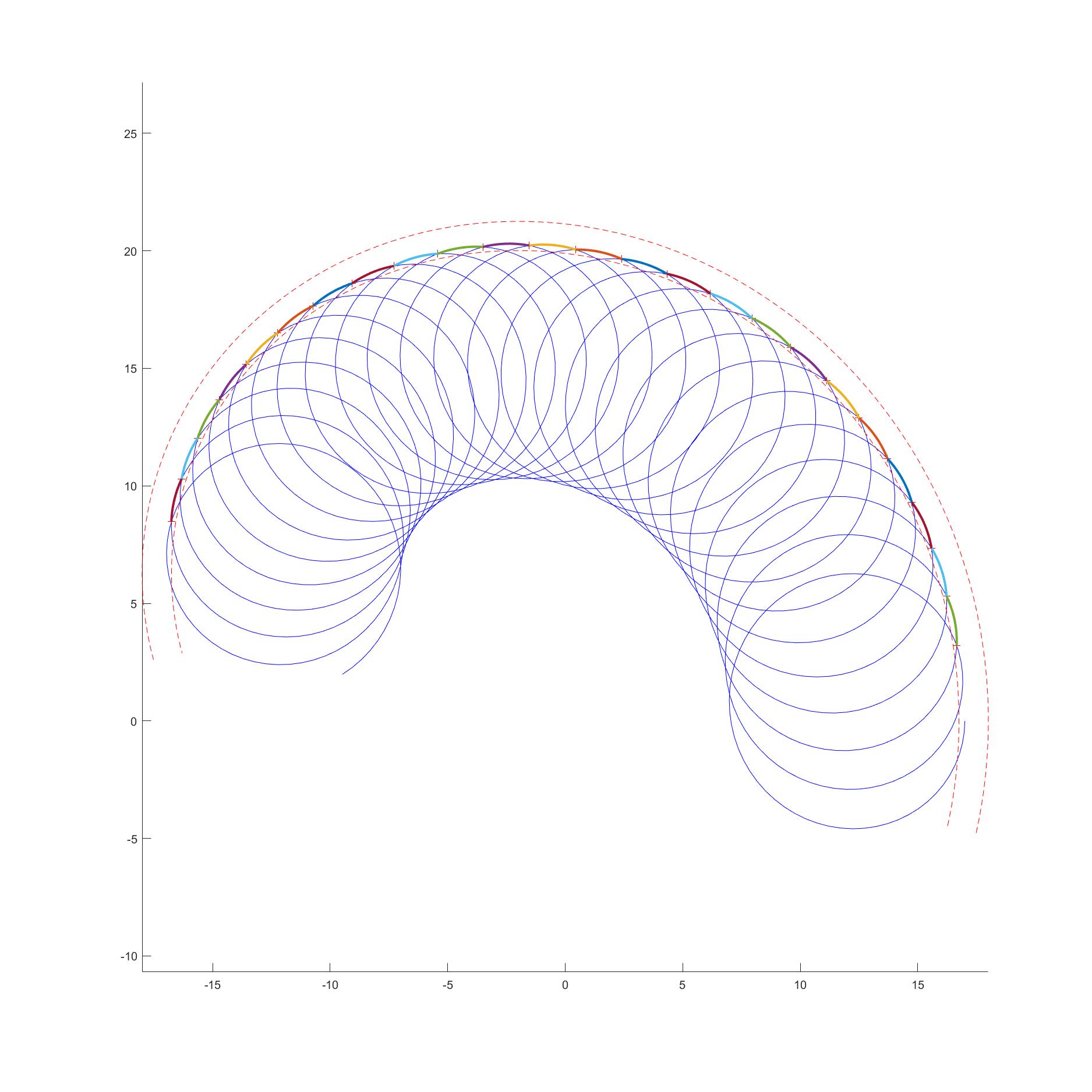
A MATLAB function for finding the outermost intersection points for the following parametric function, which defines a trochoidal path:
X(t) = R_cp * cos(Phi_dot * t) + R_t * cos(theta_dot * (-t))
Y(t) = R_cp * sin(Phi_dot * t) + R_t * sin(theta_dot * (-t)) + nu * t
[Click on title to access files]
A MATLAB function to plot the intersection area of multiple circles.
[Click on title to access files]
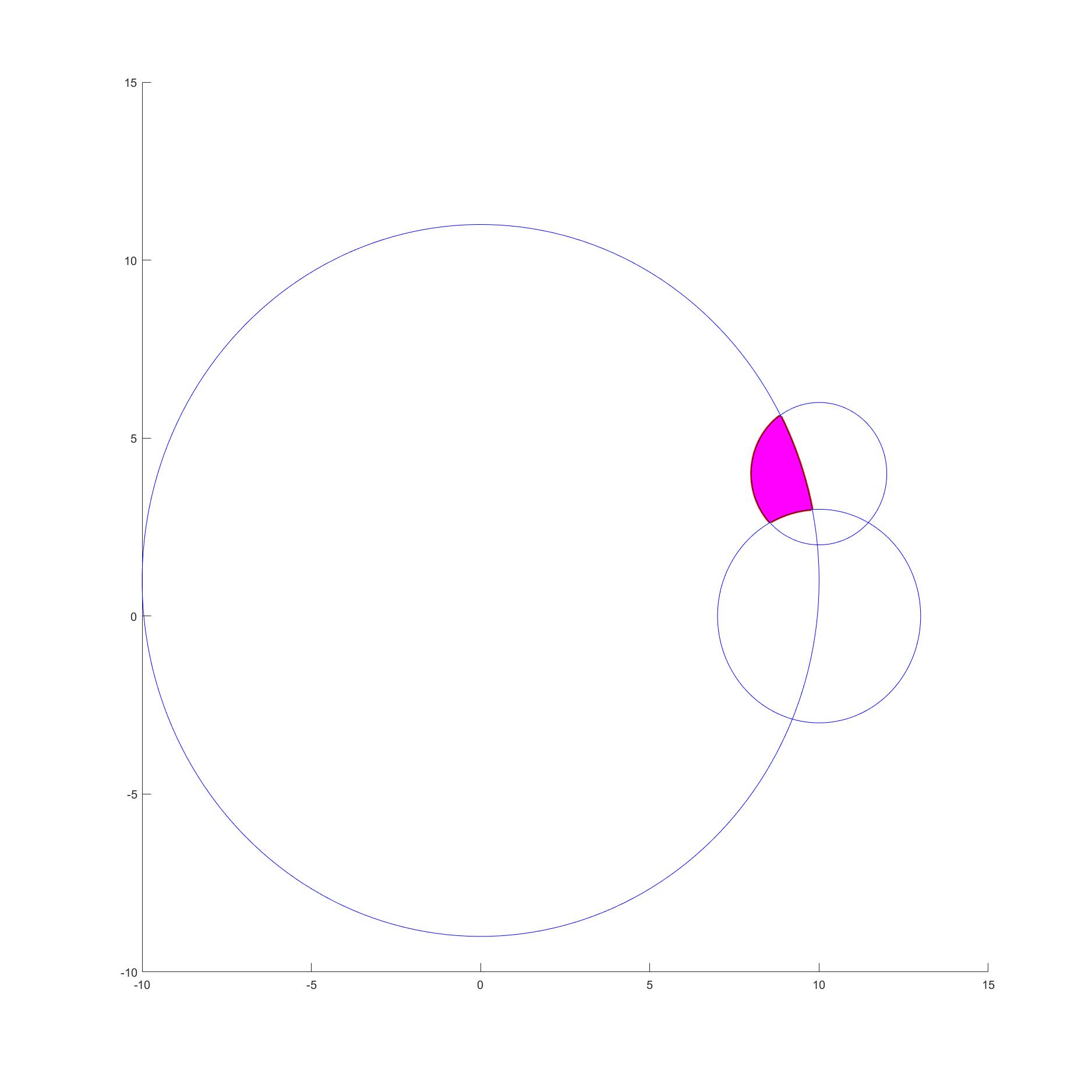
Publications
Journal
Grimm, T., Shaffer, D., Ragai, I. (2020). “Utilization of a Curly Toolpath in Friction Stir Welding,” Advanced Materials Research.
Conference
Parvathy, G., Grimm, T., Mears, L. (2020). “Chipping study of friction element welding,” American Welding Society Education 2020: Virtual Summit.
Grimm, T., Shaffer, D., Ragai, I. (2020). “Investigation of a curly toolpath in friction stir welding,” American Welding Society Education 2020: Virtual Summit.
Deshpande, A., Grimm, T., Mears, L. (2020). “Investigation of thermally assisted friction element welding,” American Welding Society Education 2020: Virtual Summit.
Grimm, T., Mears, L., (2019). “Simulation and Experimental Investigation of Scallop Removal Using Friction Stir Processing and Complex Toolpath,” Proceedings of ASME International Mechanical Engineering Conference and Exposition, Paper No. IMECE2019-11375, Salt Lake City, UT, USA, November 11-14, 2019.
Grimm, T., Kulkarni, S., Mears, L., Mocko, G., (2019). “Experimental Investigation of a Backing Sheet Stiffener in Incremental Forming of Polycarbonate,” Proceedings of ASME International Mechanical Engineering Conference and Exposition, Paper No. IMECE2019-11231, Salt Lake City, UT, USA, November 11-14, 2019.
Grimm, T., Kulkarni, S., Mears, L., Mocko, G., (2019). “Numerical Determination of Unconstrained Area Effect on Springback in Incremental Forming of 5052-H32 Aluminum,” Proceedings of ASME International Mechanical Engineering Conference and Exposition, Paper No. IMECE2019-11255, Salt Lake City, UT, USA, November 11-14, 2019.
Industrial Internships
SKF
Contributed towards qualification of novel material’s use in military-grade bearings
Developed microstructure electroetching method for stainless steel, allowing technicians to more accurately and efficiently determine grain size of material
Investigated anisotropic properties of received metallic material, confirming the existence of carbide banding due to alloy segregation
Impact Guard
Developed work instructions for 5 manufacturing operations
Constructed multiple Excel Userforms in Visual Basic
Integrated control chart feature displays visual aid for go/no go conditions and allows supervisors to monitor process statistics
Investigated improvements to converting processes
Franklin Industries
Worked within multiple constraints to developed a new pass design
New design allows tolerances to be more easily realized, consequently reducing waste material and decreasing production downtime
Created lifter mechanism for punch press, allowing greater automation and increasing safety by replacing manual operations
Compiled a parts list and investigated the cost of converting a tracer lathe to CNC lathe
Designed an improved sensor mechanism for automatic repeater gates